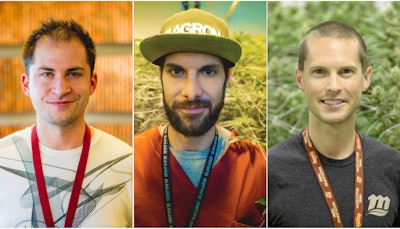
Mayflower Farms acquired a former storage warehouse in Aurora, Colo., in 2015, says Compliance Officer Mark Troutman, and he adds, “we … spent 13 months building out the best facility the Colorado cannabis community could produce.” Troutman says they doubled the space of the original structure, which sat at 24,000 square feet, by adding a second level. The facility, which features 40-foot ceilings, now boasts 48,000 square feet of cultivation and post-harvest production space. The second level-which Mayflower Farms uses for harvest, cure and extraction-is modeled after a commercial kitchen. (In other words, they take sanitation very seriously.)
“We’re uniquely positioned to succeed long term in the Colorado cannabis space due to our integrated cultivation and extraction facility, which is highly adaptable,” Troutman says. “[We’re] able to move quickly on trends in product development.”
Right now, Mayflower Farms produces wholesale buds and trim, and concentrates such as live resin, wax and shatter. But how has its approach to cultivation and extraction helped pave the company’s way into the state’s competitive cannabis marketplace? Cannabis Business Times writer Jillian Kramer spoke with Troutman, as well as Drew Greco, Mayflower Farms’ garden manager, and Travis Ingraham, the company’s head of processing, to find out more.
Jillian Kramer: Why did Mayflower Farms decide to use hydrocarbon extraction?
Travis Ingraham: Hydrocarbon extraction is a high-yielding and time-efficient extraction method for cannabis. The solubility of the cannabinoids in hydrocarbon solvents allows us to make high-potency extracts with minimal post-processing required. We find that we are able to capture the essence of the strain using this method, followed by gentle purging [which removes the solvent].
We have developed our gentle purging methods to use the lowest heat, vacuum and time realistically possible. This allows us to
save as many terpenes as possible, while still delivering a product which has [approved] levels of residual solvent.Kramer: What environmental controls does Mayflower Farms use?
Drew Greco: At Mayflower Farms, each vegetative and flowering room has heat, air conditioning, dehumidification and CO2 supplementation. We have an HVAC system that circulates chilled liquid [in a closed-loop system] throughout the facility to cool our rooms. With pre-programmable minimum and maximum temperature and humidity levels, we can make sure our rooms stay within a 10-degree or -percent variance. This is one of the most important factors in controlling mold and fungus growth. Our CO2 enrichment is controlled and delivered by a fully automated system. This allows us to maintain an even level of CO2 in our rooms during the day when the plants need it, and turn off the CO2 at night while the plants sleep.
Mark Troutman: CO2 levels are monitored in each flower room by a CO2 gas-detection sensor that operates like a thermostat. When the CO2 concentration in the room drops to an indicated low point, the system kicks on and introduces bottled CO2 into the room until the indicated high point is reached, and then it shuts off. The room will slowly drift back to the low point and it starts again. The system also includes an optical sensor that detects whether the lights are on. We don’t introduce CO2 into the rooms when they’re dark, as the plants are said to be “sleeping” and do not respirate as actively in the dark.
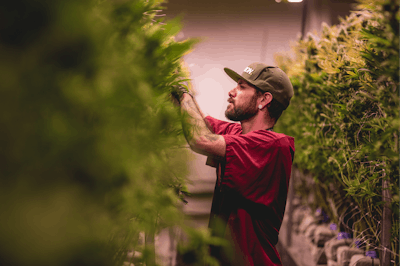
Kramer: What makes Mayflower Farms’ facility state-of-the art?
Greco: [It] was designed to be a cultivation facility. We did not just take over a warehouse and throw up some lights. Each individual room was designed for optimal air movement and environmental control. We believe that multiple 70- to 100-light rooms allow us to control the environment properly, resulting in a higher-quality finished product.
Mayflower Farms’ vegetative and propagation rooms are centrally located in the building, allowing for a smooth production flow when we move plants from vegetation to flower.
We have five flowering rooms that are all individually climate controlled and fertigated. [Outside of] each room is a 300-gallon reservoir … with an irrigation pump plumbed into the room. Each table in every room has an irrigation line and drip emitters that are pressure regulated to deliver an equal amount of nutrients to each plant.
We have an industrial elevator lift to transport plants up to our harvest room [on the second floor] for processing.
Ingraham: The build-out of our facility was designed with one purpose in mind: creating the ideal space to grow large numbers of plants and produce large quantities of concentrates. … This can be observed in every detail of [our] layout and construction-nothing is an afterthought.
Our extraction lab is designed to be fully compliant with … regulations regarding [Class 1, Division 1] classification [editor’s note: for hazardous locations, determined by the Occupational Safety and Health Administration (OSHA), “depending on the properties of the flammable vapors, liquids or gases … that may be present therein and the likelihood that a flammable or combustible concentration or quantity is present,” according to OSHA.gov]. Hydrocarbons are monitored in the air and [during] every step of our process to ensure a safe working place for our employees.
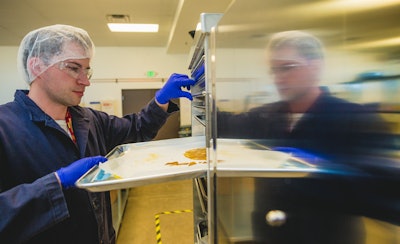
Kramer: How does your team determine if tweaks—whether to cultivars or recipes—are needed?
Greco: Our cultivation managers—Willy Gardiner, Drew Greco and Ryan Salnoske-have been working together for [more than] two years as a team to try and perfect a simple, yet well-rounded commercial cultivation SOP [standard operating procedure]. A major part of that SOP is plant inspection and health. We strive to create near-perfect environmental conditions as well as a complete feed schedule so that our plants thrive. We are striving for a clean, safe and potent product with every room we harvest.
The Mayflower Farms cultivation team works together to pair strains that feed similarly into a room. We can then adjust our feeding schedules to best fit the needs of each room.
Troutman: Each different cultivar feeds differently. Some strains require more nitrogen than others, while some strains may require more calcium than others. [For example,] OG Kush wants less nitrogen than other strains. This is why it is so important for growers to be able to recognize deficiencies, as well as toxicities, in plants. The plants will let you know through subtle indications what they need and what they don’t like. This is why cannabis growers develop such intimate relationships with their plants.
Kramer: Your cleaning procedures are modeled after those used in food-manufacturing facilities. What exactly does that mean?
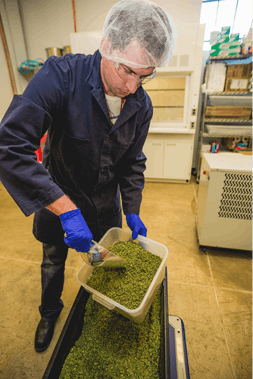
Greco: We want to produce the cleanest product possible, and that means maintaining a clean cultivation environment. We only use cleaning products that are allowed for use in commercial kitchens or hospitals to be sure our facility is as sanitary as can be.
The Mayflower Farms cultivation team implements daily cleaning procedures and checklists to keep the facility looking cleaner than most. Maintaining a clean work environment is not only beneficial to the plants, but also the workers. Our cultivation team takes great pride in our facility, and we strive to keep it well maintained.
Ingraham: Coming from a background in cGMP [current Good Manufacturing Practice] nutraceuticals production in a [Food and Drug Administration (FDA)]-regulated facility, it was obvious to me that sanitation in the cannabis industry was lacking. All dishware used in [our] processing is cleaned and sanitized to FDA food-grade production standards. Hair nets, lab coats and booties are worn by all employees to prevent product contamination.
We chose to model our production to this higher standard because we believe our customers deserve the cleanest, safest extracts. We produce extracts for use in edible formulations by third-party companies, [and those] require a high level of cleanliness. It is also our belief that this is the direction all cannabis production will go in the future.
Kramer: Buds that you don’t consider top shelf become part of your extract products—how do you decide what doesn’t make the cut?
Ingraham: For sales at dispensaries, we are looking for large, dense, well-manicured buds. While we make every effort to ensure that there is as little flower produced that does not meet these criteria, there are buds lower on the plant that do not fill out as much. These buds still have significant levels of cannabinoids, but they have not developed the density we-and consumers-look for in shelf-ready buds. This flower is combined with any sugar leaf that is removed from the premium buds during trimming to create the perfect starting material for top-notch extracts.
Kramer: What led to your decision to use predatory bugs for pest control?
Greco: Our No. 1 goal … is to produce a clean, safe and potent finished product. … We use a lot of essential oils [such as rosemary oil, geraniol oil and peppermint oil] in the vegetative stage to help prevent powdery mildew and mold in the flowering stage.
We use multiple strains of bacteria and fungi to help boost our microbial colonies at the root zone. Since the root zone is the most important part of the plant, we want to ensure the healthiest roots, to produce as much flower as possible.
… Beneficial insects [such as Hypoaspis miles and Cucumeris] keep our garden clean. The insects are brought to us in little porous pouches that we hang on the bottom branches of the plants. As the bugs run out of food in the pouches, they exit the pouch to search for a food source.
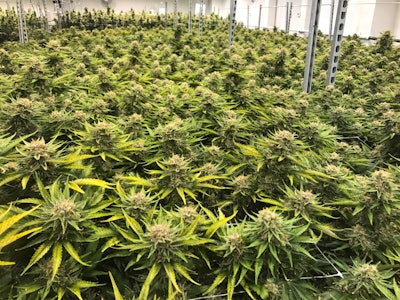
Kramer: Research and development (R&D) is a large part of Mayflower Farms’ process. Tell us more about what the chemists in your lab do.
Ingraham: Currently, we have three full-time scientists employed in our extract lab. Recently they have been developing methods to increase yields, potency and flavor. In addition, blends of various strains are being explored for unique flavor combinations as well as effects. In the next year, the R&D will move into the development of unique products and formulations.
Kramer: What is your most unique product?
Greco: We have a range of strains and concentrate products to choose from. … But our most unique product is probably our live resins. To create this amazing product, we first harvest whole plants and freeze them quickly. By freezing the flowers fast, the terpenes in the flower are preserved in their “live” state, resulting in a product that smells and tastes more like the profiles of the live plant.
Ingraham: Our live resin definitely sets us apart. We are able to process our plant material as quickly as the state’s testing statutes allow us to. ... Being located in the same facility, we are able to hand-select the best plants, get them processed and frozen immediately, and keep them frozen up until the moment of extraction. This allows us to get terpene profiles and yields that many companies struggle to get.
Our sugar wax is definitely our most unique product currently, though others are in the works. ... The specific extraction and purging process we use to create our sugar wax is unique and intentional, giving our extract unparalleled flavor.
Troutman: Plant material from a harvest must be tested for potency and microbial contamination before it can be transferred from a grow to an extract lab. Since we are one integrated team, the extract lab has direct access to the grow’s test results.
Kramer: You provide comprehensive explanations of every strain you sell on your website. Why do you think it’s important to give so much information to your customers?
Greco: We believe it is part of our job to help educate customers. We want [them] to know the differences between a sativa, indica or hybrid strain, ... [and] between a high-THC or -CBD strain and a high-terpene-percentage strain. We want the customer to know exactly what they are getting so that they can make educated decisions on what products are best for them. This also means that we have to produce a consistent quality product, so that the customer experiences the products in a similar way every time.
Ingraham: We believe that it is critical for people to know about the products they consume. The more information a consumer has … about the products they are looking for, the more informed decision they can make when purchasing. This information could be the difference between a consumer purchasing a product they love the taste and effects of, or purchasing a product that leaves them wanting more-or less. With so many different flavor profiles, and physical and mental effects produced by the strains in our portfolio, this information gives consumers the ability to choose what is right for them and gives them information to find similar strains they may also enjoy.