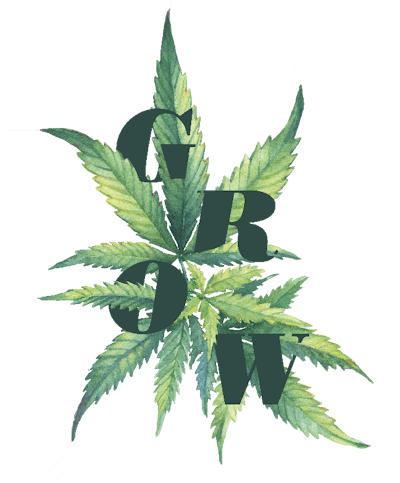
More and more cultivators are going vertical, but the vast majority of grows are still built on a single level, giving a slight mystique to the idea of building up and not over. As Justin Clapick, head cultivator at Deschutes Growery, puts it, “It’s like 95 percent of people are doing it the old way, and so there aren’t a lot of people talking about growing vertically.” But Cannabis Business Times is pulling back the vertical-growing curtain, with three head cultivators sharing details on their growing operations and offering advice on how you can go vertical, too.
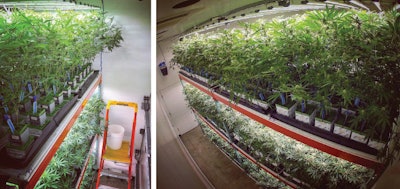
Paul Disdier, Head Cultivator, The Fireweed Factory
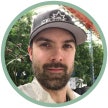
At the Fireweed Factory in Juneau, Alaska, growers cultivate some 40 strains of cannabis—classics such as Blue Dream, Bubba Kush, Green Crack and GG4, plus original varieties such as Strawberry Rhubarb, Chinookie Cookies and Blue Totem—in two vertical flowering rooms that span 192 square feet each, with vertical racks that take up no more than 62 square feet of floor space, says head cultivator Paul Disdier. For a cultivator working in condensed and expensive warehouse space, maximizing every inch matters, Disdier explains.
“We decided to go vertical from the very beginning,” Disdier tells Cannabis Business Times. Not only was the cost-savings obvious, but warehouse space is hard to find in Juneau, he says, and because of that, the Fireweed Factory knew it had to make the most of what it had. “We got lucky and found a warehouse with high enough ceilings to let us have three growing levels,” Disdier describes. What’s more, “the warehouse was an empty shell, so we were able to design our grow rooms around the vertical rack system we wanted to use.”
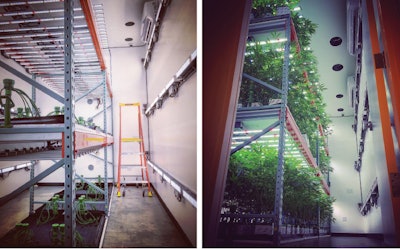
That system is composed of three vertical tiers, each 4 feet high. On each level, you’ll find four Fluence SPYDRx Plus LED lights. “We went with three tiers because we feel it is the sweet spot for efficiency and workflow,” Disdier says. “We use rolling podium step ladders to access the third level—anything higher would make the workflow a lot more difficult.”
The Fireweed Factory’s automated controls are what Disdier describes as standard, and similar to what you might find in a non-vertical growing space—including an automated watering system as well as “a Bluetooth-enabled irrigation controller that is connected to Floraflex solenoids that feed our plants from a cone bottom tank,” Disdier says.
But, Disdier admits, designing the company’s grow rooms was—despite all its benefits—actually a challenge. “We wanted maximum efficiency, but also a design that still allowed for an easy workflow,” Disdier says. “We had to come up with some outside-the-box solutions to make our design work.” For example, Disdier says, “all of our air circulation fans are mounted externally and ducted into the rooms. We basically took all of the mechanical equipment out of the room to create the space needed to move ladders around the racks.”
And yet, Disdier says it was all worth it. “For us, going vertical was a way to compete with larger operations by maximizing our efficiency and keeping our costs low,” Disdier explains. “Instead of trying to compete by using economies of scale, we use efficiency. This enables us to operate on a smaller scale and focus more on producing a quality product.”
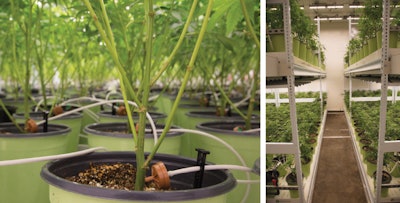
JAMES CUNNINGHAM, Head Cultivator, FOG CITY FARMS
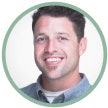
Fog City Farms didn’t start vertically. But, James Cunningham, the farm’s head cultivator, says, “like many other people in the industry, we have been watching LED technology evolve over the years. We … were unsure that [with LEDs] we could attain the quality levels that we were accustomed to producing under HID lighting.” That worry was assuaged “after touring cultivation facilities in Washington [state] with [our lighting company],” says Cunningham, who adds, “[I] saw the quality I needed to see … to be convinced that LED was the way to go.” He went back to make a change.
“At the time, we had already designed our facility around HID growing technology, and we were very pleased to realize that switching to a two-tier mobile racking system would not require additional HVAC or electrical upgrade—while doubling our production per square foot based on a yield of 1.25 grams per watt,” Cunningham says. Today, he says, the facility uses its two-tier racking system “in our flower rooms, which is a result of the ceiling height in our building. Starting with a two-tier system has allowed us to learn the growing platform and develop the very best practices for this vertical growing system.”
In its 5,000-square-foot facility with the vertical grow system in Santa Cruz County, Calif., Fog City Farms grows a variety of strains, including “a handful of strains that have been bred between Santa Cruz and Maui,” Cunningham says. The facility “serves as a model for everything we are developing and utilizes the latest technology in vertical farming,” he says. Plus, “our canopy is growing to more than 35,000 square feet of indoor cultivation space throughout the greater Bay Area,” with plans to be operational in additional spaces by next year. Fog City Farms is developing a 23,000-square-foot facility in Soquel, which could open as early as the beginning of 2019, and is developing additional properties in Santa Cruz and possibly San Jose, which don’t yet have launch dates, Cunningham says.
Pipp Mobile engineered the racking system for Fog City Farms, Cunningham says. “We developed an air circulation and filtration solution, and Pipp was able to re-construct their vertical supports in order to meet our needs,” he explains. “We worked side-by-side with them in developing a rack that would be more functional for me as a grower.” Because line of sight was important to Cunningham, “Pipp re-engineered one of their racking systems to allow me to have unimpeded sight front-to-back in our grow rooms,” he adds.
Of course, that kind of customization came at a price. “The most obvious obstacle in vertical farming is the upfront investment,” Cunningham says. That doesn’t mean it’s not worth it, though. “The equipment is expensive, but as the industry grows, we will need to maintain a level of efficiency in order to stay profitable,” he explains. “The ROI with this platform comes in the increased and consistent production using less power” thanks to LED lights, and a more efficient HVAC system. “You can cool double the lights with the same HVAC system you would design for a 1,000-watt HPS system,” Cunningham says.
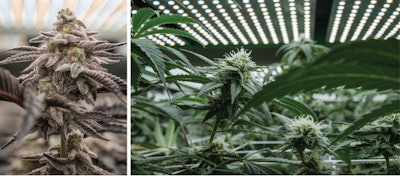
JUSTIN CLAPICK, Head Cultivator, DESCHUTES GROWERY

Deschutes Growery in Bend, Ore., went vertical a little more than a year ago, says head cultivator Justin Clapick, and in many ways, the cultivation operation is still trying to figure out what works vertically and what doesn’t. “When you’re growing vertically, you kind of have a lot of decisions to make in terms of what [strains] work better,” Clapick says. With vertical systems’ fixed height and the intensity of its lights, it takes a lot of tailoring to optimize the plants’ potential, he explains. Deschutes’ MAC, Ghost Cookie, Orange Sherbet and Meat Breath—among many other varieties of strains—have done well in the last year, he says.
Deschutes Growery went vertical, Clapick says, because “we had a fixed amount of square footage in our commercial warehouse—so we were forced to innovate because we were restricted by how much square footage we could get for growing,” he explains. Now, the operation has 10,000 square feet of flowering canopy on four tiers, occupying just 2,500 square feet of floor space.
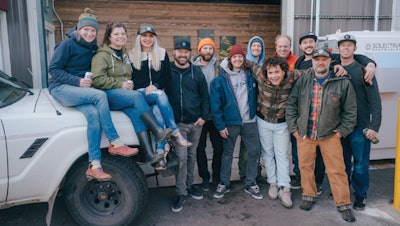
Despite its high-tech vertical system, Deschutes Growery still hand-waters everything, says Clapick, who adds that vertical growing offers an advantage in that process as well: “There’s less walking to water,” he laughs. Deschutes Growery still hand-waters its plants “to ensure all the plants get watered according to their unique needs,” Clapick says. “Different genetics demand unique amounts of water and with a room that has upwards of 10 cultivars, we wanted to be more exact with our water dosing.” Growers reach the three highest levels and back rows with the aid of a ladder, Clapick says.
Because Deschutes did not begin as a vertical grower, one of its challenges has been finding a way to integrate its new growing methods and strains with its “old” way of doing things, says Clapick. From its air system to how to light each of the tiers, “we had to rethink everything,” Clapick explains. “When you’re doing something new and you don’t always know the outcome—when you’re changing a business model at the same time you’re changing grow methods—you have to find a way to … make a leap into the new world without dropping the past,” Clapick explains.
To handle pests and bugs on a vertical scale, Deschutes Growery uses “beneficial bugs to combat bad bugs,” Clapick says. “This starts really early on in the clone stage … so that when our plants are ready to move into their final flower rooms we’ve got a head-start.” The growery continues to use “good bugs” throughout the flower cycle, as well as “nematodes in our soil to help combat prey like fungus gnats,” Clapick explains. “Because we recycle our soil in a no-till format, it’s more likely that bugs will be present. IPM is critical.”