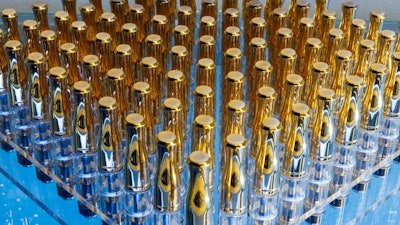
Edgar Candelas remembers the early days in Nevada’s medical market when he spent much of his shift filling vape pen cartridges by hand, using syringes that contained 50 grams of oil at a time and manually capping them. When adult-use sales came online in the state in 2017, Candelas had to ramp up production quickly to meet the nearly overnight demand.
Eight years later, as the lab director for a cultivator and processor producing products for Ohio’s medical patients, Candelas says operations have become much more efficient thanks to new technology available. But he is always looking for ways to improve extraction methods and further dial in infused product creation, and he’s applying what he learned in Nevada and before that, California, to his role in the Midwest.
Candelas shares two tips for how cannabis companies can optimize this process to save time and money, all while reducing human error and producing high-quality products.
1. Examine how product mix changes and minor updates impact overall production.
After the cultivation team harvests plants to make high-quality live resin products like sugar, shatter, batter, crumble and terp sauce, some of the harvest is reserved and frozen fresh rather than journeying through the typical two-week drying and curing process, which saves time and facility space while also adding variety to the product mix, Candelas says.
Minor changes have had major impacts, too. Once cannabis destined for extraction is harvested, the material is stored in vacuum-sealed bags that are shaped like banking machine tubes to better fit the shape of the company’s butane extraction vessel and save time on the loading process, Candelas says. The packaging also means employees do not have to break up the flower before it goes into the machine, which can degrade the product.
“The industry has really had to evolve from the time ... when there was no [educational support] for the industry,” he says. “We’ve improved upon that. But any time there is so much unknown, whatever human error you can eliminate is good.”
2. Explore options for automating vape cartridge filling and capping.
When Candelas first joined the Ohio team, the company used vape cartridge filling equipment that allowed one employee to fill and prep one cartridge at a time, precisely loading the vial, and producing on average 100 cartridges per hour. It saved time compared to the handheld syringe system, but it wasn’t keeping up with dispensary demand, Candelas says.
In response, the company upgraded to vape cartridge filling machines that allow an employee to place 50 carts on a plate, filling all at once, which ramped up production to 500 cartridges per hour. The move has had a positive impact on everything from efficiency to sales and allowed the company to maximize output without hiring an additional person. Candelas says they have produced upwards of 8,000 cartridges in one day.
Relatedly, cap placement is automated so that employees don’t have to twist or push them by hand.
“The filling machine is one of the most significant upgrades for productivity that we’ve had in this building,” Candelas says, noting that it saves on staff costs and employees’ time. Plus, it allows them to provide dispensary clients with quicker turnarounds. “Having the automatic filler cuts about a week’s worth of lead time on our orders.”
Cartridges produced by the team are between 300 milligrams and 842 milligrams. Traditional 1-gram cartridges of more potent cultivars would surpass Ohio’s daily THC potency dose limit, so being precise is about efficiency as much as it is about compliance.
“It’s barely shy of a gram, so it’s super important for us to have a machine to get that level of accuracy,” Candelas says.