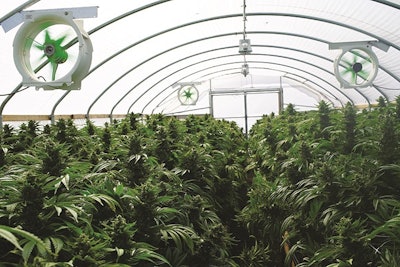
When growing cannabis, you can’t underestimate the importance of a heating, ventilation and air conditioning (HVAC) system. A good HVAC system regulates temperature, humidity and air quality. An HVAC system also regulates airflow, provides ventilation and can increase technology in grow rooms, depending on how sophisticated the system. But an HVAC system for a cultivation facility isn’t like other HVAC systems. Cultivators have specific needs, and building and running a proper system catered to cannabis isn’t that simple.
Cannabis Business Times turned to the experts to learn about the 10 top mistakes or problems that you could experience when it comes to using an HVAC system in your operation, and how you can avoid or address them.
Here’s what they said.
1. You didn’t prepare for the cost.
An HVAC system can be costly. In fact, Aaron Mullins, systems engineer for Denver-based cannabis consultancy Next Big Crop, has worked on projects where HVAC system costs reached up to $120 per square foot of facility space. “A lot of the time, owners aren’t prepared for the cost of the system,” he says, “so they try to cut costs—they under-specify the system or build it out at 80 percent of what they need.” Nothing is wrong with trying to save money, but when you under-build and inevitable problems arise, Mullins warns, “you won’t have the capacity to deal with them.” To ensure your HVAC is built to last and evolve, Mullins recommends identifying what you need for production today—then building an HVAC system that’s 20-percent bigger. “That way, if something comes up, you have the capacity to deal with it,” he says.
Things like dehumidifiers or cooling units malfunctioning, varying plant transpiration rates and changes to the outside environment can all increase humidity levels in cultivation areas, Mullins says. “A lot of the variables that affect the room can change over time, and it’s best to have a buffer … built in to accommodate this.
“It’s more expensive upfront, but you will recoup all of the costs in the first disaster you have.”
2. Your upfront costs cut into your operating expenses.
Simply because an HVAC system is expensive up-front doesn’t mean you can’t reduce your month-to-month costs, according to Rick Harder, co-owner of Oregon Cannabis Authority, a cultivation operation and producer in Springfield, Ore. Running an HVAC to its max daily would generate a large electric bill, so when Harder installed his 1,000-watt Gavita HPS lights, he also ordered a 20-inch fan for each of his three, 1,000-square-foot grow rooms. With Oregon’s year-round temperate weather, the fans help supplement the HVAC by providing fresh air and controlling heat and humidity. “The fans don’t cost much to run,” Harder says, “and now I don’t have the big HVAC units running all the time.”
3. You didn’t match your lights to your new system.
When L’Eagle in Denver installed a new HVAC system equipped with a REME HALO air purification system, co-owner Amy Andrle says the team had to evaluate their lighting to see how much air conditioning they would need for every light they had. Every 4,000 BTU (British thermal units)—or about what one ceramic metal halide light bulb produces—needs 1 ton of air conditioning, Andrle says. As L’Eagle installed the new HVAC system, the team knew it would be best for their operation to switch from ceramic metal halide lights to LED lights. “We needed to make sure that because less heat was created [by the LEDs], our thermostats were monitoring perfectly and the system was being regulated to account for fluctuations in humidity and heat as a result of the lighting changes,” she explains. Without that kind of careful planning, the company may not have installed as much AC as needed.
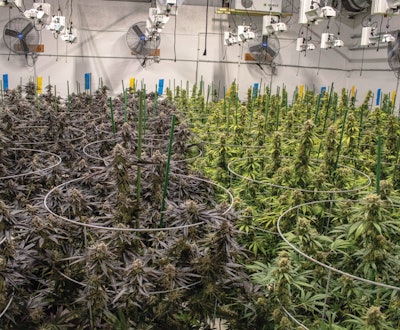
4. You didn’t work with a cannabis-savvy engineer.
While HVAC systems are common, what’s not so common is an engineer who knows how to build one especially for a grow facility, says Mullins. “A lot of the time, people reach out to engineers who don’t have experience building rooms with the requirements that grow rooms need,” says Mullins. He compares the complications of building an HVAC system for a grow space to building an indoor pool in a data center: In both cases, you have to accommodate conflicting needs for everything to properly operate.
If you’re alternating your light cycles in different grow rooms (meaning one set of lights is on during the day, the other is on during the night) Mullins says, “you need to consider what your heating and cooling load will be like in day and [at] night, and a lot of people don’t think about removing heat at night [when lights are on],” he says. “You need to find an engineer who is familiar working with grow facilities.”
5. You don’t have a backup plan.
When Harder of Oregon Cannabis Authority built out his HVAC system, he recognized the huge burden it bears for the grow rooms: It’s responsible for cooling, supplying fresh air, maintaining humidity levels and more. He knew that if the HVAC system went down, he would be in big trouble, so he realized he needed a “redundancy plan.” In other words, “it’s better to have two, 500-ton units than one, 1,000-ton unit,” he explains, “in case one goes out.”
6. You didn’t consider your environment.
A cultivation facility in Florida has different needs than one in Nevada, points out Mullins. If you didn’t consider what specific needs your environment has before you purchased your HVAC system, you could experience regrets. For example, if the internal humidity is too high in a Colorado grow, Mullins says, you have the luxury of bringing in outside air, but if it’s too high in a Florida grow, “that’s not an option,” he says. “The outside air is already hotter and more humid than what you’re working with,” he adds, so you need an HVAC system that works with, not against, your environment.
7. You didn’t consider the long-term investment.
Andrle loves the building that L’Eagle calls home. But L’Eagle doesn’t own the building; it is leased. “We installed an incredibly valuable HVAC system in a building we lease,” she says. It’s not a decision she regrets, but it’s something she encourages other growers to consider when purchasing or upgrading their systems.
“You can’t take [the HVAC] with you,” she says, “so you have to think about how it will benefit you in the time that you have it.”
The L’Eagle team decided it was best to install the best HVAC system they could afford. “It’s not just about plant health—it’s about employee health,” Andrle says. “You want to make sure that you’re filtering any impurities in the air.” That’s why L’Eagle opted for a hospital-grade HVAC system. “We have a team that’s dedicated to us, so why not try to create for them the best possible working environment we can?”
8. You didn’t consider electricity.
An HVAC system creates quite the electric bill. To keep costs down, Harder says he drops the wattage. “I kind of stumbled onto a little secret that works for me,” he says. Using an auto-dimmer feature, he dims the lights when the temperature increases, which in turn drops the temperature and allows him to run the HVAC system at a lower wattage. Once he did this, “I noticed the plants did as well, if not better,” he says. “When you oversaturate a plant with light, it can start to get a little yellow or light green.” Plus, Harder saved a bundle on his electric bill. By lowering the lights and therefore, lowering the AC, his bill has dropped from $4,500 to $3,200 a month, he says.
9. You didn’t consult your grower.
All growers have different preferences for their grow room environments. If you don’t consult them on the HVAC system before it’s installed, you could run into problems, Mullins warns, adding that many owners will build systems without consulting their growers first. It’s better to work with your grower when building or redesigning an HVAC system, so that the system can be customized to the grower’s needs and preferences.
10. You didn’t make a plan for your plants.
When L’Eagle installed its HVAC system, the team had to learn how the plants would respond to the humidification.
“We knew that the plants would react positively to a new HVAC system with better and cleaner air circulation,” Andrle says, but the team still wanted to keep a watchful eye on every plant. “It’s not that it affected each strain specifically, but more overall, [we had to ask] how does changing one variable factor into the overall formula of what goes into a room—i.e., beneficials, plant treatments, nutrients, additional fans and air circulation, dehumidification systems. The team needed to be very aware through the duration of a flowering cycle and record … any fluctuations.”
Other growers should do the same with a new HVAC system, she recommends. “You have to be ready to anticipate changes.”