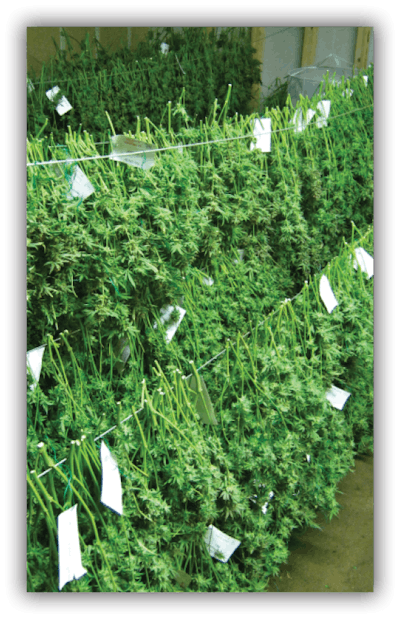
The harvest — something agriculture has experienced since the beginning of time — is the culmination of all of your work in planning, zoning, buying land, obtaining financing, constructing facilities, training staff, acquiring genetics, cloning, vegetative and flowering growth, and countless other activities.
Reaping the fruits (or flowers) of your labor is not an easy process, but rather one fraught with risk, potentially causing high levels of stress if not thoughtfully designed. Poor harvesting techniques may lower the harvest’s quality, which ultimately impacts your financial bottom line and can create potential brand and even industry damage with distribution of low-quality products.
Building efficiency into the physical and logistical details of harvesting plants, manicuring buds, handling raw plant material and storing the final dried and cured product will help you streamline your operation and reduce costs of goods sold. This is essential, since the very nature of a competitive business environment like cannabis shrinks the margin of error for product quality, price and presentation. As the industry scales into a standardized and commercialized agricultural sector, this becomes even more important.
Below are tips to guide you through a successful harvest. These can be used with any form of production, whether outdoor, full-term seasonal greenhouses, hybridized year-round greenhouses, or indoor models. The goal is to help you develop standardized methods for harvesting that result in quality products and a strong bottom line.
Pre-Planning
The planning phase actually starts four to 10 months before harvest, depending upon cultivation methodology, as factors with significant influence on the harvesting process can be controlled by the cultivation schedule. Cultivation schedules must be synced with harvest schedules and cannot operate independently. When discussing initial harvests in a new facility or as an organization scales, we hear far too often: “We’ll cross that bridge when we get there.” Harvest is a bridge that you must design, plan for and construct well ahead of time. Not thinking this through initially will set you up for failure.
Growers create massive harvesting problems and bottlenecks when multiple strains finish simultaneously, creating a deluge of work that cannot be adequately managed. Anticipated finishing times relative to specific genetics allow the harvesting team to make a detailed schedule, so that personnel and material resources can be allocated judiciously.
A similar problem on the opposite end of the spectrum is seen in the downtime created, waiting for too many harvests to come online and wasting retained resources. This is amended by creating crop schedules, staggering batches, and knowing your genetics and how they work with your cultivation methodology to determine when they will be ready for harvest.
On a logistical level, staff need to be equipped with appropriate material and intellectual capital (aka “know-how”) to operate at peak productivity. Standardizing all methods of production for cultivation management, such as growing singular genetics in compartmentalized rooms that can be harvested all at once, is a great example. An operation that has been meticulously overseen prior to harvest will likely result in an approachable and easily managed harvest for all staff levels.
Every aspect of the facility, staffing and operations need to be modeled in standard operating procedures (SOPs) to standardize the entire operation. Often master growers have never had to do this as it was seen as a “paper trail.” If a group does not have SOPs for harvest or the rest of its operations, it should seek professional guidance and work with a firm who specializes in cannabis management and SOPs.
Design
A well-planned cultivation design contains layout attributes to benefit both growing and harvesting operations. Desirable layout needs to incorporate worker flow, cleanliness protocols, and how plants, products and supplies are moved through a facility. Every cultivation facility will be a bit different. However, following lean manufacturing and good agricultural practices, as well as kanban (or queue-limiting) processes, an operation can minimize many risks to its facility before they pose a threat. Most of an operation’s problems derive from poor design and planning. Plant canopy structure must be uniform, allowing standardized harvesting methods to efficiently move through large quantities of material.
How many varieties do you have ready to harvest per week (on average)? How many plants of each variety do you have? What is the typical flowering time? How much space is required for satisfactory drying and trimming?
If you are unable to calculate the volume of buds you anticipate producing, seek guidance from an expert to help you determine adequate sizing of trim rooms, as well as drying, curing, packing and shipping areas. A detailed harvest plan accounting for all resources is highly recommended, especially if this is your first time harvesting a large quantity from either outdoor or large greenhouse production.
Timing
Timing is a critical component to facilitate flow in the planning process. There are many different opinions on when cannabis is ready for harvest. Knowing the varieties you're growing, combined with the optimal CO2 enrichment, nutrient requirements, flushing and lighting conditions for your strains will make it easier for you to determine when to harvest these plants.
If you are unfamiliar with your varieties and this is your first time cultivating them, you will want to meticulously inspect the development and trichomes during maturation to ensure that you do not harvest your plants too early or too late. On an average, by using 12 hours of light and 12 hours of uninterrupted darkness, indica varieties can require up to 60 days of flowering to reach an ideal harvest time. Harvesting kushes and hybrids can require up to 75 days to harvest, and sativas will often take the longest, requiring up to 90 days of flowering. In general, we have observed that indoor producers rarely allow their sativa varieties to mature, often harvesting them 30 days prior to the plants' optimal harvest time.
One of the best and easiest ways to know that your plants are ready for harvest without expensive scientific instruments is to use a hand lens to inspect your trichomes, including their color. It is important to note the difference between trichomes and pistils or calyxes; trichomes grow on calyxes and are the flowering parts of female cannabis plants.
The common knowledge is that if trichomes are clear, they are not ready for harvest. Once they begin to take on a milky color, they are nearing the time to harvest, and if the trichomes start to turn amber or orange, the cannabinoids are degrading. When that happens, your window to secure a quality product is closing, and plants should be harvested as soon as possible. Another option is to bring samples to a testing lab weekly before harvest time. This will allow you to see how your cannabinoids are developing and will help you determine when to harvest.
Material and Personnel Logistics
Managers in charge of harvesting must constantly review key logistical considerations. Ill-prepared operations waste precious time and will cost your company more money than you can likely fathom.
Important questions harvest managers need to ask: Are sufficient supplies for harvesting on hand prior to harvest? Do you have enough containers, drying racks, scissors, rubber gloves and cleaning supplies on hand to adequately process all of your cannabis? If you are considering using a mechanical trimming machine, do you have staff who will be able to operate it? Have you done your homework, looked at trim machine product reviews, and spoken to current users of those instruments to ensure that they work, are easy to clean, and that they produce a high-quality trimmed product?
Is there sufficient internal staff scheduled to accomplish the harvest? Will you be using one of the temporary staffing agencies for the industry to provide trim services? Temporary staffing agencies are becoming increasingly common and are useful to deploy in the right scenario. Staffing firms can be lifesavers for larger commercial operations, to avoid having internal trimming staff on constant payroll. Instead, a contract company is able to bring in the supplemental, well-trained labor only when it is needed.
If you are planning on using a temp trimming agency, the best approach is to have a predesigned standardized operation, so that temps can just “plug” themselves in seamlessly.
While there are many operations who are using temp trim services, there are also examples of cultivators who have had trouble with such services. Some of the trouble we have witnessed is when a grower brings in a trim company last-minute and does not have time to train the trim crew to the specific methods of the operation, often creating points of contention. It can be challenging for a grower to trust someone else to trim his harvest, so often growers will hover over a trim company and smother them, making their work environment more stressful than it needs to be. Communicating and establishing a relationship with a trim company prior to needing them is the best way to minimize these issues.
If problems exist, they should be addressed at the root. While it is easy to blame the temp staff, sometimes the problem is that the operations are so haphazard, no one would do well working under them. Working with the trim company beforehand to go over your harvest plan, to set expectations on how “tight” to trim buds and to determine how they will harvest and trim your plants is vital to successfully outsourcing your trim labor.
A good trim agency will work with your managers prior to the harvest to estimate anticipated yields, schedule when they will bring in workers and how many, as well as create a logistics plan and contingency plan if things change.
Do research in your local market to find quality and compliant trim companies. We have found that with the right training and relationship, they will save your organization time, effort, headaches and, most importantly, money.
The harvest manager is in charge of coordinating all facilities logistics, lining up labor, working with the flower manger and overseeing the harvest, and is responsible for answering the following questions:
- Are you planning on trimming wet or dry?
- How do you address the work environment of the trimmers, taking into consideration lighting, temperature and the spatial environment to maximize trimming efficiency?
- How do you plan to take care of your trimmers? Will you be providing them with food and/or incentivizing high-output trimming?
- How do you plan to track individual trimmer productivity and maintain compliance with state-mandated seed-to-sale tracking programs?
These factors are often overlooked and could create poor rapport among workers, causing management issues that distract from the larger task at hand.
Drying and Storage
Drying and storage require simple, yet refined systems that use physical space and material work flow to produce a high-caliber final product. These spaces need to be designed with optimal temperature and humidity considerations, and controls in mind.
Once cutting down, harvesting and preprocessing is accomplished, it is critical that adequate space has been designated for finalizing the material into a marketable product.
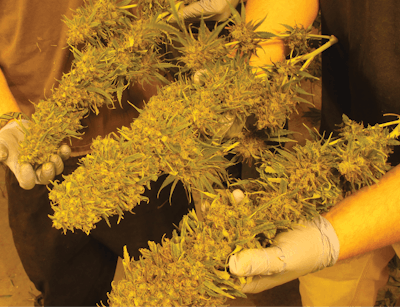
Typically, fresh cannabis contains 70 percent to 80 percent water weight. How do you plan on removing that much water from your drying rooms? When drying cannabis, avoid drying the product too fast or exposing plant material to light, as it will have a harsh taste later. Harvest managers must ensure flow is maintained throughout the drying process by moving harvested material through the system at a standardized rate and system.
Additionally, take the layout of your processing and trimming space into consideration, in order to maximize returns for all components of harvest materials, such as keef and small bud catchment systems.
Ensuring cleanliness of the harvesting facilities is vital and should be routinely cared for by sanitizing the trimming area and tools daily, in order to prevent material from being compromised by molds and to keep products in compliance.
Operations also need an emergency harvest plan in place in case environmental conditions change or there is a biological event, such as mold, that begins to affect your plants.
A good emergency harvest plan will include what to do as a contingency plan for various scenarios. This plan also will include supply lists of everything that needs to be on hand for sanitation, harvesting and preventative equipment, which can be utilized to mitigate the spread of contamination if mold is encountered.
Designing your operation with flow and efficiency in mind facilitates smooth transitions from production bays to product processing, to drying, curing and storage.
Security
Product becomes most vulnerable to theft and tampering after it has been successfully cured and stored. During this time, it is important to anticipate patterns of prospective theft, which is most commonly carried out by employees.
To combat this, minimize personnel that come into contact with stored material and ensure there is a standard protocol for employee culpability. Incorporate transportation manifest logs, and only allow managers to weigh and package large lots. Use sign-off sheets and seed-to-sale tracking systems to cover each step of the process. That way, if there is a problem you can see just where it happened.
Plan on increasing security during large harvests, to ensure that all products are accounted for. Security personnel aren’t there specifically to watch workers, but to ensure operational safety in the increased activity during harvest. However, knowing security is nearby could make workers less likely to attempt to take product. Missing product is not only a detriment to an operation’s revenue generation, but also a dangerous liability issue that could potentially create harsh penalties and even license termination for the producer.
Being Prepared for Success
Harvesting is incredibly important and often underestimated in scope and importance. Utilizing proper planning will increase redundancy and preparedness enabling successful, regular harvests, which will keep your operation running smoothly.
Designing your operation with flow and efficiency in mind facilitates smooth transitions from production bays to product processing, to drying, curing and storage. Accounting for all material logistics well ahead of time enables harvest managers to focus their bandwidth on the task at hand, rather than hitting bottlenecks or distractions during the narrow harvest window.
Products that commercial cultivators bring to market now will determine the public opinion about cannabis and its efficacy, as well as influence future consumer consumption patterns. By investing in your harvest planning and operations, you’re investing in yourself, your brand and the industry's reputation. This isn’t just your job as a producer: It is your responsibility to the industry and your consumers as well. By approaching harvesting properly with planning and standardization in mind, you will set yourself up to reap the “flowers” of your labor for years to come.