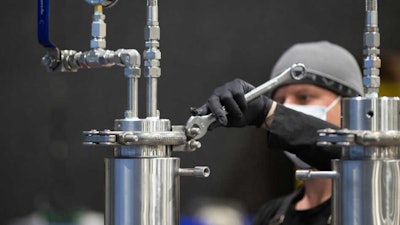
Having a piece of extraction equipment break down can cost your business thousands in manufacturing delays. Especially for companies running extractions en masse, ensuring your equipment is operating at peak performance is crucial to avoid missed sales and prevent production bottlenecks.
Follow these tips from Craig Byrtus, Parts & Service Manager at Vitalis Extraction Technology, to make sure you’re getting the most out of your extractions.
1. Understand OEM maintenance schedule timelines.
While it might sound obvious, reading and following the original equipment manufacturer (OEM) maintenance schedule outlined in the product’s user manual is often the first thing that falls through the cracks with in-house employee training, Byrtus says.
New employees might be trained on “annual” maintenance tasks, but “is that once a year? Is that a specific date?” Byrtus asks. “Annual maintenance for Vitalis usually is a number of hours of run time: 4,160 hours.” That number is derived from an average use of two 8-hour runs per day, five days per week and 52 weeks per year.
“If you have a small facility that only does extractions when biomass comes in or when orders are placed, maybe they're only running one or two extractions per month, so now your annual maintenance is really extended,” Byrtus says, adding that understanding “recommended maintenance intervals is crucial” and that OEMs often will offer on-site trainings (and retrainings) to interested customers.
“I'm not here to just sell you a big box of parts and consumables and supplies,” Byrtus says. “Our goal here with the service department is to keep you running and make your company profitable, because your success is our success.”
By not following OEM maintenance schedules, operators also risk voiding their warranties in the case of system failure, when on-site repairs or replacement are needed, he notes. For example, with co-solvent extraction systems using ethanol, operators must “vent, depressurize, and get the ethanol from the environment before you do any of that maintenance.” And not following outlined maintenance procedures can create avoidable employee safety risks.
2. Identify a team member responsible for scheduled maintenance execution.
Hand-in-hand with following the OEM maintenance schedule, Byrtus encourages customers to identify a specific team member to be accountable for extraction system maintenance.
“I've seen that really fail at a lot of sites where the role is assumed by management to be [decided by] the operators on the floor and none of the operators on the floor want to take that responsibility,” he says. “So it just keeps getting passed along and then nobody is truly accountable for the maintenance of the machine.
“That person should absolutely be really good and diligent at documenting when maintenance is performed—what date, what time, the run-time hours on the machine when it was done. Because if you're on holidays or you have a rotation of staff, they can easily identify what's next, what has to be done, what's already been done. This way you're not changing high-cost filters when you don't have to.”
How maintenance is documented is up to the person responsible. Whether written on a white board, a binder, or stored digitally in a cloud, what is most important is that other team members can easily access the information when they need it.
3. Plan your system downtime.
Some required maintenance can’t just be done at the end of a work day or between extraction runs—they require a day or more of care and repairs. High-throughput operations need to plan that downtime into their production schedules “to allow your production team to get any orders out the door and your purchasing department to order the parts or consumables needed on site” for those repairs, Byrtus says.
Additionally, by “having scheduled maintenance days when you know the system is going to be down, your staff can take a break, and certain individuals can book holidays if they are not needed on-site,” he continues.
Keeping critical spare parts on hand is also a great way to avoid unscheduled downtime, with “critical” varying based on the importance of extraction to the specific operation. “When your lab runs five days a month, maybe you only need $500 or $1,000 worth of a couple key items on your shelf,” Byrtus says. Pump rebuild kits, flow control valves, or pressure relief valves (PRVs) are just a few critical parts important to have on hand at an extraction facility.