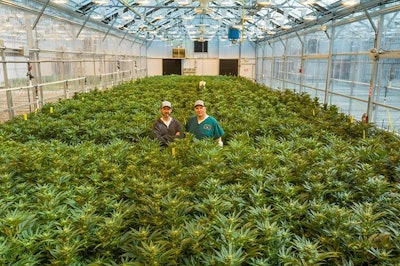
_fmt.png?auto=format%2Ccompress&fit=max&q=70&w=400)
Silicon Valley may be the undisputed capital of the tech world, but that wasn’t always the case. For decades, much of the world’s tech-startup and venture-capital activity occurred in quaint suburban office parks and low-rise office buildings along the Route 128 Beltway outside Boston. Early computer pioneers Digital Equipment Corp., Data General, and Wang Laboratories formed a “Technology Corridor” along Route 128 and made Boston a beacon of innovation in a digitizing world.
Though Silicon Valley raced ahead and ultimately won the battle for regional tech supremacy, Greater Boston is still a formidable tech hub in its own right, with influential research institutions, tech-focused venture capitalists, universities, and innovation centers. Tech companies such as Hubspot, TripAdvisor, and Dell EMC are based there, and Facebook, Twitter, and IBM have offices in the Boston metro area to take advantage of the local tech talent and innovative culture.
So, could Greater Boston become the next hub for technological innovation in cannabis?
That is one hope for the Massachusetts Cannabis Center (MCC), a purpose-built, tech-driven, eco-friendly cultivation and processing facility situated on a 52-acre parcel of land in Freetown, Mass., about an hour drive from Boston proper. The center is the flagship project of site-designer AmeriCann Inc., a publicly traded company that develops facilities for the production of cannabis, cannabis-infused products and concentrates, and the grand vision of its chief executive officer, Tim Keogh, who grew up in nearby Marion.
Keogh’s goal is to create an actual physical hub—a state-of-the-art campus where multiple licensed operators can co-locate to grow, cultivate, and process their cannabis using the most advanced technologies and cutting-edge manufacturing practices available. AmeriCann has the permits to build up to 987,000 square feet of infrastructure on the property, and Keogh hopes to attract as many as eight “tenant” partners during the next several years.
AmeriCann’s first partner? Bask Inc., a stalwart of the cannabis scene in Massachusetts’s Southcoast area. In February, Bask moved from the Southcoast town of Fairhaven into a new 30,000-square-foot home at the MCC known as “Building 1,” the first to be completed as part of AmeriCann’s project. Under a joint venture with AmeriCann, which began in 2016, Bask will operate in Building 1 for 15 years, with the option to expand its physical footprint. According to AmeriCann, Building 1 is projected to produce 7,500 pounds of dry flower annually and more than 400,000 units of infused products. As part of the partnership between the companies, AmeriCann will receive a “revenue participation fee” of 15% of gross revenue on all products produced from Building 1.
Tech at the core
“If we were going to invest millions of dollars in a cannabis-cultivation and processing facility, we had to ask ourselves some tough questions,” Keogh says, such as: How should AmeriCann design the structure? “That’s where we started really looking at ourselves like an ag-tech company.”
To ensure every square inch of the center is used efficiently and allows for consistent, top-grade cannabis production, AmeriCann embraced automation and data analytics. The company created “Cannopy”—an umbrella term for a set of systems and equipment that it adapted and consolidated from tech vendors—which operators can avail themselves of as tenants. Keogh declined to share specifics about Cannopy but said AmeriCann is promoting the solution as one-stop and all-inclusive. Cultivators just have to show up and grow.
Making tech the center’s core feature was an easy choice, Keogh admits. As an advocate for pro-cannabis regulation in the early days of legalization, Keogh had observed firsthand how some companies adopted new technology and thrived as a result. Since then he has come to think of tech as a necessity, he says. But the decision to be tech-centric was dependent on another, perhaps more controversial one: The MCC would rely entirely on greenhouse technology.
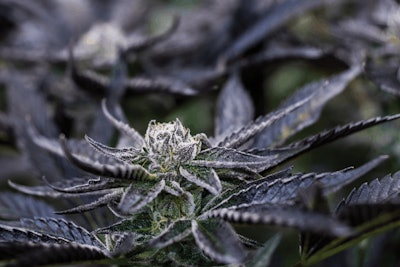
Going Green
In Keogh’s view, the most efficient and cost-effective way to grow high-quality cannabis at scale is under the sun in modern industrial greenhouses aided by digital technologies.
Keogh did not come to this conclusion based on emotion or anecdotal evidence, he says. As a former designer of marinas and boatyards, Keogh thinks differently than the average person about where light and energy will come from, how air flows, how people will maneuver themselves and objects within the space, what is absolutely essential to the space, and what can be easily omitted.
And greenhouse technologies have also improved greatly in the past ten years: With digital tools, growers can control and automate the heating, cooling, dehumidification, fogging, lighting, airflow, ventilation, and just about every other make-or-break condition for a successful grow, Keogh says.
“With hybrid-greenhouse technology, we have most of the benefits of indoor grows,” Keogh says. “But the big advantage is that we can bring in natural sunlight when it’s available. It cuts down our carbon footprint and reduces utility costs—and it’s a lot more efficient.”
Not everyone shared Keogh’s enthusiasm for greenhouse cultivation, however. Freetown officials were skeptical, Keogh says. To get the local community comfortable with the idea of the MCC, Keogh says he took some members of the town’s council, planning board, fire department, and building department on a tour of a leafy greens greenhouse operation in New Hampshire.
“Some people have this vision of hoop houses with poly tarp draped over them like in people’s backyards,” Keogh says of the public perception of greenhouse growing.
Innovating for Efficiency
Technologies like artificial intelligence (AI), robotics and new methods for continuous manufacturing hold enormous potential for improving how cannabis companies cultivate, process, and sell their products to customers. But some established industry players have been slower than others to adopt new technologies because, historically, there was little incentive for cannabis companies to innovate and be more efficient, Keogh says.
“Why would a company invest $20,000, $30,000, or even $100,000 on an irrigation system if they can pay a few people to water their plants and still make a profit?” he says. “… The problem is that doesn’t necessarily scale up. As you scale, any inefficiency—like the lack of an irrigation system—is going to eat into the margin.”
With this context, it’s easy to see why Bask is such a good fit for AmeriCann’s MCC. The vertically integrated company is not only Massachusetts to its core, but it operates much like a rapidly scaling tech startup, its culture imbued with equal parts tenacity and humility.
Though Bask CEO Chapman “Chappy” Dickerson jokes that he’s been “fighting technology” his whole life, he’s also quick to point out that he embraces a new technology or approach if it means “working smarter, not harder” and “getting results.”
In most technology-propelled companies, the CEO is also the chief technology booster, providing not only the resources to use new technologies, but, just as important, the permission for every employee to think and act boldly and creatively, developing an expansive view of the future. That is Dickerson.
“There’s a better way to do everything,” says Dickerson, who served in the military and worked as a commercial fisherman before leading Bask. “Just like there’s always someone tougher than you. It’s the same thing with cultivating. There’s always a better way; somebody’s always going to do it better. So you try to adapt and do it the best you can.”
The willingness to embrace technology and change started with Bask’s manufacturing process. Before Bask relocated its operations to the MCC, AmeriCann’s team worked with Dickerson’s team to streamline every aspect of the cultivation and processing operation. As Keogh put it, AmeriCann “took the stopwatches out.” It wanted to understand where the slack was in the system, and if Bask could do things better and faster. So Bask shifted to a lean manufacturing model, where workers execute a variety of production tasks, take responsibility for product quality, and are encouraged to find ways to improve the production process.
One specific change was to move to an “everyday production model,” in which the same task—whether that’s cloning, transplanting, feeding, trimming, or other growing tasks—is performed every day by each worker. With more predictability built into processes, workers can focus more of their attentions on improvements and creative problem-solving.
“They came in and said, ‘Hey Chappy, you’re doing a great job, but you’re doing it all wrong,’” Dickerson jokes about AmeriCann. “I don’t need to be biggest, but I want to be the best I can be.”
_fmt.png?auto=format%2Ccompress&fit=max&q=70&w=400)
Working With, And Alongside, The Machine
The continued spread of artificial intelligence (AI) technology has stoked fears of machines and algorithms running the world. Many employees worry they will soon report to robots—or be replaced by them.
At Bask, you see a more encouraging picture in which people and machines are not rivals fighting for jobs but rather are close collaborators, each taking advantage of the other’s complementary strengths.
From climate-control equipment to inventory tracking systems, almost everything in Bask’s operation is now online-enabled, in the cloud, on hard drives, or on a tablet computer. When something breaks down or fails to perform as expected, growers can’t afford to stop everything, track down a user’s manual and spend the rest of the day troubleshooting. As Dickerson says, “I can’t Google my way through fixing everything.” This is where AmeriCann’s tech system control comes to the rescue.
Armed with a tablet and an app feeding him real-time data about the growing conditions in the greenhouse, Christian Powers, Bask’s head of cultivation, has more time and mental energy to make strategic and tactical decisions to optimize grow operations and think bigger picture about the business.
“It’s really the brains of our whole operation,” Powers says of the app. “If a computer [senses] a mistake, it sends us an alarm. If I make a mistake, an alarm doesn’t get sent out ... I have to tell everyone that I just made a big mistake.”
“If I die tomorrow, the business still runs,” Dickerson adds. By having all this critical data integrated into one analytics interface, Bask can see how its systems work together and what it can change going forward. “By next March we can really see what works well [with a year of data-collection],” Dickerson says.
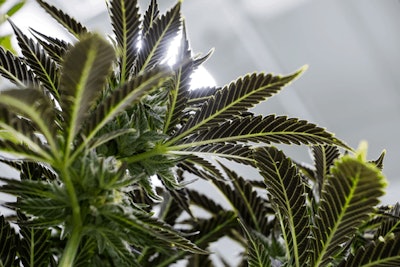
Becoming the Hub
As the Massachusetts market continues to evolve, Keogh hopes the MCC will serve as the state’s industry’s hub.
In-state demand already is encouraging. According to the Massachusetts Cannabis Control Commission (MCCC), the state’s recreational dispensaries sold more than $157 million worth of cannabis so far in 2020.
However, the COVID-19 pandemic’s impact on adult-use stores, which were not deemed “essential businesses” like their medical counterparts and were forced to close until at least May 4 (as of press time), remains to be seen. According to the MCCC, from March 23 to April 1, 2020, after it was announced that adult-use stores would shut down March 24, 1,308 people registered under the medical program, a 158 percent increase from the period 10 days before.
“The licenses held in AmeriCann’s project are both medical licenses—medical cultivation, medical processing—so from that standpoint nothing has changed,” Keogh said in a follow-up interview at the end of March. He said Bask’s Fairhaven dispensary saw an uptick in sales as customers stockpiled product in March before Gov. Charlie Baker’s stay-at-home order, and continue to come in.
With Bask operations humming and Dickerson already thinking about expansion, AmeriCann is optimistic about the future.
The next step for AmeriCann? Become an operator.
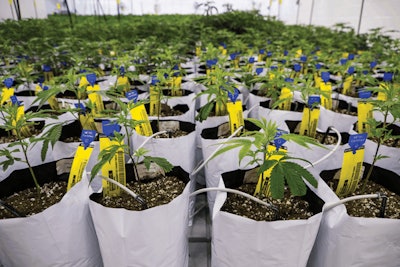
“From AmeriCann’s standpoint, we’re going to have a handful of companies here each with about 100,000 or more of square feet to themselves. And so we said, ‘Why not us as well?’” Keogh says.
The company established a new subsidiary, AmeriCann Brands, to cultivate and process cannabis on site at the MCC, and is seeking the requisite approvals to do so. As a potential multi-state operator, AmeriCann Brands would take advantage of the same technology solutions, systems, and innovations the parent corporation developed for companies like Bask.
This raises some issues about data use. As the creator and owner of the Cannopy system, AmeriCann the parent company and its newly created AmeriCann Brands could theoretically have the leg up on its tenant competitors and potentially have access to new rivals’ data and trade secrets. But Keogh says AmeriCann sees MCC occupants as partners. The way the deal between Bask and AmeriCann is structured, AmeriCann benefits financially if Bask succeeds.
Keogh says AmeriCann collects results, productivity, and efficiency data from its agricultural technology and building systems to be as efficient as possible. “We have been transparent about the data with our existing partners and inquiring future partners,” he says.
AmeriCann has already taken steps to draw clear lines of demarcation—every operator must have its own security staff and take responsibility for maintaining its own infrastructure. Despite the potential for competitive tensions, Keogh says he believes one selling feature of the MCC is that it’s a turn-key property. Licensed operators can come in and get right to work. And AmeriCann has an enviable vantage point to see what works and what doesn’t.