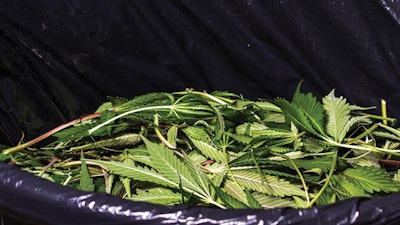
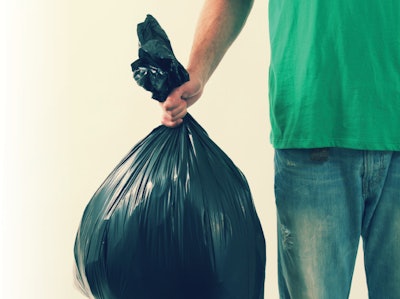
As of late, when I scroll through social media, I’ve seen posts displaying beautiful, golden, creamy extraction filtrates that contain lipids, fats and wax combined with traces of cannabinoids and terpenes. Winterization, inline de-waxing apparatuses, media filters and thin-film extraction processes, among other things, all produce these filtrates.
Often accompanying these posts are questions I’ve been asking myself: What can be done with all the cannabis and hemp extraction byproduct? What current and future uses are possible for their biomass, from pulp to fiber?
Hemp Today
The cannabis byproduct processing industry is in its infancy, mostly because prohibition prevented mass production of hemp-based products for decades, resulting in most hemp-related manufacturing technologies of old getting lost to time. And despite the business potential, many states established regulations for the production or extraction of cannabis and/or hemp that often prevent a cultivation or extraction company from using or selling waste for byproduct use.
As such, nearly all hemp manufacturing today occurs in foreign countries that have lower production costs. HempFlax, a company with operations in the Netherlands, Germany and Romania, for example, produces “raw materials, semi-finished and finished products based on environmentally friendly grown hemp,” according to its website. Listed applications include: construction, animal care, horticulture and nutraceuticals, among others. The company’s operations have grown from 140 hectares of hemp cultivation in 1994 to a projected 3,500 hectares in 2020, indicating a growing demand for the entire cannabis plant, not just its flowers and oils.
In North America, there has been a renewed interest in hemp production and manufacturing of hemp-derived products both before and after the recent passage of the 2018 Farm Bill (which once again legalized the commercial cultivation and processing of hemp). Companies such as Green Heffa Farms and the Colorado Hemp Project are at the forefront of encouraging hemp farming in the U.S. and are reinvigorating interest in a multitude of uses for hemp byproducts. The Colorado Hemp Project also is credited with harvesting the first legal hemp crop in the U.S. in modern times and serves as an educational research center focused on reinvigorating the hemp industry with respect to hemp building materials (such as Hempcrete) in a sustainable fashion.
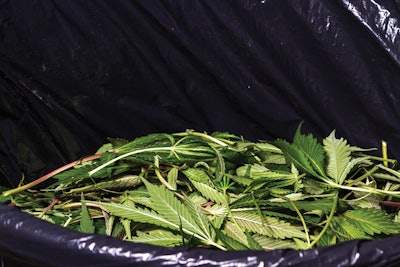
Hemp Tomorrow
Looking at the progress, albeit slow, in today’s hemp market, I ask myself how on earth will byproducts and waste byproducts be utilized and transformed into something useful or profitable considering current restraints, such as the lack of existing infrastructure to collect and process byproducts?
Perhaps, in the beginning, it will be a cottage industry with a very small number of local operators willing to explore different byproduct opportunities. From there, it could evolve into a co-op situation in which producers of a given byproduct, whether it be fiber, pulp, seed, wax or fats, can deliver the products to the co-op instead of the landfill. That co-op might then utilize that byproduct to mass produce a given product.
This seems like the best model to follow to get this industry off the ground because many small facilities manufacturing the same product is unfeasible and inefficient. For example, I see no need to have multiple Hempcrete manufacturing facilities in one geographic location; why have a bunch of companies produce small batches of brick when it is common sense to have one large brick manufacturing center?
Such co-op models exist in other industries, such as the Italian olive oil industry. In many small towns in Italy, an olive oil co-op might operate the one grinding wheel and olive oil press in the town, and anyone who has olives that need pressing can bring them to the co-op where they are combined, ground and pressed together. Each olive producer then receives a share of the final oil’s profit based on the amount of olives they contributed. This way, each family doesn’t have to have a grinding wheel, press and an area to perform the process and instead shares costs with other small producers.
Perhaps a new company will perform a feasibility study projecting the possibilities of a given cannabis or hemp byproduct and create the required infrastructure to transport the byproduct to a manufacturing facility to be processed or manufactured into a profitable product or revenue stream. There is no doubt that, in the very near future, there will be an insurmountable amount of cannabis waste available, especially when the lion’s share of hemp will be destined for extraction to produce CBD, resulting in metric tons of wasted biomass in the form of ground-up plant material. It would be an avoidable environmental disaster for that biomass to simply go to a landfill.
Current uses for that extracted biomass are many. Among other things, you could create:
- Hempcrete, i.e., concrete manufactured utilizing hemp, for products such as bricks or utilized in the same fashion as concrete
- Fiber board/hemp plywood utilized as a plywood substitute
- Fiber for a multitude of industrial uses—from construction to insulation.
- Hemp seed oil
- Hemp paper (e.g., rolling papers)
- De-hulled hemp seed/nut for food products
- Seed for bird food
Looking at future use, possibilities are endless:
- Cellulose: isolation for potential plastic manufacturing for cannabis packaging
- Hemp cardboard for cannabis packaging
- Lipids, fats and wax for salves, creams and lip balm
- Waste ethanol for potential redistillation
- Fuel, including ethanol
- Soil amendment
- Pet products for both wellness and as bedding
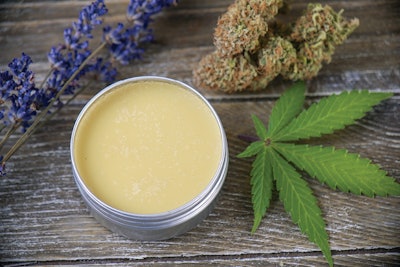
Waste Beyond Biomass
Regulators also often consider the growing media and soil used in cannabis and/or hemp production to be a waste byproduct. When that is the case, regulations often require that the soil or growing media be destroyed at the end of the cultivation cycle. During one client visit, I saw a dumpster full of root balls and soil from a recent harvest and asked how much money they spent per month on soil and amendments. The answer: $9,000.
I realized this was simply one facility of literally thousands, a significant portion of which simply dispose of the media after each harvest, and in some states are legally prevented from giving away or donating the soil to, say, a community garden. As such, some of the most valuable soil on Earth, which has been utilized for only approximately 90 days, is headed to landfills across the U.S.
The main reasons for disposing of the soil in this way are: to minimize the risk of infection from pests or diseases caused by recycling soil, by not properly composting used soil or simply due to a lack of space to compost and sterilize large amounts of soil.
This situation made me wonder: If legally allowed, could a company survive and profit by simply arranging to pick up waste soil from growers each month (perhaps an eco-conscious cultivation company would even pay for soil disposal diversion from a landfill), and then resell that soil once it has been put through a chipper/shredder (to break up the root system and homogenize the soil) and recomposted? Once properly composted and homogenized, the soil could be re-bagged and made available for sale to the existing landscaping industry for half the original cost, if desired, to be competitive in the market.
Imagine if a soil reuse company had 100 clients that paid $1,000 per month to have its waste soil picked up and diverted from landfill and reused, which would be a very environmentally friendly thing for a company to do.
A basic breakdown reveals incredible possibilities and potential:
- 100 clients pay $1,000 per month to have waste soil disposed of once a month for 12 months, which totals $1.2 million per year. Even if the service costs $500 per month ($600,000 a year for 100 clients), it remains intriguing.
- If a soil reuse company were to collect $9,000 worth of soil from 100 clients each month and resell it for half the value, sales would total $5.4 million for the year.
- The combined revenue of both the soil diversion service and the soil resale is $6 million to $6.6 million. This does not include all associated ancillary costs— i.e., property to recycle soil on, wood chipper or grinder, compost capabilities, trucks to haul soil, equipment to bag and palletize the bags of a soil for shipping, etc.
Even if one sold the soil for half value, charged half for soil pickup or transportation and paid $1 million on infrastructure, there is still amazing profit potential, all on 100 clients. Imagine the possibilities of a franchise that performed this service in each legal production state? Sounds like an amazing opportunity in the cannabis industry without the associated headaches caused by onerous regulatory oversight—simply play in the dirt all day and pay taxes at year’s end like normal people? Doesn’t sound very stressful to me.
The main takeaway here is that cannabis production does not have to be a wasteful industry if it chooses not to. Besides the byproduct waste that exists, the disposal of vape carts and vape batteries and the triple packaging required to sell cannabis all add up to be an environmental disaster that need not exist in the first place. Henry Ford demonstrated that plastics can be made from hemp and other plant sources decades ago. How much plastic used by the cannabis industry can be made from the very products those packages hold?