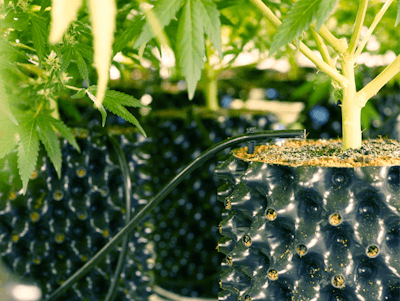
Bigger, better, faster. For many cannabis operations, commercial cultivation meant scaling up small-scale practices, but expansion introduces possibilities for new technologies and a competitive edge.
Advances in growing containers and bench container systems, and production-tested tools from traditional horticulture cultivators provide opportunities for the cannabis industry to enhance productivity and profits.
Nontraditional Growing Containers
Solid plastic nursery pots are containers of choice for many growers. They’re readily available, inexpensive, easily sterilized and reusable, but they have challenges. Solid plastic can limit oxygen flow in growing media, amplify over-watering and encourage circling roots when growing tips hit plastic walls.
Ryan Bradley, founding partner at cannabis consulting and facility build-out specialists Performagrow LLC, says many growers are considering alternatives that capitalize on a natural plant response called “air pruning.” Non-solid, aerated pots allow oxygen flow through container walls. As roots contact high oxygen levels at the pot’s wall and bottom, tips dehydrate. Roots initiate dense, fibrous, lateral growth instead. “Aeration containers are really catching on,” Bradley says.
Traditional horticulture has used aeration containers for decades, but they’re relatively new to cannabis. Extensive research and nursery use show air pruning’s benefits across plant types. Aerated containers encourage smaller root diameter and increased laterals, which means more root surface and nutrient uptake.
“The air pruning allows you to take full advantage of your media and capture that entire volume of media without restriction,” Bradley explains.
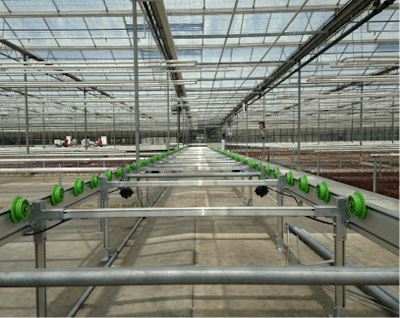
Fabric Aeration Containers
Smart Pots are considered the original fabric container. Products of High Caliper Growing, Inc., their custom-made, U.S.-manufactured geotextile is exclusive to Smart Pots. Charles Jackson, Smart Pots’ vice president of retail sales, stops short of promising specific yields; however, he says a #7 Smart Pot yields the same growth as a standard #10 plastic pot. “Less soil, nutrient and room translates to bigger yields with less expense,” Jackson says.
Recent innovations include the Smart Transplanter, with an overlapping, easy-opening side. “It peels back like a banana and simplifies transplanting when growing from seed or clone,” he says.
Ryan Skinner, head grower at Green Rose Gardens, LLC, uses plastic pots and grow bags for small clones being prepped for their outdoor grow. But he turns to 30-gallon fabric pots for mother plants. “The babies are only in plastic for a short time,” Skinner says. “For our mother plants, the fabric allows for greater airflow through the soil and much better root growth.”
Plastic Aeration Containers
A plastic aeration pot with a long history of success in horticultural institutions is garnering attention in cannabis. Air-Pots, from Scotland’s Caledonian Tree Co. Ltd., are made from recycled plastic, with walls of inward-pointing, solid cones and outward-pointing, open-ended cones.
Garrett Shaw, Air-Pot importer and owner of distributor TerraHydro, credits the Air-Pot system with accelerated air pruning, faster growth, more weight per plant, and higher-quality flower. “If you use the technology properly, you can see productivity increases of 25 to 30 percent, and cut one to two weeks off the growing cycle,” Shaw says. “If you’re paying bills with four cycles, you can potentially get a fifth cycle per year.” The reusable pots last over 20 growing cycles.
The pots also reduce transplanting frequency and alleviate transplant shock, says Shaw. “Instead of two weeks in a 4-inch pot, you can grow four weeks in an Air-Pot propagation cell,” he says.
Bradley notes the simplicity of removing Air-Pots just by undoing a knob, unwrapping the sides, and pulling off the base. “There is no stress to the root ball. It’s ready to jump into that new media,” Bradley says. Wall kits can be customized for communal raised-bed grows, with few size restrictions.
Bradley cautions against attributing yield directly to a container, though. For example, while some growers voice concern that media dries out faster in aeration pots, Bradley emphasizes the opportunity that presents. “When the container is sized properly and you have a tight, well-formed root ball fully maximizing that container volume, over-watering is eliminated. You can capitalize with an aggressive feeding and watering schedule,” Bradley says.
Bench Container System Efficiencies
Without an in-floor system, just getting your crop off the floor and onto benches offers benefits in labor and plant health. Zev Ilovitz, president of greenhouse technology supplier EnviroTech Cultivation Solutions, says industry terminology is not standardized, so exploring options can be confusing at first. It’s important to understand that the “containers” in these bench systems are the pallet-like tables that hold your growing pots. There are three primary options: stationary/fixed tables, roll-top/rolling tables, and mobile container systems.
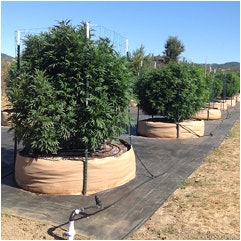
Stationary Table Systems
As the name suggests, stationary tables do not move. Benches are fixed to the ground, with fixed aisles on each side. Bill Bissell, senior process design specialist for horticulture automation company AgriNomix, says benches place plants at an appropriate ergonomic level. Designs can accommodate employee and plant height. “Thirty-inch height is pretty standard. In areas working with young plants at hand level, it might be 36 inches,” Bissell says.
Edwin Hoenderdos, CEO and principal consultant for horticulture automation and logistics company Hove International Inc., notes, “[the] significant gain in fixed benches is the ergonomically friendly work environment. It also allows improved airflow beneath plants, and greater precision and efficiency in irrigation.”
Roll-Top Table Systems
Rolling tables are fixed tables with roll bars added. The supports are stationary, but tables roll side to side. Because tops roll to create aisles, just one aisle allowance – a standard of 16 inches to 18 inches – is needed per bay. The flexible design doesn’t mean a large jump in price, though. “The cost difference between stationary and rolling is minimal,” Ilovitz says.
Hoenderdos estimates rolling benches allow up to 90 percent space utilization versus 60 percent for fixed tables.
While actual layouts affect gains, Bissell says, “You can do the math. If you’re using 5-foot tables, you gain 16 to 18 inches of aisle space per table.”
Mobile Container Systems
Mobile systems have been staples in horticulture for decades. However, Ilovitz says the idea is new in cannabis cultivation. “There’s increasing interest in mobile systems, but a lack of familiarity with cannabis growers,” he says. “When we talk with them about mobile container systems, it is often the first time they’ve looked at it.”
Mobile container systems have palletized table “containers” that move laterally and transfer vertically on a system of pipe rails and conveyors within a greenhouse. Mobile systems can be manual, or partially or fully automated.
“With these systems, labor savings is very significant. There’s a lot of downward price pressure with a commodity crop. High-quality, low-cost production wins. Other growers will be at a competitive disadvantage." — Zev Ilovitz, EnviroTech Cultivation Solutions
“Mobile container systems take plants to people,” Ilovitz explains. “This solves a lot of problems. You significantly reduce labor expense by reducing manual handling. A smoother, more consistent production system is possible, eliminating peaks and valleys in labor, and you improve security by eliminating the necessity of 20 to 30 employees working in sensitive areas. Employees stay in their work area, and the plants come to them.”
Costs vary significantly with the addition of ancillary systems, and prices drop with volume. Bissell estimates that standard containers only, without automation, could run around $7.50 per square foot with mesh-screen container bottoms, and $9.50 per square foot with ebb and flood (also called ebb and flow or flood and drain) containers, used in the process of flooding pots with nutrient solutions and letting them drain into reservoirs.
ROI and Predicted Trends
Variables in cannabis production costs, particularly labor, complicate return-on-investment (ROI) assessments. Mobile systems require larger initial investments, but maximize space utilization and workability. Hoenderdos notes that traditional greenhouse growers often expect four-year ROIs; however, he has heard reports of significantly shorter ROIs on rolling benches and mobile systems for cannabis cultivation.
Ilovitz says he’s seeing more requests for two-level fixed tables, particularly in vegetative areas. He’s also seeing new demand for multilevel roll-top tables and integrated trellis support. “With these systems, labor savings is very significant. There’s a lot of downward price pressure with a commodity crop. High-quality, low-cost production wins,” Ilovitz says. “Other growers will be at a competitive disadvantage.”
Hoenderdos predicts price pressures will popularize greenhouses and automated systems. “Large investors are looking at greenhouse environments to reduce expenses in labor and lighting,” he says.
The pressure for low-cost production pushes investment toward tools and efficiencies, echoing the horticulture industry 30 to 40 years ago, says Bissell. “You have to be lean. Other than protocols, documentation and security, cannabis is no different,” he says. “Adapt what’s been around for decades. Every crop has its recipe. Every grower is a chef.”