1. Why is mechanical design so important?
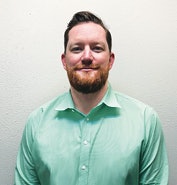
Troy Rippe: Your mechanical design might be the single most important decision you make as a cultivator, with far-reaching impact on the bottom line. Apart from initial costs, which are significant, the recurring costs associated with energy consumption will have an effect on your cost of cultivation throughout the life of the system. It’s also exceptionally difficult and costly to retrofit an existing mechanical system in an active cultivation facility. Most importantly, though, is the impact the mechanical system will have on yields and biosecurity. A poorly designed mechanical system is your single biggest vulnerability for crop loss due to fungus and pests, and a poorly managed environment is arguably the biggest contributor to diminished yields and quality in a cultivation facility.
2. Can you offer advice on specific mechanical design approaches?
Rippe: While we have the expertise to design just about anything, at Surna, we recommend a modular chilled water approach for most cultivation facilities. Chilled water allows for simple redundancy and scalability, high energy efficiency, lots of dehumidification options, simple maintenance, easy operation in extreme temperatures and free cooling options without the need to bring in outside air, which allows you to take advantage of cool outside temperatures without compromising biosecurity.
3. Is there anything I should know about the pros and cons of different air sterilization approaches?
Rippe: High efficiency particulate air (HEPA) filtration is tried and true, and generally filters out about 99.9 percent of airborne contaminants. The downside to HEPA is the cost of maintenance (filter replacement) and the high static pressure of the filter itself. Incorporating HEPA in line with your mechanical system can increase energy consumption because higher static pressure requires a more powerful fan. At Surna, we often employ a separate recirculating HEPA filter to get the benefit of HEPA without the energy hit on the whole mechanical system.
UV sterilizers in ductwork are quite effective at destroying air- and surface-borne viruses and bacteria. However, they have a minor impact on airborne fungi (mold, for instance) because they require more exposure time than they get to the light as they are moving through the air—and airborne fungus is likely what you’re most concerned about. UV lights do a respectable job of surface sterilization though, where exposure time between harvests can be long enough for them to be effective.
Various methods of oxidation/ionization are effective as well, and generally require very little power and maintenance. These units create hydroxyl radicals and super oxide ions by combining UV light, water vapor, and titanium dioxide (TiO2). The radicals and ions rapidly oxidize any particulate they encounter. However, take a hard look at any unit that claims to do both air and surface sanitation because surface sanitation means there is a possibility that plant material could be impacted. (Ensure that any vendor you’re considering has ample evidence that their units do not damage terpenes or plant cells.) Ozone (O3) is also a means of rapidly oxidizing particulates and volatile organic compounds (VOCs). It’s an effective sterilizer and odor remover; however, exposure can be dangerous to plants and humans. Ozone should only be applied between harvests in an unoccupied space for sterilization and possibly on exhaust air for extreme odor control. Ozone should not be employed in a room occupied by plants or humans.
4. How can I ensure that the mechanical engineer I’m working with will design the best system for my needs?
Rippe: First, experience is key. Ask your mechanical designer how many cultivation facilities they’ve designed, and ask to speak with a couple of existing clients to get a feel for their overall experience with their systems to ensure what was designed met their needs and budget. Ideally, speak with a client who has operated the system for a full year, so they have experience with it in every season.
Second, the engineer should be asking you the right questions to fully understand plant dynamics, your temperature and humidity needs and what your priorities are, and be able to easily explain the pros and cons of various approaches. Be wary of anyone telling you what you need; the design process should be a collaborative and consultative process with costs versus shortcomings explained so you can make an informed decision.
This goes without saying, but the engineer should also ask you a lot of questions around watering and lighting loads. The right engineer will understand the unique requirements of cultivation facilities and how those requirements fit in with local regulations and building codes. We see this overlooked often when engineers are hired. It can be very tricky to design cultivation facilities, as there is no code that directly addresses many common items, like economizers, for instance. The result is that many times, an engineer will either not be able to defend the design to local permitting personnel or over-design the system so much that the first cost is substantially higher than it needs to be. Lastly, the right engineer will understand how vital biosecurity is to your facility, and how important it is to maintaining a healthy crop. His or her understanding of these key issues (or lack thereof) will become apparent after just a few minutes of conversation, so getting a good feel for your engineer before you engage is your best assurance that the ultimate design will check all the right boxes. At Surna, we’ve been involved in more than 700 cultivation projects, so if you’ve already engaged a mechanical engineer and aren’t 100-percent confident in the design, reach out to us for a quick review.