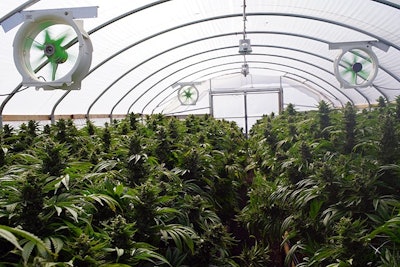
At the end of March 2018, the Commonwealth of Massachusetts published its regulations for the adult-use cannabis industry—the rules governing legal cultivation, distribution and use of cannabis products. They were the culmination of a series of legislative fits and starts to improve upon the referendum’s language. The Cannabis Control Commission completed a six-month sprint, holding dozens of advisory board meetings, public meetings and two multi-day listening sessions across the state. Members heard from hundreds of individuals expressing their opinions on all aspects of the industry.
The regulations are expansive in their scope and touch upon every facet of the industry. Energy and environmental aspects related to cannabis cultivation, product manufacturing, retail and transportation of cannabis products are defined. In essence, the new regulations affecting a facility’s environmental impact fall into three discrete areas: energy, water and waste.
All cannabis businesses seeking a license need to include in their written operating procedures: a description of how they intend to implement energy use and demand reduction opportunities, how they are engaging with utility energy efficiency programs and how they are considering incorporating renewable energy into their power supply.
Lighting
For cultivation facilities, these criteria have been overshadowed by groundbreaking lighting rules that call for facilities to cap wattage per square foot. Cultivation space of 5,001 square feet or more (Tier 3 and higher, in the legal parlance) specifies a lighting power density (LPD) of no more than 36 watts per square foot (W/SF). Growers with 5,000 square feet of canopy or less (Tier 1 & 2) need to achieve an LPD under 50 W/SF.
Many observers are suggesting that this standard spells the end of commercial-scale HID lamps —or worse, indoor commercial growers writ large—but growers willing to make a few tweaks should find them manageable. For example, raising the height of lamps or spreading them out more may be able to reduce growers’ LPD below the threshold.
Given the pace of innovation in lighting technology, it is conceivable that in just a few years growers could obtain acceptable yields and qualities using lighting that is more efficient than even the leanest HID.
In any stage of a facility’s development, smart growers will study their options carefully. Always use real data when making decisions about equipment selection including lamp replacement cycles, the value of utility rebates, local electricity rates, and utility demand charges.
Regardless of equipment selection, many growers should be able to reduce their energy consumption by optimizing the inputs plants receive. For example, plants only take in light when they need it, and smart sensors and automation can control lighting output based on plants’ actual physical needs. Growers may want to consider growing shorter plants, which will shrink vegetation time and allow for faster flips. This technique will reduce energy use due to the more prolonged light exposure the vegetation phase requires and the subsequent reduction in heating, ventilation, cooling, and dehumidification (HVAC) needs.
Environmental Conditions
For HVAC equipment used in cannabis cultivation facilities, Massachusetts requires all growers to meet Massachusetts Building Code requirements and all state amendments to relevant codes. Licensed HVAC engineers can identify eligible equipment for growing operations. Even with code-compliant HVAC equipment, grower practices will go a long way in reducing their energy costs.
Fundamentally, as with lighting, gathering and analyzing data of a grow’s environmental conditions is critical. What is measured is as relevant and how. Measuring relative humidity will only go so far considering how much mechanical cooling and dehumidification a room needs because it only measures the amount of water in the air relative to air temperature.
Instead, Vapor Pressure Deficit (VPD) provides growers with a measurement of humidity and transpiration levels. VPD is a more relevant indication of how plants feel. A bonus is that the focus on VPD and plants’ needs throughout their growth cycles may mean your plants can sometimes handle more humidity freeing up demands on your HVAC. Incidentally, this may also open up additional opportunities to explore water reclamation technology that lets you collect atmospheric moisture or condensate, filter it and re-use it, thus saving on water costs.
The Massachusetts regulations also obligate the building envelope for all cultivation facilities, except for greenhouses, to meet the minimum Massachusetts Building Code requirements and all state amendments to relevant national and international codes. Growers using existing buildings may demonstrate compliance by showing the envelope insulation complies with code minimum standards for “Type Factory Industrial F-1”. As for HVAC, licensed building professionals know and understand how to apply these standards to a cannabis cultivation facility. In short, this requires growers to be thoughtful about the structural integrity of the building in which they operate and minimize the loss of conditioned air beyond what they may intentionally ventilate.
Indoor Building Materials
For growers contemplating new indoor buildouts, one of the most critical components they need to consider is what building materials to use. While the selection of articles seems far removed from plant quality and energy efficiency, growers that choose poorly invite trouble, particularly in creating environments that may host molds.
One notably promising option is Permatherm; wall material made of a Styrofoam interior and metal exterior. While not necessarily a load-bearing element, it breathes well, discourages mold growth and provides a sufficient buffer between both exterior and interior spaces. Poly-panel is a less expensive wall alternative that is non-porous and can handle chemical disinfectant. Avoid drywall and green board at all costs due to mold and mildew risks.
Growers developing plans for a new operation may want to choose different types of facilities altogether. Greenhouse technologies have evolved to deliver performance equal to indoor facilities. Depending on a range of factors, including external temperatures, humidity levels, and light levels, greenhouse growers may be able to reduce their operating costs significantly over traditional indoor setups. Seasonal cultivators might even prefer being outside altogether resulting in the lowest startup and operational costs.
The regulations also require both cultivators and product manufacturers to use best practices for water and waste management. While the state’s Cannabis Control Commission has yet to describe what those best practices are, growers should use their best judgment. When in doubt, consult professionals with experience in energy, water, and waste management in cannabis facilities.
Bottom line: Companies planning to set up a cannabis business in Massachusetts will need to watch the regulatory developments as the industry and state get into a groove. Observers looking to predict the future should understand the state’s keen interest in protecting broader environmental protection goals and continue to do so by helping cannabis businesses reduce their energy and environmental footprint. The good news is, being compliant with the state’s power and environmental regulations will make most companies more competitive, profitable, and more attractive to municipalities.
He has held management positions within two Massachusetts Registered Marijuana Dispensaries in cultivation shortly after the rollout of the MMJ Program. His focus lies in providing the highest quality medicine to patients using best practices.
Having witnessed a considerable amount of waste throughout the industry, he has expanded his attention to include sustainability and waste reduction. He is currently working with an RMD with a provisional certificate and environmentally friendly organizations to further the safe access to cannabis while reducing the footprint.
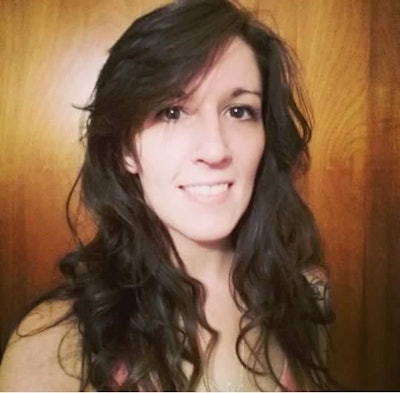
Maggie Kinsella has cultivated cannabis for the last five years. She has a fiery passion for the plant and patients as well as adult consumers. She expanded her knowledge and network attending the Northeastern Institute of Cannabis in 2014 with the first round of students.
Maggie started in Massachusetts cannabis industry as an office secretary for a certified cannabis doctor assisting patients with online registration and medical marijuana cards. Shortly after, she worked for a medical marijuana cultivation facility as a trimmer and advanced to Harvest Supervisor. After a year there, she circled back to NIC to help others expand their cannabis knowledge and employment opportunities in the industry.
She is now freelancing with her partner setting up cannabis gardens for those growing at home as well as working with different organizations concerning energy efficiency and sustainability, health and safety, quality control, and employee rights in the industry after seeing a high level of neglect and waste. Maggie has also sat on the board for MassCann/NORML since 2015 and is the current Press Secretary.
Top photo courtesy of Adobe Stock