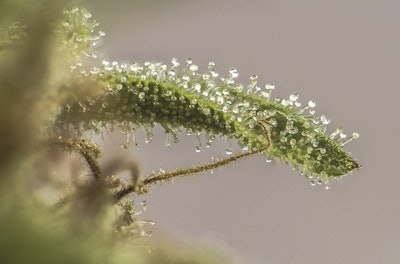
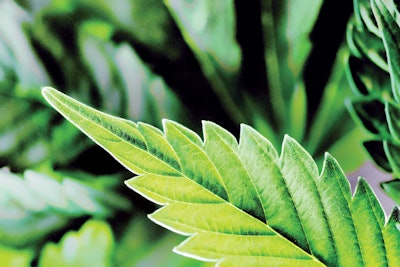
Recently, I consulted for a cannabis operator that was producing 2 acres of greenhouse-grown cannabis. I had worked with this client before, helping them set up their indoor cultivation operation and processing lab. In the time since, this company partnered with a nearby farm and expanded into half of a 4-acre greenhouse.
But the team did not have the systems in place to efficiently process 2 acres worth of cannabis, so they called me to figure out how to harvest thousands of plants (of multiple cultivars) without compromising quality, and to do it efficiently with the minimum amount of labor, product drying, curing and transport required.
Here are 12 tips that I offered to this group to help them tackle a large harvest quickly and efficiently during my two-day facility assessment visit.
1. Let sales guide your decisions.
I explained that having a game plan for what the cannabis products will ultimately be grown for is the first requirement when planning a harvest. They needed to know how much of their crop is destined for flower sales and how much would be processed into extracts.
For example, if only 10 percent or 20 percent of a cultivation operation’s top-quality flowers is to be dried, cured and hand-trimmed, and the remaining product set to be extracted into various concentrate forms, that will affect everything from extraction methods to transportation.
In this case, the majority of the non-flower end product was to be created through fresh-frozen extraction, which involves taking the buds straight off the vine and freezing them without drying. (Drying destroys up to 40 percent of terpenes.)
2. Move plants, not people.
The goal is to prep all the products for extraction as quickly and efficiently as possible. In this case, we used human labor combined with machinery—more specifically, conveyor belts—to eliminate unnecessary human traffic and reduce time spent on mundane tasks. A 10-minute walk across the facility and another 10-minute walk back can add up, and that is a poor utilization of time and resources.
Conveyor belts move product more efficiently than humans. Some situations are not designed for conveyor belts (e.g., grows with narrow halls, many turns, odd angles), but they should be employed whenever possible. The equipment is fairly expensive, but there may be options to rent the equipment so that you can experiment with layout, workflow and see if it fits or is advantageous before you purchase.
3. Start an assembly line.
The layout of the facility at which I was consulting was perfect for an assembly line harvest: it had long corridors with little to no twists and turns. I recommended they set up a team of five to remove the fan leaves of all the plants while they were still in their pots. Anything without resin glands on it should be removed, as they contain little to no active ingredients (cannabinoids and terpenes).
After de-leafing, I advised that another team of five should remove all branches containing buds and place those branches into a bin. Once the bin is full, workers can put the branches onto a conveyor. It is much more efficient to move the product from one station to another via conveyor belts than it is to have humans walking buckets back and forth.
4. Automate stripping.
I also advised they set up the assembly line so that the de-leafed branches travel to a separate work station, where five more workers could strip the buds from the branches utilizing a bucking machine. (A bucking machine accelerates stripping buds from branches by drawing in the stalks through different-sized holes, leaving the stripped buds to fall into a bin.) When the bin is full, the worker can place it onto another conveyor belt.
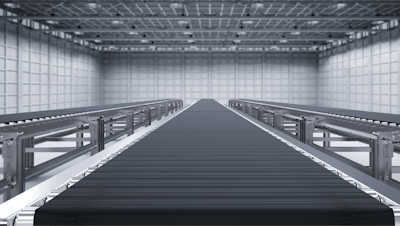
5. Sort product on the line.
From there, the stripped buds travel to a sorting table where any material that does not contain resin glands is discarded, and quality control processes are performed by another team of five. These processes include looking for any signs of pest and disease. During sorting, large buds can be broken down further into smaller buds and unnecessary stems removed.
6. Plan for extraction methods early.
Once sorted, there are multiple options for what to do with the separated buds—it all depends on the final concentrate desired. Product destined for distillation via CO2 or ethanol extraction is typically dried prior to extraction, as terpene preservation is not paramount. This means you must have racks ready in a suitable drying environment (roughly 65 degrees Fahrenheit to 70 degrees Fahrenheit, and humidity levels of approximately 45 percent to 50 percent). This operation had adequate space and conditions for drying product in the form of retrofitted semi-tractor trailers.
Conversely, if the desire is to utilize cannabis for hydrocarbon extraction with a focus on terpene preservation (as in this case), the cannabis should be frozen fresh, not dried.
7. Utilize nitrogen freezing tunnels.
As this group was looking to freeze large amounts of cannabis quickly for hydrocarbon extraction, I advised they use a freezing tunnel: a covered conveyor belt system that flash- freezes the cannabis by utilizing liquid nitrogen.
As the cannabis passes through the freezing tunnel, liquid nitrogen solidifies all water, fats and waxes within the material and eliminates the odor and flavor of chlorophyll (i.e., wet plant). This is a superior method to placing fresh, harvested material into a freezer and letting it freeze slowly over a period of hours, which causes concentrates to have a higher level of undesirable compounds (e.g., chlorophyll).
Freezing tunnels come in a large variety of sizes and prices. For large-scale applications, it’s best to search scientific and manufacturing auction sites (LabX.com, BioSurplus.com, or any other clearinghouse sites), where freezing tunnels are more affordable.
Once the freshly harvested cannabis is thoroughly frozen, the available terpenes evaporate more slowly, resulting in an extract that has monoterpene levels much higher than extracts made from dry cannabis. At this point, the fresh frozen cannabis is in a perfect state for hydrocarbon extraction. The resulting extract can be processed into many forms ranging from shatter, budder, wax and others. As of late, the focus of live resin extractors is the production of raw terpene-rich extracts (also called “sauce”). That sauce can be classified as HTFSE (high-terpene full-spectrum extract) or HCFSE (high- cannabinoid full-spectrum extract). Sauce can also be utilized to produce crystallized THCA, while other extractors focus on products containing select terpenes or cannabinoids. Flash-freezing allows extractors to specifically focus on THCA production, as some other methods of extraction only produce decarboxylated THC.
8. Store for safekeeping.
The flash-frozen cannabis can also be properly dried later for CO2 extraction, or even utilized frozen or dry for ethanol extraction (although a percentage of the preserved monoterpenes would be lost in the drying process).
9. Transport biomass using subzero trucks and freezers.
Once we figured out how to best process the 2 acres of harvested cannabis, it was time to determine how to transport it. One transportation option is to use a diesel truck (or several, depending on the volume) with subzero trailers for the frozen product, as well as another diesel truck with a basic refrigerated trailer for the dry product. Once at the destination, a large subzero freezer is necessary to store the material until it can be extracted. Large and small walk-in freezers can be rented for short-term use.
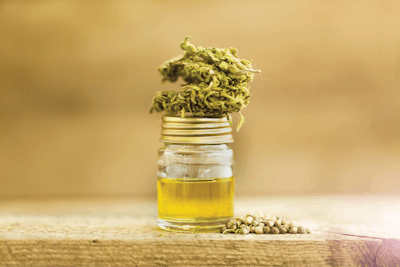
10. Extract the active ingredients before transporting.
As this group had its own lab, I advised them to remove the active ingredients from the biomass (the vegetative material) before transporting it, as it has no real use at this time. This method’s main advantage is that you minimize both transportation cost and storage cost. Look at it this way: It is far more economical to transport a few kilos of raw resin than hundreds of pounds of bulk plant material, and it is much easier to store that amount of raw resin compared to that amount of frozen bulk plant material.
Since we opted in this project to extract the active ingredients before transporting, we were left to determine how to efficiently remove the active ingredients from the biomass. We discussed a couple of methods currently commercially available: a basic dry sieve or scaled water-extraction technologies.
11. Use dry-sieving to collect all active ingredients.
Industrial sieving apparatuses are readily available in many sizes and configurations, from rotating drum separators that employ dry ice to maintain frozen conditions in subzero environment conditions, to particulate separators utilized in industrial applications. Both are capable of dry-sieving and separating all active ingredients from the biomass.
12. Use water-extraction if you plan on distilling your extract.
Currently available large-scale water extraction apparatuses utilize multiple screen sizes to separate various-sized resin glands and separate the resin glands from the biomass, but many water-soluble terpenes dissolve in the water and are lost. Therefore, water-extracted resin glands have fewer available terpenes. This may not matter to someone intending to distill the cannabinoids in the end.
These aren’t the only methods to extract active ingredients, however. Many industries have been producing flavor and fragrance compounds and oils for decades (and still are). There is a lot to learn from those industries with respect to the equipment and methods they employ to achieve commercial scale production of essential oils, flavors and fragrance. I predict we will soon begin to see those industrial applications employed in the cannabis industry.
Kenneth Morrow is an author, consultant and owner of Trichome Technologies™. Facebook: TrichomeTechnologies Instagram: Trichome Technologies [email protected]