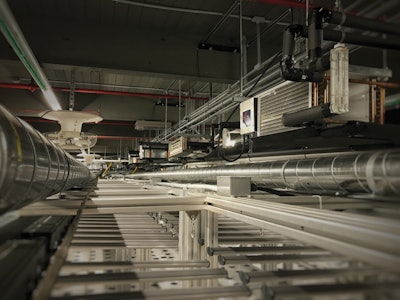
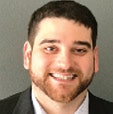
The following case study is sponsored by Surna.
Andrew Lange’s methods to efficient cannabis cultivation are slightly different than that of most indoor commercial operations throughout the United States.
Black Diamond Biotech, a Tier 3 cannabis producer and processor in Shelton, Wash., utilizes an aeroponic growing system in its 72,000-square-foot facility. This means that rather than using a growing medium such as coco coir to cultivate cannabis, Black Diamond sends misted air packed with nutrients to the plants’ roots, providing them with everything they require to flourish.
Each room contains about 4,000 plants stacked on 140 to 145 movable tables outfitted with aeroponic system hardware, nutrient and fertigation components, and LED lights. The system utilizes sensors that monitor 380,000 data points per hour, helping the cultivation team effectively track factors such as temperature, humidity, carbon dioxide level, vapor-pressure deficit and more.
Compared to a traditional indoor hydroponic operation, this type of cultivation can produce excess humidity in the growth facility because the plants are fed every 30 to 60 minutes as opposed to once a day. Additionally, plants grown this way transpire quite often, releasing the moisture they have collected back into the air after absorbing the nutrients they need.
“We use about 90 percent less water than you’d use in any other hydroponic system,” Lange notes. “Our facility is water-neutral, because we harvest more water from the air than we use.”
With so much moisture in the mix, Lange knew he needed a reliable climate control system to deter pests and prevent diseases from festering. He turned to Surna—a company he’d worked with previously through his other consultancy business, Ascendant Management—to outfit Black Diamond’s operation with equipment to keep excess moisture at bay, holistically.
To maintain desired climate control levels, Lange uses Surna’s industrial chillers and fan coil units.
“Surna’s entire climate control package is based on glycol cooling, so it uses water and a glycol mixture that gets distributed to the units,” explains Lange. “So instead of a traditional air handler, where it’s just pulling air into a condenser and there’s a refrigerant line, we’re bringing warm air into chillers that are outside the building, so they can chill the glycol.” The glycol is then pumped through air handlers as it passes through a radiator, cooling the air, which is then returned via a closed-loop system to each growing room. Lange says this reduces biological risk, because the plants are never exposed to outside air.
If we don’t have to move any air between the rooms, we don’t have to worry about cross-contamination.” — Andrew Lange, owner, Black Diamond Biotech
“If we don’t have to move any air between the rooms, we dramatically reduce the risk of cross-contamination,” he adds.
Surna’s fan coils help regulate the humidity of each room, keeping fluctuation to a minimum. V-Flow fans circulate the air, preventing the development of dead spots where moisture could collect.
Because Black Diamond Biotech’s rooms are considered “clean rooms,” air purification is another key concern. The air goes through multiple filters, including high-efficiency particulate air filters, and is treated with ultraviolet light before being redistributed to the plants. Surna’s air sanitation units contribute to Black Diamond’s biosecurity by removing potentially contaminating particles from the environment.
Black Diamond’s automation methods, including the incorporation of closed-loop climate control with Surna products, have also led to significant cost savings in labor. With only about 15 employees working in the facility, Lange says his company has realized an “80-percent reduction over other types of grow methods.”