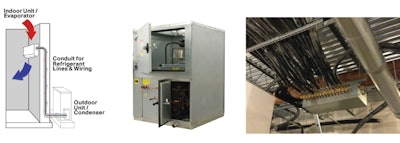
Developing the precise environment necessary for cannabis cultivation is important for healthy crops and a grower’s bottom line. Several technologies can be used for climate control, differing in functionality, reliability and cost, and choosing the right technology for a cultivation facility based on its specific goals and methodologies can be overwhelming. Here are some of the common technology choices, their applications in cannabis cultivation and the pros and cons of each, taking some of the guesswork out of the decision-making process.
Unitary Technologies
1. Split Systems and Mini Splits
A mini-split system supplies conditioned and heated air to one or more rooms within a building (providing anywhere from 9,000 to 36,000 BTUs). Split systems or multi-zone systems are commonly ductless and condition up to eight rooms (zones) from one outdoor unit (up to 60,000 BTUs). A variety of indoor-unit styles are available, including wall mounted, ceiling mounted, ceiling recessed and horizontal ducted.
The primary advantage of ductless air conditioners—beyond smaller size and flexibility for zoning or heating and cooling individual rooms—is their cost, which is about $1,500 to $2,000 per ton (12,000 BTUs per hour) of cooling capacity. Ductless systems are also more efficient. However, they require substantial equipment and electrical infrastructure, as the compressors are tied to specific zones within the facility, and direct control of humidity is impossible—as the system only comes on when the space is “hot,” regardless of humidity levels. The dew point from the coil is set by the evaporator and condensing unit and cannot be adjusted due to refrigerant pressures pre-engineered by the manufacturer. Additionally, mini-splits only offer up to 4 to 5 tons, so multiple units may be needed for any given room with multiple electrical connections. Mini-split systems also have a lower life expectancy compared to other designs, and frozen evaporators are common.
2. Self-Contained Systems (Self-Contained Splits)
Self-contained systems are larger, more complex versions of split and mini-splits. They utilize a direct refrigerant-to-air heat exchanger (evaporator) in the airstream to cool and dehumidify the space. They range in sizes up to 50 tons and have options that small-tonnage mini-splits lack, including ducting, UV lights, hot gas bypass for direct humidity control, and multiple heating options. These systems are sized for each space and come in either air-cooled, “split” condenser versions (condenser located outside with refrigerant piping between) or water-cooled condenser arrangements that require connection to an evaporative-cooling tower sitting outside to reject heat.
Self-contained units can be expensive and require floor space in the grow, although they may be placed outside the facility and ducted into the grow supply and return connections. Redundancy can be expensive or difficult with ductwork and space/sizing factors. Water-cooled versions require piping indoors to the condenser and associated tower, and frozen evaporators/air handlers are possible. However, self-contained systems feature easy integration into controls, direct humidity control and limited structural considerations.
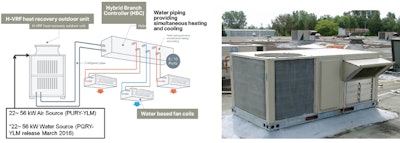
Packaged Technologies
3. Packaged Variable Refrigerant Flow (VRF)
Variable Refrigerant Flow (VRF)—or Variable Refrigerant Volume (VRV)—is an HVAC technology using refrigerant for heating and cooling. Refrigerant is conditioned by an outside condensing unit and circulated in the building through multiple fan coils. VRFs support variable motor speed and thus variable refrigerant flow, which allows for substantial energy savings at partial-load conditions. Heat-recovery VRF technology allows individual indoor units to heat or cool as required, while the compressor load benefits from internal heat recovery.
VRFs come in two-pipe and three-pipe system formats. In a heat pump (HP) two-pipe system, all zones must either be in cooling or heating. Heat Recovery (HR) systems, however, can simultaneously heat certain zones while cooling others, usually through a three-pipe design.
While heat-recovery systems have greater initial cost, VRFs also minimize ducting, have a smaller footprint and allow for a sealed cultivation area. However, they may have higher installation and maintenance costs, and refrigerant being pumped to terminal units pose a risk of leaks.
4. Roof Top Units (RTUs)
Roof-top packaged units (RTUs) are easy to maintain and are most suitable for lower-lying buildings with space on the roof for installation. The units themselves require ductwork for supply and return air distribution, power lines and drain piping.
RTUs come in a variety of efficiencies, sizes, features and costs. The RTU does not use indoor space, although ducting to the space is required. Most units come with a multi-zone arrangement, meaning outside and grow-space air is recirculated for both cooling and heating. These can pose odor-control and biological-contamination challenges as both bugs and nearby airborne contaminants can easily infiltrate standard damper packages, even when closed.
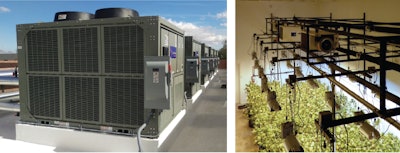
5. Complex Chilled Water System (Air Handling Units (AHUs))
By separating the machine producing the cooling from the indoor environment, chiller systems move cooling to the places that need it most, when they need it. The units can share chilled water for dissimilar loads, reducing electrical infrastructure requirements. A chiller can be outdoor (air-cooled) or indoor (water-cooled). Indoor models frequently require connection to an evaporative-cooling tower outside, which will consume water, while air-cooled models sit outside and do not require a tower. A complex chilled-water system regulates and circulates air as part of an HVAC system. AHUs usually connect to a ductwork system that distributes the conditioned air through the building and returns it to the AHU, but in some applications, AHUs discharge and admit air directly to and from the space served without ductwork.
Room temperature and humidity are controlled with a combination of different heat exchangers, as well as features and options inside the conditioned air stream going through the unit. In most applications, initial cost, unit controls complexity, local utility rates and energy consumption drive an owner to certain units and configurations. Common options include cooling via direct-refrigerant expansion coil (DX) and/or cooling via chilled-water coil (CW), heating and heat recovery.
6. Modular Chilled Water (CW) System
In a Modular Chilled-Water System, a bank of air-cooled chillers sits outside the facility for operational redundancy. The compressors inside the chillers maintain a precise temperature in a water/glycol mix that is then pumped around the building to fan coil units (FCUs) of varying sizes, controlled by a simple wall thermostat or control unit with on/off control. Warm, moist room air is circulated over the coils, transferring heat and humidity from inside the room to condensate in the unit drain pan and warm water for the closed chilled-water loop, which then goes back to the chiller via pumps, for the process to start again.
Multiple chillers and FCUs can be used inside and outside the grow with multiple fan coils tied back to the collective chiller bank, offering flexibility for the system to grow as needed. And because no fan coil is tied to one specific chiller directly via the chilled-water loop, any malfunction of either piece will not cause complete loss of cooling capacity. Dedicating space entirely to climate control indoors is unnecessary since most of the indoor equipment is hung from the ceiling, and the use of multiple fan coils also ensures more homogenized air due to distributed, ductless airflow. Although the initial expense can be slightly higher and engineering work is required to design the water-piping loop properly, these units offer greater efficiencies, redundancy, flexible tonnage, allows for a sealed cultivation environment and 24-hour dehumidification, even when compressors are off.