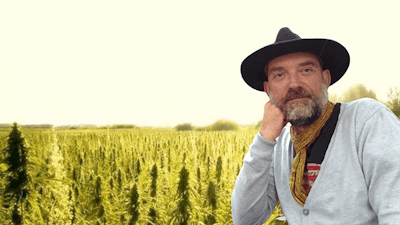
The European Industrial Hemp Association (EIHA) held its annual conference in the virtual space earlier this month, and its innovation award remained a highlight. Three products were chosen as winners this year: Lyohemp knitwear from Sächsisches Textilforschungsinstitut in Germany (third place); a modular, off-grid hemp house from SUNIMPLANT (second place); and Henry’s Hemp Harvester, a double-module front-loaded attachment for harvesting industrial hemp flowers and stems, which earned first place in the competition.
We caught up with Heinrich Wieker, CEO of Henry’s Hemp Harvester in Burgdorf, Germany, to talk about the context around this award and why a piece of harvesting equipment might be so important at this juncture in the global hemp industry.
As EIHA described the machinery: “Four years in research, development and production, the harvester is durable, proven technology that turns out high-quality industrial hemp flowers. The harvester can be driven by a small tractor, has an aluminium frame and rollers for weight reduction, stainless steel parts such as chains and other flower-contacting parts for food- and pharmacy-grade products, hydraulic drives for the main aggregates and an electric scissor-bar.”
Eric Sandy: Can you describe your agricultural background? And what led you to work with hemp crops?
Heinrich Wieker: My professional background is industrial engineering, not agriculture. Maybe it was an advantage and made me think outside the box. I have been working as an automation programmer in oil and gas, nutrition and pharma for over 25 years. I was annoyed with the job and got self-employed with engineering services and hemp machinery. I saw my first hemp harvest in 2015 in the Czech Republic and I was fascinated by the plant and the fact that hemp is the most powerful and at the same time the most discriminated plant on the planet. And while I joined the crew at the laborous work to strip the flowers from the stems, I started imagining how this move could be imitated by a machine, 100 times faster, tea-quality on the field, possible double use of flowers and hurd—and affordable for small farms.
ES: What is the problem that you set out to solve when designing your harvester?
HW: Small farms and extractors face the problem that the harvest is enduring weeks with lots of staff, it's cost-intensive, depends on fair weather conditions while the cannabinoid composition constantly changes during a harvest of weeks. Conventional harvesting strategies and machinery don't work for hemp because of the unique properties of the hemp fiber, and many machines were destroyed at trials with hemp.
ES: Why is it important for harvesters like yours to be mobile and easy to transport? What sort of customers are you targeting with this product?
HW: It is a good advantage. It makes it easier to harvest on different spots, maybe share a machine with others, and also for machine renters it's a cost-effective way to get the machinery from spot to spot. A double module fits on a regular pickup truck and it can be gone 500 miles when the night is done.
My target group is quite a bundle of different interests: beginners, tryers, expanders, extractors, local micro-industries and developing countries. They all can get an affordable tool for acreages up to 100 acres easily with a double module, but up to 500 acres with a six-module setup. But please note that machine is designed for industrial hemp, not bushy CBD- or smokeable outdoor plants.
ES: With the EIHA award, what it is about the hemp market in 2020 that makes your harvester such a critical product?
HW: I think it's the progress that is demanded urgently in our [industrial sector]. Development was lying idle for decades and a lot knowledge and technology is lost. And besides the historical gap, there is the technological gap: There is not much available between sickle bars and a $1-million machine. I also want to support the double use of the plant, that should unveil its potential and it reduces the farmers risk if one product should fail.
ES: What do you hope to see in the hemp fiber market in the next five years? More processing, more growers, international trade?
HW: Actually, I hope to see that hemp products come out of the niche and find a solid position in the market. I will be happy when my machine can help to attract more farmers to feed a growing processing industry. For environmental aspects, I would rather say think global, but produce local. Mass mobility also didn't start with flagships, but with tiny cars that many could afford.
ES: What is something that hemp growers often misunderstand about harvesting? What are they getting wrong?
HW: I could only speak for Germany and I'm not in charge to tell farmers how to do their job. They do well. What I've seen was that some underestimated the properties of the plant and some were enthusiastic with growing and wanted to care for harvesting and purchase later. There is a bundle of strategies including tilling, sowing, fertilizing, harvesting, processing and sales. You should have them all before you buy the seeds. And starting too big.
I think we should all practice to see hemp as an industrial resource that can also produce CBD—but not only.