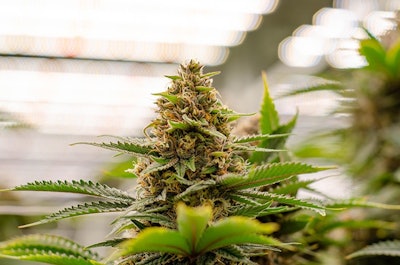
As director of cultivation for Maryland-based Holistic Industries, Nick Denney oversees seven cultivation facilities—soon to be eight—in as many states.
The company’s all-indoor grows range from 15,000 to 30,000 square feet of flowering canopy each and reside in Maryland, Pennsylvania, Massachusetts, D.C., Michigan, Missouri, West Virginia, and soon-to-be New Jersey.
Denney started his career in South Florida. After undergraduate studies in economics and a graduate degree in agronomy, he spent several years in the hydroponic specialty produce industry.
Then cannabis called in 2018. Denney joined Holistic’s Maryland location as assistant cultivation manager. As he advanced to oversee cultivation nationwide, he watched Holistic grow from 40 or so employees to more than 700.
HPS Beginnings
When Denney first started with Holistic, the company used high-intensity discharge (HID) lighting, opting for high-pressure sodium (HPS) for flower and ceramic metal halide (CMH) for veg. Though Denney wasn’t part of the decision-making that chose HPS, he expects it was simply because that was the standard for flowering at the time.
“That’s what people knew, and they knew it worked,” he says. People understood HPS temperature and HVAC requirements, so a certain comfort level was there. In comparison, Denney says LEDs were still considered unproven in cannabis.
Denney’s exposure to LED technology dates back to the first Indoor Ag-Con show in Las Vegas in 2013. He followed horticultural research through the years and watched LED research and development progress.
“But with cannabis, I hadn’t seen any LED lights that were being used, especially for flower. So, it was newer technology. I think people were less sure about it,” Denney says. But he felt it was time for change.
Learning Curves
As cannabis photobiology research and LED technology advanced, Denney lobbied to switch existing facilities from HPS. Around the end of 2019, plans were put in motion to retrofit Holistic’s three cultivation facilities in Maryland, Massachusetts and Pennsylvania.
Increased yields were the main driver behind the push for LEDs. “If we can get more light to the plant up to a certain point, it theoretically should result in higher yields,” Denney says. “What I was seeing in the industry was you could do that with either equal or better quality, all while using less energy per unit of light.”
HPS lighting limited how much light he could get in a room before problems with overheating or morphological issues with plants arose. But with LEDs, he could push that ceiling higher and be more energy-efficient, too.
But retrofits involved more than bulbs for Holistic. “You couldn’t just pull your HPS lights down and plug in LED,” he says. He points to different light counts, different voltages, new electrical plugs and wires required to make the switch. And every facility had different retrofit needs. For example, LED mounting positions meant that fans had to relocate to maintain desired air movement through the canopy.
More changes came later. As yields rose, dehumidification capacity fell short. “As yield goes up, that means biomass is going up, which means you have more water being taken up and released by the plant, which means you have to remove more water,” Denney explains. “We learned quickly and got through the learning curves of new technology.”
Retrofit Goals
Before the retrofits, Denney estimates the three facilities were hitting around 1,000 PPFD in a best-case scenario. He aimed to boost that ceiling by 50% and have available capacity for 1,500 PPFD.
A second goal was to find a vendor that provided the product quality and support he wanted for the company and his growers. “With the quality, we just want to make sure we’re getting what we paid for,” he says. “For the support side, we really like to lean on our vendors to provide that support for their equipment. Because if anyone should know it best, it should be them.”
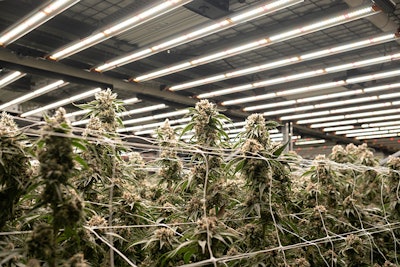
Denney prefers his growers work directly with vendor support teams, not filter everything through him. Growers become more informed and educated in the products, while building important relationships with the vendor teams.
After researching his options extensively, Holistic settled on Fluence for the retrofits—and all lighting that’s gone into Holistic cultivation facilities since. Part of the draw was Fluence’s approach to research and grower education.
“I’m really attracted to companies that are open and want to educate—and not for something directly in return. They were putting information out to the public with really credible researchers. Good, non-biased information,” he says. “… I was attracted to that because I very much like educating people myself or being on the other end receiving that education.” The added benefit of Fluence’s horticultural services team—dedicated to helping growers succeed—confirmed it was the right fit.
The Holistic and Fluence teams worked closely through the entire triple retrofit, from Denney’s initial contact to the project management and real estate teams who help build and design Holistic facilities. All while, Denney’s cultivation goals stayed foremost in layout and design.
Trickle-Down Gains
One big lesson learned is that LED gains affect more than yields. Returning to the dehumidification example, Denney explains that more biomass means more water at every step—not just in your grow rooms. If yields double, there’s twice the water to remove in dry rooms. Then you need space to cure the extra flower, staff to trim it, space to package it and store it—all good problems to have.
“We’ve made it work in every facility, thankfully. But I don’t think we initially anticipated the gravity of those changes,” he shares.
With Fluence LEDs running across the board, yields have gone up significantly. Denney now has a new standard for minimum acceptable harvest. And Holistic’s facilities are pushing or exceeding the limit of what he thought was the highest theoretical yield for indoor cannabis just a year or so ago.
Plants are bigger and more vigorous. Better light penetration, reduced density and increased yields mean fewer production cuttings, less plants for the same space in veg, and less transplanting into flower. Temperature, humidity, pruning and maintenance have all changed for the good.
Looking forward, Denney continues to draw on horticulture and controlled-environment agriculture research. As yields continue increasing, he’s focused on quality and end-user experience. “How do we continuously improve that part of the equation as well?” he says.
Wherever the future takes it, Denney says he’s excited to see what’s next.