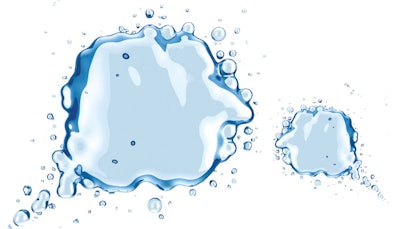
When it comes to water, growers should plan on having redundant systems, a 24/7- response service contract, storage for multiple days of normal operation—or all the above. Never running out of clean water is not just a goal, it is a key performance criterion. Here are eight steps to help make it possible.
1. Treat Your Water Properly
Determining how much treatment any source water requires begins with knowing what the water needs to be for good growth. Plants don’t need perfect water—not even potable (drinking) water—so the minimum requirements define the target production water.
The next step is to run lab tests to learn what is in your source water, including:
- levels of mineral content,
- alkalinity and pH,
- heavy metals,
- radiation and
- biologicals.
Comparing the test results to the target water levels allows the grower to see where levels are high and in need of treatment. Those treatments may include filtering, reverse osmosis (RO), ionic resin exchange columns, ozonation, acidification or UV light sterilization. Be sure that designs treat everything that needs to be treated and nothing more.
Water storage requires cleanliness. Water held for more than a couple of days should be monitored or treated with biocides such as chlorine bleach, hydrogen peroxide or ozonation to discourage biological growth. (Editor’s note: When using organic-based amendments, avoid using hydrogen peroxide, “as it will kill all beneficial bacteria and desired life forms in addition to pathogens,” writes Kenneth Morrow, owner of cannabis consultancy Trichome Technologies, in his book, “Marijuana Horticulture Fundamentals.”) Holding tanks need to be drained and cleaned with disinfectants on a regular schedule.
2. Utilize Smart Design
Water-system design is no secret, and information to help growers is plentiful from various sources. It involves a straightforward set of calculations that translate delivery requirements into a physical system.
Investors and managers should have high expectations of any water system—from cleanliness to a stable delivery rate over a prolonged period—and should deem the system operational and up to quality standards before formally accepting and paying for it.
Water-system suppliers should be contractually required to meet all specified water-delivery parameters.
3. Consider Safety
Safety first, safety always! Safe water-delivery systems start with backflow prevention where the water supply enters the facility. All pressurized water lines should be given the same respect as electricity—water lines can be subject to corrosion, leaks, clogs and freezing, among other problems, and should be frequently examined and well-maintained.
Water left on floors is a leading cause of falls in the horticulture workplace.
Tanks that employees must enter to clean require a two-person team, so no one gets trapped inside.
4. Create an Energy Plan
The cost of moving water depends on how much water must be delivered at any given time and how long the system must run. A system that delivers water to all rooms at once requires more pump capacity delivery to one room at a time. Likewise, a system that delivers all water in 15 minutes requires more pump capacity than a system that spreads water delivery across 12 hours.
Drip systems can be designed to keep up with transpiration rates. A rapid drenching approach minimizes system run time, but any system must provide specific amounts of water at specific rates. So, once the system has been defined, growers can size the pumps, along with the electrical service required to operate them.
Aside from the cost of pumping liquids around the facility, water temperature could become another significant bill. Nutrient mixing is aided by using warm water to raise the solubility of dry fertilizers. At production scales, the cost of warming water is significant. If water does need warming, look for a way to preheat the water for free to reduce energy usage. One way is by exposing storage tanks for incoming source water to the sun. Doing so can shave a surprising number of dollars off the energy bill.
5. Enhance Nutrient Delivery
Fertigation is the only real lever a grower must pull to control growth. A reliable water-distribution system is the perfect platform through which to deliver essential mineral nutrients to plants. Numerous ways exist to mix nutrients to the proper concentration—from direct mixing of dilute solutions to concentrated A/B and multi-tank “single element” systems, all of which produce a pipe filled with a diluted nutrient solution that contains a known amount of each mineral nutrient (according to the grower’s recipe) in each gallon of solution.
Along with the knowledge of how many gallons of water each plant gets, a good water-delivery system lets the grower know how many milligrams of each nutrient the plants receive in each fertigation period. The grower knows to increase nutrients relative to water to make the plants grow faster and to decrease the concentration for slower growth. Nutrient mixing is not a complicated process, and nutrient recipes don’t change much once set. We suggest growers find the most reliable way of mixing the solutions, not necessarily the most flexible.
Prepare to Control Fertigation
Water delivered per plant is the principle feedback we look at with fertigation systems because it encompasses all variables that affect water usage and nutrient delivery. Each gallon of nutrient solution contains so many milligrams of each of the essential mineral nutrients according to the solution’s recipe. The amount of mineral nutrient per gallon of solution, times gallons delivered, is the total amount of each nutrient delivered to the plant in that crop cycle. When the mention of PPMs (parts per million) causes eyelids to close, grams or pounds of a mineral given per plant is an intuitive way of looking at nutrient delivery.
Once a cultivator has discovered how much water the plants need, all he or she needs is a timer to control the fertigation. That can be implemented in the form of hand-operated valves to fully automated activators, but all merely control run time.
Perform Regular Maintenance
After nutrient mixing, the system’s mission is to deliver the “salt-water” nutrient solution to the plants. Nowhere is the salt water more noticeable than on drip emitters and leaky connectors: They crust if not maintained properly. Crust buildup on emitters is a function of nutrient concentration, so if a grower is running nutrient solutions with ECs above 2.0, he or she needs to monitor for crusting and be prepared to implement an anti-crusting cleaning protocol. The frequency of crusting treatment may be reduced by removing emitters from their spaghetti tubing or using drip tapes, but crusting will still occur even with these approaches. Even if weak compared to sea water, nutrient solutions will corrode any metal they touch, so pipe connections should be stainless steel or plastic wherever possible.
Pipes become damaged and connections spring leaks. When they do, it is good to have a shutoff valve close by. A few moments spent during the design phase envisioning a burst pipe/valve scenario and how best to mitigate it will place shutoffs in positions where they could potentially save a crop.
Some systems are pump eaters. We experienced a case where improper plumbing resulted in sudden pressure drops in the pump exit piping, resulting in the phenomenon known as cavitation—which “ate” (collapsed) the steel exit piping and pump rotor. After losing a few pumps in a short time, a switch to pumps with ceramic rotors and changes to the outlet piping solved the problems. An experienced piping designer would have known to flag designs that could promote cavitation and other problems. Piping systems aren’t as easy as they look, so find a professional to review plans.
8. Dispose and Reclaim
The “easy-to-do” tip here is for indoor cultivators who can capture and reuse chiller condensate. Given that condensate represents a considerable portion of the water given to the plants every day, significant water reuse can be achieved.
Low to no drain-off systems (for example, peat or coco-based systems) produce little waste solution to dispose of. With significant waste water, follow local rules before the waste water is put down drains or released outside. Discharge of water into sewers or streams is heavily regulated, and pretreatment of discharge may be required.
Nutrient solutions require processing through RO, distilling or other treatments to remove nutrient ions from the water. With nutrient costs being as low as they are, nutrient reclamation may not make sense financially.
A reliable watering system may be the single most important part of a cultivation facility. Being able to rest assured that plants will never be without water is worth every penny spent to attain that reliability and peace of mind.