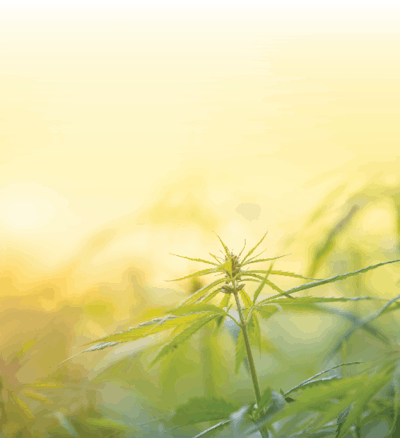
In cannabis cultivation, light is everything. So, it is a good idea to understand what kind of light levels a design will deliver to the plants long before the plans are drawn up.
Designers need to be careful not to save electricity at the expense of yield and profit. The potential annual yield of any greenhouse design is linked closely with the light the design delivers to the plant. Understanding a design’s light performance early in the planning process can help inform expensive decisions and set reasonable expectations for the facility’s performance.
Indoor facilities deliver steady light controlled with an on/off switch. All indoor growers we work with still favor HPS (high-pressure sodium) lights for their flower rooms, and there is ample data that says how much yield those lights produce. But the cost of HPS lighting drives people to consider greenhouses as an alternative.
When considering greenhouses, cultivators need to know how much that greenhouse can produce in comparison to their indoor operation. The answer to that question can be found by looking at photosynthetic light levels in both conditions.
Yield is driven by light, among other key factors; so, all other things being equal, a greenhouse facility that delivers similar light levels as an HPS indoor operation will deliver similar yields and quality.
Greenhouse yield is driven by a combination of sunlight and any supplemental lighting used. To aid in designing an appropriate greenhouse lighting system, we offer a way to model any greenhouse’s yield potential through light levels. The relative amounts of sun- and supplemental-lighting-driven yield determines the greenhouse operation’s overall light cost per gram.
We can look at greenhouse light levels, compare them to the levels in an ideal HPS-driven indoor facility and infer the yield potential of that greenhouse relative to the indoor facility. For this comparison, the light levels delivered to plants in an ideal indoor facility (represented in the charts above) are HPS lamps set at a known distance from the canopy and left on for 12 hours. That light level is measured with a meter, at the known distance, and that measurement becomes a reference point, for which we set the value on the charts as "one."
The charts also show the hourly, natural light levels of a greenhouse design in two different locales and throughout the seasons. Different seasons are represented by different colored blocks and, for comparison, the reference (indoor standard) light level is represented by yellow blocks.
In the left-hand chart, the front row of data (blue) represents the expected natural winter sunlight levels received by plants inside that greenhouse. The second row (green) shows higher spring and fall light levels. The indoor standard is represented by the constant hourly level shown in the third row (yellow), and the back row is light levels on a clear summer day.
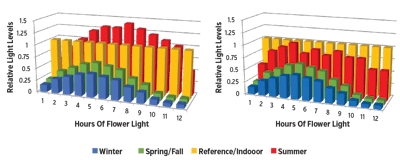
The chart on the right shows a second greenhouse where natural light never exceeds the reference level, suggesting that a greenhouse in this location will likely require supplemental lighting to reach competitive yields.
The only difference in the two charts is that summers at one location deliver more light than at the other. If the other seasonal yields are high enough, the grower with the stronger summer light levels may choose to accept seasonal swings and not to add supplemental light.
On the other hand, the other grower may not be able to produce competitive yields without adding supplemental light. There will be greenhouse locations where the problem is keeping sun out, but the process of estimating yields against an indoor reference remains the same.
The available sunlight numbers allow designers to then determine supplemental lighting needs and estimate the length of time those lights need to be left on to reach specified yield targets.
You can do this by subtracting the natural light level for each hour from the reference level, and then deliver, with supplemental lighting, the difference the following day. Deficits will be different every day, requiring daily monitoring and recalculating of how much supplemental lighting is needed.
Estimating Numbers
The trouble with estimates is coming up with realistic numbers as a base. We suggest you start with getting data for the typical photosynthetic light levels that reach the ground throughout a year at a given location. This data is available from several sources.
Seasonal angle changes are easily obtained for any latitude as well. With that, the designer is faced with translating roof angles, glazing specifications and other design and site information into predicted light levels at various spots in the facility. The high-tech approach to this is light-ray-tracing modeling tools we see used in research. We have not found a commercial ray-tracing tool yet, but growers should be on the lookout for a product, and those inclined might want to look into developing one.
A lower-tech, yet reliable and more feasible approach is using the wealth of data and experience greenhouse suppliers have access to, including recent performance data on cannabis greenhouses. Be sure to account for opaque sidewalls if local regulation requires them for cannabis operations.
Another option designers may wish to try if they can get the data: The percentage of incident light that is captured inside a greenhouse and contributing to heat gain is a good lead on how much photosynthetic light will reach plants in the greenhouse. If the heat gain computation for a greenhouse determines that percentage, that percentage also can be applied to the incident photosynthetic light to get an estimate of the levels the plants will receive for the charts.
Supplemental Lighting
Natural light yield is low-cost yield. When looking at the total natural and supplemental light, the final cost per gram is the average of the cost per grams weighted by the percentage of total yield the two light types contribute.
The relative amounts are determined first by the local incident light levels during the 12-hour flower period and the amount of supplemental light also added during that 12-hour period. Supplemental lighting can be added to deliver even more yield than the reference if environmental systems can handle their heat.
In considering the amount of available sunlight, growers designing greenhouse operations also need to know whether local regulations require opaque sidewalls.
A greenhouse in the Coachella Valley in Southern California will need less supplemental lighting than a facility in Ohio, so each locale needs to be evaluated to understand the true operational and capital costs that should be expected.
If supplemental light is required at all, it is a good idea to replicate an indoor lighting design using the same lamp count, spacing and height above the canopy. This ensures the most intense light-level delivery which limits the time lights need to be on to deliver a given level of catchup light, placing the smallest heat load on the cooling system. Cultivators will likely complain that this is what they were trying to avoid, but competitive volumes are required as well as low costs.
If supplemental lights need to be on for a significant number of hours each day, canopy temperature becomes the limiting factor in hot seasons, so you will need to make sure the cooling system design takes into consideration the lighting heat load and air flows. In winter months, supplemental light could be required for the entire 12 hours of flower light just to keep yields up.
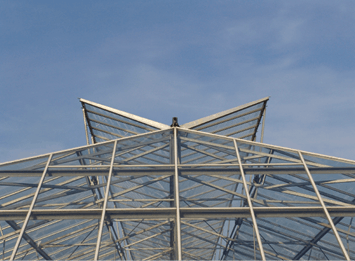
Expect significant seasonal yield swings in greenhouses even when supplementation is used.
A good cannabis greenhouse design should include an emergency heat-dumping scheme, as well. Whether it is by opening typically closed roof vents or bringing emergency cooling online, preventing plant overheating takes precedent over even tight pest management. Heat will surely kill plants, while pests can be marginalized.
An emergency heat-dumping plan is a feature we have not yet seen in practice, but we have seen the need for it.
All in all, growers must deliver competitive yields at increasingly lower costs. Harnessing the sun is one way to achieve those lower costs, but the decision to move to a greenhouse warrants making the effort to collect some data and collaborate with the designer and supplier to eliminate surprises once the money has been spent.