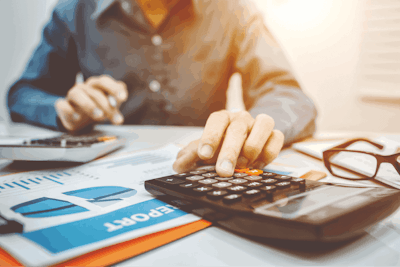
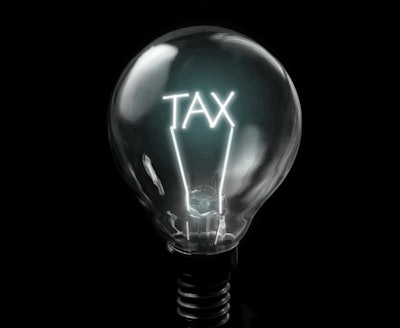
On March 30, 2020, the U.S. Treasury Inspector General for Tax Administration (TIGTA) released a report that noted the federal government missed out on $48.5 million in tax revenue from cannabis businesses in California, Oregon and Washington that were not in compliance with Section 280E of the tax code in tax year 2016. Projected over five years, that amount came out to $242.6 million in those three states alone.
As a result, TIGTA recommended the Internal Revenue Service (IRS) “leverage publically [sic] available information at the State level and expand the use of existing Fed/State agreements to identify nonfilers and unreported income in the marijuana industry.” As Rachel Gillette, partner and chair of Greenspoon Marder’s Cannabis Law Practice, told Cannabis Business Times in April 2020, “the industry should plan for more audits—not fewer audits—in the future.”
Thankfully, there are a few ways that plant-touching cannabis companies might be able to legally reduce their tax liabilities while remaining in compliance with Section 280E, including leveraging IRC Section 471(c) and the Research and Development Tax Credit.
IRC Section 471(c)
The Tax Cuts and Jobs Act of 2017 modified parts of the tax code, including a section called 471(c), which allows cannabis companies to change their accounting method from accrual to cash. (For more on the difference between accrual and cash accounting, see sidebar below.) The IRS normally would need to approve a change in accounting method. But with the update, which was effective in 2018, the change is “automatically accepted as long as your books and records reflect this change of accounting,” Mike Goral, partner at Armanino, a national accounting and consulting firm, tells CBT. “471(c) provides some leeway [on how] to do your accounting for your books and records.”
The change was a technicality, but it offers a chance for small businesses, defined by statute as a company earning less than $25 million/year, to reduce their tax burden by only paying taxes on money that has been officially transacted and exclude outstanding receipts and bills from their tax filings.
For example, if a grower sends an invoice to a retail company for $50,000 worth of flower products delivered, “normally you’d have to put that $50,000 on your books and … for tax purposes, it looks as if you already got the $50,000,” Goral explains. “Under the cash method, you have to wait until you get the actual cash in order to be able to put it on your books,” at which point the business can be taxed on it.
Goral stresses that while businesses can defer declaring revenue to the next tax year by using Section 471(c), 280E still applies. He also notes that if a holding company operates different licenses, then the holding company’s total revenue cannot exceed $25 million for it to qualify for 471(c). For example, if a holding company operates three licenses under the parent company’s umbrella, and each license reports revenues of $10 million, $12 million, and $5 million, the company does not qualify for a change in accounting method.
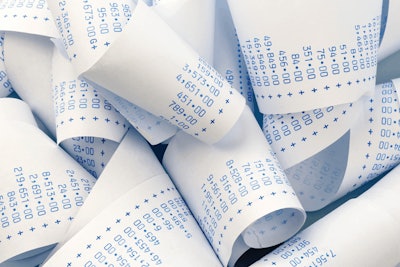
R&D Tax Credit
The R&D Tax Credit is another credit that appears to be available for plant-touching cannabis businesses—but careful planning, corporate structuring and bookkeeping are required.
The R&D credit is designed to reward innovation, according to Daren Shaver, an attorney with California-based Hanson Bridgett. “Any business that is eliminating technical uncertainty in the development of products or experimenting and relying on science to really develop a product [is] a very good candidate for an R&D credit,” he told CBT in December.
That doesn’t mean that simply adding an extra dose of nutrients and noting the effect allows growers to claim those costs as an R&D credit. Rather, expenses relating to breeding programs for the development of therapeutically valuable genetics, equipment modification and/or design that facilitates or improves a manufacturing process, and/or developing novel or innovative consumer products (such as a faster uptake method to increase the bioavailability of cannabinoids) can all be used to apply for an R&D tax credit.
Plant-touching cannabis businesses should structure their corporation thoughtfully, Shaver says. Separating R&D activities from plant-touching activities is crucial to obtaining the R&D credit. For example, if a cultivation company has an employee whose sole job is to oversee and conduct research and analysis, that employee’s salary could be used in applying for an R&D tax credit, Shaver explains. If that employee is a part-time researcher, then the company should keep track of how much of that employee’s time is spent on R&D and only use that portion of the employee’s salary when applying for the credit.
Costs for supplies and equipment also can be eligible as long as the research being done is science-based. Additionally, if the research has applications outside the cannabis industry, that could also increase the chances of getting the R&D credit, according to Shaver.

Be on the Lookout
Federal prohibition continues to be a major hindrance for cannabis companies in a multitude of ways, but that doesn’t mean the industry is without lifelines. Goral advises cannabis companies to be on the lookout for potential opportunities to take advantage of to help reduce their tax burdens while they remain under the onerous requirements of 280E. For example, while cannabis companies are not eligible for the Paycheck Protection Program under the Coronavirus Aid, Relief, and Economic Securities (CARES) Act, he says they are able to apply for the employee retention credit.
Being aware of the options “could be the difference between staying in business and not making it until next year,” Goral says.