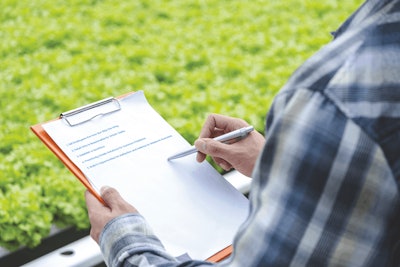
Cultivating cannabis requires multiple standard operating procedures (SOPS) to ensure healthy plants produce consistent products. Nutrition, environmental control parameters and pest scouting programs, among many others, all need SOPs.
Often compared to checklists and scripts, good SOPs not only provide helpful guidelines for teams, but they also direct workflow, keep people accountable and have systems for measuring how people and the business are performing. Especially in a high turnover labor market, ensuring consistency and preventing errors is a challenge that SOPs are especially well-designed to meet.
Here are some of the top tips for establishing or improving SOPs:
1. Tell Employees the How But Skip the Why.
SOPs are about how things are done, not why they are done. Resist the temptation to add explanatory text to them; put that information in your training package, along with your SOPs. The goal of new hire training is to make employees productive as quickly as possible. That is achieved by teaching them how to do their daily jobs to the letter.
2. Detail Who is Responsible for Which Tasks.
Often, the first SOP is one that includes roles and responsibilities. When you identify a clear set of requirements, responsibilities and performance metrics, it’s difficult for staff to argue that they didn’t know the chain of command or who was responsible for what. When everyone knows who does what task, operations go smoothly.
3. Establish a Workflow.
The foundation of a good SOP is workflow and a schedule because they describe what plants move from where, to where, when and by whom. Workflows also outline all of the tasks involved in growing plants.
4. Proactively Create Solutions for Common Problems.
The bulk of an SOP package is made up of task descriptions identified in the workflow, such as: take cuttings, sanitize trays, perform apical pinch and assign work schedules. Understanding each step in these tasks as well as how to control the variables in them is the foundation for developing an effective SOP.
Look at all the moving parts (variables) inside a task and ask of each, “What if it slows down, wobbles or stops … what happens to the output?” If you don’t like the answer you come up with, that is a part you need to pay attention to and manage. Figure out what needs to be done and document those steps in the SOP.
Remember to include regulations and worker-safety tasks in your SOPs; they move, too.
5. Build in Opportunities for Reflection and Metrics to Measure Success.
SOPs need to produce information to answer the question: How are things going? The number of cuttings of each cultivar shipped from the propagation room this week is a performance metric that provides a clear-eyed view of how that propagation room is performing. Additional metrics, like the number of pests found on cuttings, provide more insight. In aggregate, metrics paint a picture of operational health, and they also provide the explanation behind why the picture looks the way it does.
Read the Cultivation Startup & Expansion Guide