
Based in Portland, Ore., Pruf operates as part cultivation business and part research and development (R&D) lab. It benefits from being a subsidiary of GroundWorks Industries, a vertically integrated company with investments in production (Pruf Cultivar), retail (Serra, Electric Lettuce and Farma), distribution (GW Distribution), processing (GW Processing, GW Workshop) and services (GW Services).
Being part of the vertically integrated business guarantees shelf space for Pruf’s products in Oregon’s competitive market. More importantly, though, says Groundworks Industries COO Karlee Eichenberger, “it’s something that helps us provide the right amount of depth to the conversation we’re trying to have [with customers].”
That conversation is quite advanced: Pruf’s product labels and in-store information cards go beyond strain names and THC content to include extended terpene and minor cannabinoid details—a point of pride for Pruf’s Director of Production Science Jeremy Plumb.
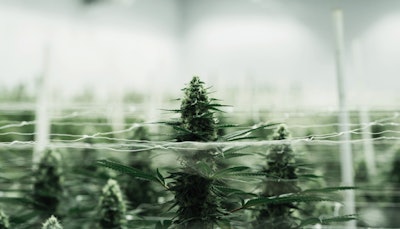
A long-time cannabis activist and researcher whom Willamette Weekly once qualified as “the smartest guy in the room,” Plumb leads Pruf’s R&D projects. He is most passionate about the cultivation environment’s impact on a cultivar’s cannabinoid and terpene profile (aka phytochemistry). “I live to find correlation between changing environmental conditions and various phytochemical outcomes,” he says. “To make the connection between genotypes and chemical phenotypes is just as exciting as it gets.”
Plumb’s passion for discovering, creating and expressing exotic phytochemical profiles stems from his past experiences. He was a patient advocate in the ’90s, when the AIDS epidemic was ravaging California communities. Having already been inspired by the work of cannabis pioneer’s such as Chris Conrad, Mikki Norris, Lester Grinspoon and many others, he eventually had the opportunity to watch Dennis Peron interact with patients at his famed San Francisco Cannabis Buyers’ Club. Seeing patients receive the standard of care offered by that collective, as well as by Women Advocates for Medical Marijuana (WAMM) in Santa Cruz, galvanized Plumb to study cannabis.
When he moved to Portland in 2000, he became involved with the medical cannabis program. After a subsequent encounter with Sunrise Analytical founder Pat Marshall, he began conducting chemical analyses of his own plants and other medical patients’ crops. “I had years of data to look at up to 64 compounds from the plant,” he says. “As the data became clearer, I recognized that the phenotypic range of cannabis is profound, and that you can take a single genotype and change conditions in the environment and see pretty [distinct] results in the chemical phenotype.”
Plumb identifies three pillars to what he calls Pruf’s Innovation Lab: 1) advanced organic crop production methodology; 2) photobiology; and 3) efforts to improve genetics via phenotype discovery coupled with a hybridization program populated with a deeply curated selection of plants. He credits the research in these areas for the company’s advancements in product quality.
Growing Organic
One of Plumb’s first major decisions after joining Pruf Cultivar in 2017 was to “rip out” the mineral salt fertilizer system and to move toward an organic substrate and fertilizers. Many reasons spurred this change, including ecological value and product purity.
“Having the diverse organic rhizosphere dynamics makes it a lot more complicated than simply running a mineral-salt fertilizer program,” Plumb says. “But [what] I have seen in my early observational studies, [is] … a general trend toward more chemo-diverse sets of profiles from organically produced cannabis in my gardens, as opposed to more chemo-intensive cannabis produced in my mineral salt fertilizer-driven gardens.” In other words, his analytical results point to organic-crop production as better suited to express a broader array of compounds in targeted profiles (Pruf’s ultimate goal), while mineral salt-produced crops generally showed absence of other compounds and higher levels of only certain terpenes.
The switch from mineral salts to organic crop production was an interesting challenge for Lee Nye, Pruf’s head grower, especially considering her background as an ornamental plant grower for Pleasant View Gardens and D.S. Cole Growers in New Hampshire.
“We have clean rooms that are safe, … we can minimize pests coming in,” she says. However, when “we add the biology of the plants and the soil and organic fertilizer, … then [it’s about] learning how to build that ecosystem in a clean room.” Despite the challenges, she says the change to organic methods and the subsequent Clean Green certification were necessary, adding that “most of our competitors are Clean Green [Certified], so it’s an expectation [in the market].”
Implementing organic production also caused Pruf to adjust how it watered its crops. “With your organic soil, you have things like worm castings—things [that] are being broken down by microbes, and there’s always a good chance that you’re going to have something like a fungal pathogen or any kind of bacteria” being brought in, says Kylie Mendonca, a plant health specialist (PHS) at Pruf, who previously studied applied agriculture science at the University of California-Davis and obtained a master’s degree in horticulture crop science from California Polytechnic State University.
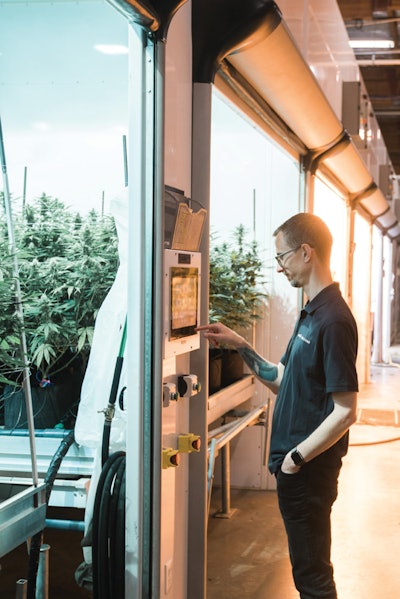
Assuming a constant pest outbreak threat forces Mendonca and Pruf’s other PHSs “to really tightly control the environment” and inputs. For example, says Mendonca, “we had to make sure we weren’t over-watering to create an environment that a fungus would like.”
A custom-designed, fully automated Dosatron fertigation system helps Nye and the PHS team avoid watering and feeding issues, and nutrient recipes can be fine-tuned to a specific cultivar and its current growth stage. (These recipes are based on Plumb’s past research and have been tweaked by Nye and the PHS team to maximize each cultivar’s expressions.) It also allows the PHS team to spend more time on trials, Mendonca says.
“Everyone’s got their side projects where we’re testing different fertilizers, or we’re trying out different soil mixes or … light regimens. It takes a lot of time for the plant health specialists to … pursue these little projects that are ultimately going to move our growing practices forward,” she says.
During trials, environment data collection is aided by Pruf’s custom-made environmental control system (ECS),o called PrufOS. In addition to tracking all the factors relating to plant growth, as any good ECS would, “we’ve tuned it up with a proprietary machine-learning platform,” Plumb says. “It can look at multi-variable equations and, in a lot of ways, make me obsolete in time.”
Pruf’s system can analyze genotype data created by partner labs, detailed environmental data (thanks to an array of sensors in every cultivation area), as well as high-resolution phytochemistry data—which Plumb says helps the cultivation team come up with targeted approaches toward revolutionary phytochemical solutions.
For example, when Pruf observed that the parts of the canopy that received the most light (the top) had higher levels of cannabinoids and terpenes compared to sections with less light (the bottom), the team decided to move from 5-gallon pots to 2-gallon pots. While plants wouldn’t grow as big, the smaller pots mean more plants can fit in a grow space, ultimately leading to more flower area being hit by light and increasing the cannabinoid and terpene content in those crop sections. Pruf is currently transitioning from roughly 14,000, 5-gallon pots to 24,000, 2-gallon pots, and expects that transition to be completed by Q1 2019.
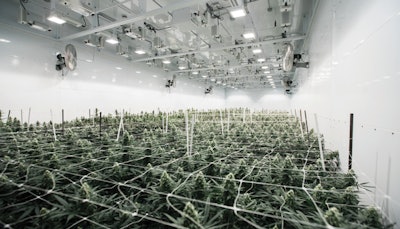
Photobiology
With photobiology (the study of light’s effects on living organisms) being another of the company’s main building blocks, Pruf made another change to its cultivation practices to truly test lighting’s impact on plant development by switching from high-intensity discharge (HID) lamps to LEDs.
“With the advent of LEDs, we found the ability to control wavelength and output, and beam angle and deficiencies in levels that [were] never remotely possible with a high-intensity discharge system,” Plumb explains. “Using LEDs allows for us to open the door to proper photobiology research where we can use a single wavelength at a particular stage of development, and greatly influence plant morphology to manipulate and optimize the expression of phytochemical production.”
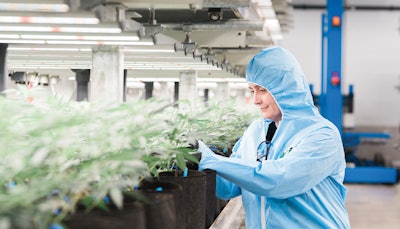
Pruf is on its fourth lighting trial using LED fixtures. In one flower room, the company is testing how LEDs set at a photosynthetic photon flux density (PPFD) of more than 1,600 µmols affect plants, compared to a double-ended high-pressure sodium (HPS) fixture set at 800 µmols (which are still in use in a few of Pruf’s flower rooms). So far, Plumb has seen increased phytochemical diversity and biomass (yield) in that trial—mostly thanks to the increased PPFD and wavelength without the corresponding heat load increase that comes with non-LED fixtures.
Lighting trials, along with the conversion to LED technology, have enabled and pushed Pruf to adopt different technologies, including vertical racking systems. “We’ve been able to do things that are just absolutely remarkable, partly because we’ve decoupled radiant heat from the fixture; high-intensity discharge fixtures are notorious for building huge thermal loads,” Plumb says.
In its vegetation room, Pruf installed a three-tier vertical racking system with two rows of racks for a total of six shelves, Nye says. “Each one of those tiers has dimmable lighting [comprising 12 lighting zones], so that we can actually have different crops in there at the same time getting the light that they need, and not try to compromise between all of the crops.” In addition to the 12 lighting zones, there are 16 different fertigation zones in the veg room, allowing the Pruf team to feed each cultivar exactly what it needs and granting cultivation staff even more crop control.
Plant Health Specialists are each in charge of three to four flowering rooms, but the veg room is granted one dedicated staffer, Charlie Smith. Smith can oversee up to eight varieties in that one room alone, Nye says, a complicated task due to the variety of cultivars the company offers and the amount of data Pruf collects for each crop—such as rooting times and plant health.
To help with the veg room work, Pruf purchased a robot the team affectionately calls Clarence. Resembling a forklift on tracks, Clarence can be directed to any tier, pull trays and bring them to the staffer who can then work with the plants at a comfortable height. The robot also increases employee safety, as team members don’t have to use cherry-pickers or ladders to inspect elevated plants. (Editor’s note: See Clarence in action at: bit.ly/pruf-clarence.)
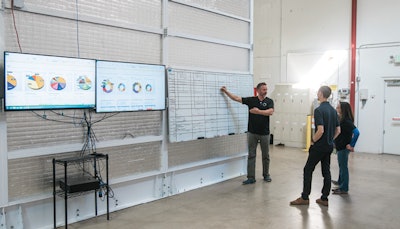
Pheno Disco
As a co-founder of the Open Cannabis Project, an organization dedicated to building the world’s largest public domain of cannabis genetics, Plumb understands the central role genetics are going to play in this industry’s future. That is why Pruf is amidst its first round of its phenotype discovery program: a period dedicated to seed-popping that staff refers to as “Pheno Disco.”
“We just started our first lot of a thousand [seeds from 100 different cultivars] for a phenotype discovery program that will take really high-resolution genetic data from every single cultivar that is germinated,” Plumb says. Pheno Disco is currently taking place in multiple rooms: the veg room is where seed germination and early growth happen. From there, the cuttings from that vegetative tissue go into a propagation environment. After that, plants mature enough to be flowered go into an all-LED bloom environment. Additionally, every environmental variable during Pheno Disco is tracked through the PrufOS system and correlated to a cultivar’s progress and chemistry.
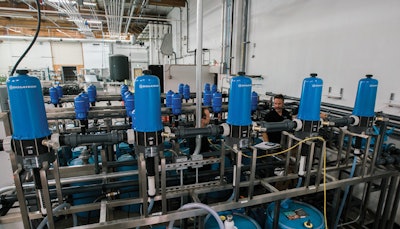
Offering different products with different chemical compositions than the competition is an obvious reason why the company is working so hard to find unique genetics and expressions. But for the director of production science, having different chemical compositions also means better serving the diverse needs of patients and consumers. Plumb imagines a world in which cannabis plays a central role in people’s health and well-being—whether they are (re)introducing themselves to cannabis as a health and wellness supplement, seeking options without the “medicated” feeling or looking for an intense cerebral experience.
“We’re in a post-THC and -CBD world,” Plumb says. “We’re in a chemical fingerprinting world, which goes beyond the cannabinoids and terpenes … and we have to start to lean into this unbelievable complexity, knowing full well this is really the most phytochemically complex plant to interact with.”
Germinating seeds is far from the last stop in Pruf’s hunt for new chemovars. Once interesting specimens (i.e. those with exotic cannabinoid and terpene contents) are identified, they will be brought into one of Pruf’s three mother rooms to have cuttings sampled for further study and hybridization, which in turn will yield even more genetic diversity.
“We [at Pruf] see ourselves as adventurers on the path to imagining how to both wield that phytochemistry for the good of the whole and to consistently be able to reproduce it,” Plumb says.
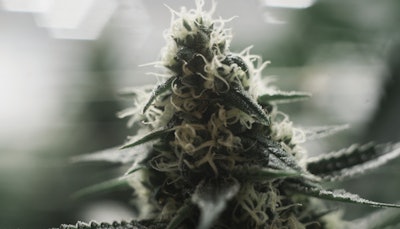
A Company of the Future
For Eichenberger, investing heavily in R&D comes with risks. Balancing R&D with financial solvability, she says, “is a struggle that I can’t pretend we’ve mastered perfectly. ... [However,] that innovation is part of our core values.”
For example, companies might forgo Pheno Disco and only cultivate from purchased clones because it takes longer to grow from seed. But, the COO says, “I think that when we pause and ask ourselves why we’re doing it, we always agree that it’s important.”
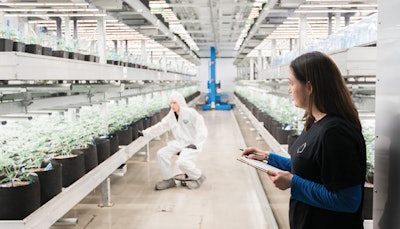
What balances those costs is the company’s dedication to being part of the cannabis industry for the long-term. In five years, Eichenberger would like GroundWorks Industries, and Pruf Cultivar, to be known throughout the U.S. for genetic innovation and for pushing forward all that is possible with this plant.
The cultivation team is confident in being able to achieve those lofty goals. “It’s like we’re constantly at the edge of discovery,” Plumb says. “There’s always an opportunity to gain insight right now. There’s so much low-hanging fruit because of the fact that, despite all of the passion … for this plant, it has simply not been worked with in a way that allowed for a mature expression of research and development.”