_fmt.png?auto=format%2Ccompress&fit=max&q=70&w=400)
It’s no secret that indoor cannabis cultivation is energy intensive, requiring significant lighting, ventilation and climate control, for starters.
A well-known study published in 2012 in Energy Policy journal found that legal indoor growing operations accounted for 1 percent of the nation’s total electricity use and produced 15 million tons of greenhouse gas emissions (CO2), the equivalent of operating 3 million cars—and that was when only 15 states had legal medical marijuana programs, and before recreational cannabis was legalized and a glut of new growing operations came online.
Here, three cultivators who recognized and worked to change the environmental impact of their indoor grows share insights into their efforts to grow cannabis as sustainably as possible.
Juddy & Danielle Rosellison
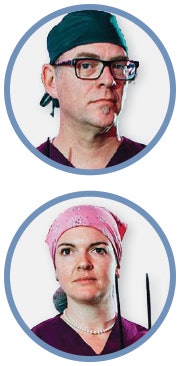
Trail Blazin’, Bellingham, Washington
For Juddy and Danielle Rosellison, cultivating cannabis is more than just a business, it’s a chance to rethink capitalism.
“The industry has a chance to set a new standard for how capitalism is done,” Danielle says.
A big part of cultivating right means focusing on sustainable techniques, according to the Rosellisons. Since launching Trail Blazin’ in 2014, the husband and wife co-owner/operator team have installed LED lighting and a water reclamation system in their pesticide-free facility in Bellingham, Wash.
“We started growing [for the medical market] before LED lights were ‘a thing,’ and the few that were out were so expensive,” Juddy recalls. “Back then, we weren’t growing on a big enough scale to worry about investing in efficiency,” or infrastructure, adding that limited technology also stymied sustainability efforts.
That changed with Washington state’s passage of Initiative 502, which legalized adult-use cannabis.
With a license for 10,000 square feet of canopy, the Rosellisons knew sustainable cultivation needed to be top of mind not only to reduce electricity costs, but also to ensure their operation wasn’t putting undue pressure on the planet. “We only have one planet, and we wanted to get it right from the get-go,” he says.
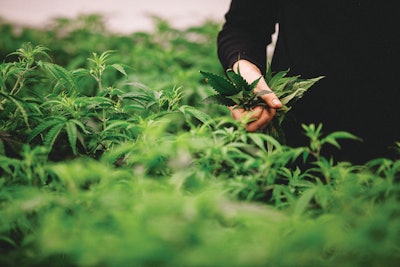
Other pressures also helped them prioritize. “We were worried that regulations could happen on a state or national level to try to minimize the cannabis industry’s impact on the grid, and we wanted to put ourselves ahead of the curve,” Danielle explains.
Trail Blazin’ operates in a two-level, 17,000-square-foot building that includes three flower rooms and two vegetative rooms. Installing high pressure sodium (HPS) fixtures wasn’t an option because the low ceilings prevented adequate space between the lights and the plants, so the couple opted for LEDs, before focusing on water reclamation.
During the average flower cycle, plants are watered 20 times, each using up to 250 gallons of water. Juddy designed a simple system that recaptures the water from the air conditioners and dehumidifiers and, instead of sending it down the drain, reuses it for subsequent waterings. The process has reduced the company’s water use by 90 percent and cost less than $500 per room in materials, according to the couple.
Trail Blazin’ eschews pesticides in favor of biological pest control techniques. The facility was built from scratch with a focus on keeping pests out. Juddy notes that cleanliness and sanitation are part of the company’s integrated pest management (IPM) program and also reduce pest pressures.
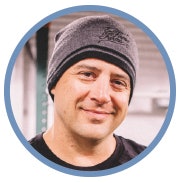
“We don’t make these changes because of the money; we make them because they are the right thing to do,” Danielle says. “Money is the byproduct.”
Jesse Peters
Eco Firma Farms, Canby, Oregon
When Jesse Peters was selling medical marijuana in Seattle, he watched other cultivators go into dispensaries with bags of unlabeled product that had no information about the growers.
“It was just a bunch of people wanting to sell their cannabis,” he recalls.
Peters wanted to sell his cannabis, too, but he wanted to stand out from the crowd. He created the Eco Firma Farms brand and focused on sustainable cultivation methods, hoping to reduce carbon emissions and produce cannabis that had minimal impact on the planet.
“I realized that if we were growing cannabis in a way that destroyed the planet for a profit, we were no better than an oil [petroleum] company,” he says.
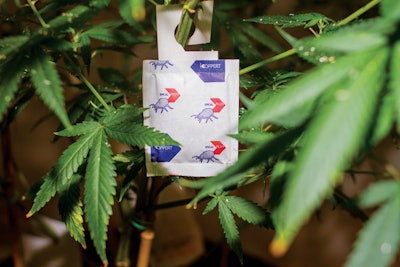
Eco Firma Farms occupies a 23,000-square-foot warehouse, powered by Portland General Electric (PGE). The utility offers customers the option to purchase wind power—a switch Peters, Eco Firma Farms’ CEO, was eager to make.
Peters agreed to pay the regular PGE rate plus $2.50 per 200 kWh of power to source electricity from local wind farms. In 2017, Eco Firma Farms purchased 236,340 kWh of wind power, preventing more than 373,197 pounds of CO2 from being released into the atmosphere.
Even with the additional fee, Energy Trust of Oregon estimated that Eco Firma Farms saved $63,000 in utility bills by switching to renewable energy.
“Ninety percent of the CO2 emissions produced by cultivators come from power use,” Peters says. “Making the decision [to switch to wind power] was easy.”
This fall, Peters plans to add a 250,000-watt solar array to help generate electricity for Eco Firma Farms, furthering his commitment to sourcing alternative energy for cultivation.
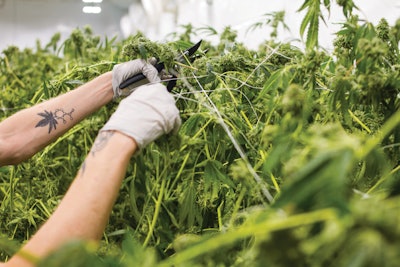
Once renewable power was secured, Peters turned his attention to the second biggest environmental challenge: waste.
Eco Firma Farms wants to reduce waste to the point that it can eliminate garbage service. To achieve that goal, the farm uses recycled products and cultivates relationships with suppliers that sell nutrients and soil amendments in recycled or reusable packaging. However, Peters admits that keeping products out of the landfill is a significant challenge.
“Not all companies are on board [with recyclable packaging],” he explains. “We make a big effort to source responsibly, but sometimes we have no choice, and we end up buying products we need and putting packaging in the trash.”
Like other indoor cultivators, Peters has also focused on energy-efficient lighting. LED lights are installed on all lower tiers of the multi-level grow rooms. Double-ended HID lights power the top tier.
Despite critics warning Peters that yield would drop with LED lights, he hasn’t found that to be true. In fact, he notes, “We’ll never turn back.”
“The steps we’ve taken toward sustainability allow us to grow a far superior product far more efficiently,” he says.
As for the future, advancing the company’s eco-friendly efforts remains a priority at Eco Firma Farms. Peters hopes to add a full-time sustainability expert to help the farm achieve carbon-neutral status.
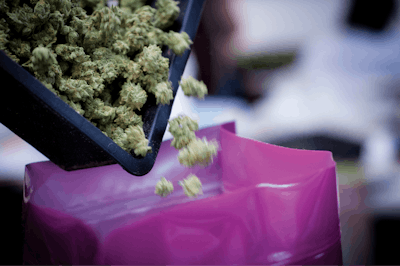
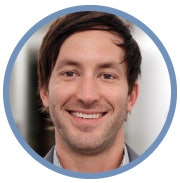
Photo courtesy of THC Design
Ryan Jennemann
THC Design, Los Angeles, California
Ryan Jennemann, owner of THC Design, a cultivation company in LA, got the idea to use aquaponics to grow cannabis from an article he read in a cannabis publication about a European cultivator who had success with the closed-loop method. (Closed-loop is a method of production in which inputs, such as water and/or nutrients, are treated and recycled back into the same growing system, thus conserving natural resources.)
The article was published long before legalization. Jennemann didn’t want to take the financial risk of investing in aquaponics for his small home-based growing operation, but he found the concept intriguing, so he purchased a 10-gallon aquarium and started growing herbs in the windowsill of his Oklahoma home while fish fertilized the roots.
Fast forward to the present, and Jennemann now uses aquaponics to grow cannabis on a commercial scale. He set up an 800-gallon tank in the reservoir room of his 20,000-square-foot indoor cannabis farm. Catfish swim in the tank, and as their nitrogen-rich waste builds up, it’s fed to the plants.
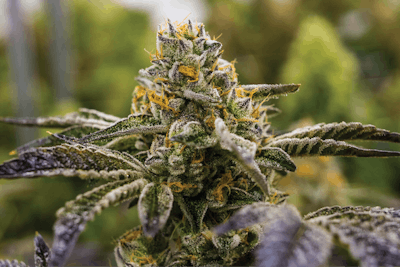
It’s the latest in a long list of sustainability initiatives Jennemann has implemented at THC Design.
Jennemann launched the Organico Revoluce collective in 2010, which was restructured as THC Design in 2014. He has emphasized sustainable cultivation from the beginning, and while it’s taken a lot of trial and error to get the right systems in place, the environmental controls are paying dividends, he says.
In addition to aquaponics, Jennemann built a sophisticated water-reclamation system to collect all of the water from the air-conditioning unit and dehumidifier and recirculate it back into water reservoirs instead of letting it run into the groundwater.
But those initial attempts to recapture water failed.
Despite struggles with sedimentation and algae growth, however, Jennemann refused to give up.
In 2015 after looking to other industries for inspiration, Jennemann made significant changes; he learned hospitals use UV lights in their ductwork to sterilize the air, and some aquariums require UV lights to control algae. THC Design now utilizes UV lighting in its water-recapture system.
The water line that runs between the air conditioner, dehumidifier and the main reservoir also has a 200-mesh count UV filter.
Together, these technologies help filter out impurities, reduce sedimentation and prevent bacteria from growing. On a humid Southern California day, the system can achieve up to 75-percent water recapture, providing up to 1,500 gallons of the 2,000 gallons of water THC Design uses daily.
A bin of black soldier flies helps keep garbage out of the landfill. The larvae are voracious eaters that feast on items like plant cuttings and cardboard. The larvae are later fed to the catfish in the aquaponics system.
Pest control is also organic. Applications of fish oil, sesame oil and garlic oil suffocate bugs feasting on cannabis leaves, and beneficial insects help battle fungus gnats and other pests.
“We spray three to four times a week as a preventive. If we have an infestation, we spray seven days a week,” Jennemann explains.
_fmt.png?auto=format%2Ccompress&fit=max&q=70&w=400)
Organic products tend to congeal in the equipment, leading to bacterial growth, says Jennemann, so equipment cleanings are more frequent and intense between applications.
Due to a combination of more frequent applications and cleanings, Jennemann estimates organic pest control requires up to 15 times more labor than chemical applications, but he believes the efforts are worthwhile because, in his experience, the plants seem healthier throughout their life cycle.
While THC Design can’t obtain certification through Oregon Tilth—a nonprofit organic certification organization that is regarded as having the strictest organic certification standards in the nation—due to cannabis’ Schedule I status with the Drug Enforcement Administration, Jennemann works to implement Oregon Tilth standards throughout his operation anyway.
“I know it sounds trite, but we are truly trying to make the world a better place,” Jennemann says. “You can start a business and make a profit, but if you’re not doing it for the good of the world, what’s the point?”