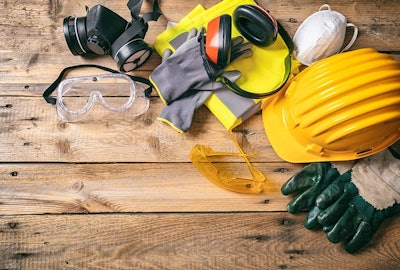
Cannabis cultivators use standard operating procedures to keep their plants safe and healthy, so it only makes sense that they should pay attention to the safety of their workers, as well.
Personal protective equipment (PPE) is one way to protect employees against chemicals, falls and other common hazards in cultivation facilities. Every facility should have an employee dedicated to safety to protect the well-being of the staff and comply with state and federal laws, according to Roberta Smith, occupational health program manager for the Colorado Department of Public Health and Environment.
“That might not be the biggest role that people think of when it comes to a cultivation, but keeping workers safe is just as important as keeping the plants safe,” she says.
Laws regarding safety vary state by state, Smith says, so cultivators should reference their specific state guidelines before implementing a safety program and PPE at their facility. While some states follow Occupational Safety and Health Administration (OSHA) guidelines put forth at the federal level, others have state OSHA plans that override the federal rules.
RELATED: How to Ensure Your Facility’s Safety Program is Compliant and Effective
In Colorado, the cannabis industry is regulated by OSHA at the federal level. OSHA requires cannabis cultivators to perform a hazard assessment in their operation to determine what hazards exist. If there are chemicals being used, for example, or other hazards present, business owners should generally try to eliminate the hazards before implementing PPE, which should be used as a last resort if hazards cannot be removed, Smith says.
When PPE must be implemented, it can include the use of gloves, coveralls and respirators when handling pesticides, for example. The Environmental Protection Agency (EPA) has a Worker Protection Standard guideline that can dictate which type of respirator is required with which pesticides, Smith says.
Slip-resistant shoes are another example of PPE and should be worn in cultivation facilities where the floor is wet to avoid slips, trips and falls. Some facilities also require employees to wear Tyvek sleeves, or at least long-sleeved shirts, when they harvest because the stickiness of the terpenes can cause skin sensitivity, Smith says.
“I think the key message is every cultivation facility is going to be different,” she says. “[Operators should be] looking at each task and understanding the hazards of each task and then what is going to be required to protect the worker.”
If employers do not follow applicable laws and protect workers against potential hazards, they could face OSHA citations, Smith says. Fines vary state by state and depend on the violation, but if a worker files a written complaint to OSHA, the organization will investigate, either in person or in writing.
Employers should pay close attention to OSHA’s general duty clause, Smith adds, which says that if an operator is aware of a hazard in the workplace, he or she must take steps to protect employees against it.
“A lot of things can fall under that general duty clause in regards to PPE and protecting the worker,” she says. “There are specific PPE standards within OSHA for glove use. There’s a respiratory protection standard. … If you are using respirators in a facility and you’re requiring employees to wear respirators and you don’t have a written plan, that can be a citation, and in fact, that generally falls under OSHA’s top 10 violations, not adhering to a respiratory protection plan.”
But even the best laid plans can derail if employees don’t use the required PPE. Training is essential to ensure that employees know how to properly use and maintain their equipment. Safety training generally happens when a new employee starts his or her job, but it should also occur if a process changes within the facility, Smith says.
“If you get, let’s say, a new bud trimming machine, people should be trained on how to use that appropriately,” she says. “If there are any changes in respirator use, you need to have training then.”
Training should also happen on an annual basis, she adds, as a refresher course on the company’s safety policies.
And once trained, employees need to do their part to ensure safety, Smith says. “If your employer is requiring you to wear PPE, it’s because there’s a hazard that has been identified,” she says. “If you are using PPE, it’s there for a reason, and it’s probably the most fail-able aspect of the whole hierarchy of controls, we call them, because it involves humans. People forget, or people won’t wear their PPE appropriately. It’s very important if an employer has chosen PPE for you to wear, that you wear it appropriately. If it needs to be cleaned and maintained, that you know how to do that, as well, because if PPE is cracked or torn or fails, it’s not going to protect you like you think you are being protected."