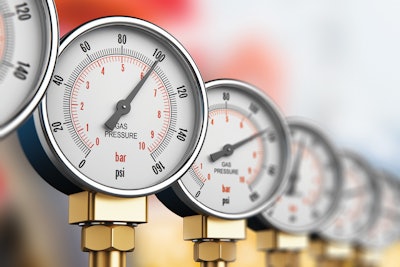
Chris Witherell was walking the exhibit hall at an industry trade show in 2017, drifting past vape pen vendors, lighting manufacturers and dozens of technology companies when he came upon a new extraction equipment company. Witherell, a professionally licensed engineer, struck up a conversation with the vendor and began inquiring about the equipment’s safety certifications.
“We have a peer-review certification,” the vendor said. When the rep added that the review was performed by Pressure Safety Inspectors, LLC (PSI), a Colorado-based company that conducts safety certification reviews and inspection on cannabis extraction equipment, Witherell was perplexed: He owns PSI and had never heard of the company in front of him.
When he mentioned this, the vendor said, “‘Oh, we’re going to give you a call next week,’” Witherell recalls. “But I never heard back from them.”
This is not an isolated incident, says the engineer. Several cannabis equipment manufacturers have been regularly making false and misleading claims about safety certifications, he says, and the buyers are left dealing with the fallout.
Outlining Industry Standards
Any piece of equipment with an electrical component, whether a household item or a manufacturing tool, needs to be certified by an Occupational Safety and Health Administration (OSHA)-approved Nationally Recognized Testing Lab (NRTL). The most commonly used NRTL is Underwriters Laboratories (UL), which typically writes the testing protocols used by the other 17 approved testing labs such as Intertek Testing Services (ETL) or the Canadian Standards Association (CSA). NRTLs focus exclusively on electrical safety codes. When testing electrical equipment or the electrical components of a larger system, UL runs a current through the item to test its capabilities. “They’ll try to start a fire, essentially,” Witherell says.
As described on OSHA’s website, “After certifying a product, the NRTL authorizes the manufacturer to apply a registered certification mark to the product. If the certification is done under the NRTL program, this mark signifies that the NRTL tested and certified the product, and that the product complies with the requirements of one or more appropriate product safety test standards.”
NRTLs cannot certify any non-electrical component of a system, meaning there is no NRTL testing procedure for any extraction equipment such as CO2 or butane/propane extractors like those commonly seen in the cannabis industry. Additionally, NRTLs like UL would not certify equipment or components that were specifically designed for cannabis during the early years of legalization. This lack of oversight led to some “very scary” equipment being sold to processors during the industry’s early years, Witherell says.
In 2014, Colorado created rules to protect processors and local communities by requiring that solvent-based extractors obtain “a report from an Industrial Hygienist or a Professional Engineer that certifies that the equipment, [facility] and standard operating procedures comply with [Marijuana Enforcement Division rules] and all applicable local and state building codes, fire codes, electrical codes and other laws.” This is how Witherell came to create PSI. Since Colorado implemented those rules, several other states have included similar requirements and his business has expanded to 15 states.
When reviewing a system, Witherell examines the product’s specifications, parts list and drawings, and checks whether the system’s mechanics are sound. “We’re looking at each vessel, we’re looking at each piping component, each valve, each chiller, each heater and making sure it’s appropriate for the process and is safe,” he explains.
In supercritical CO2 systems, pressure is the main safety concern. Witherell recalls an instance where low pressure flanges (a projecting flat rim used to connect pressure components) were installed on a high-pressure system. Once pressurized, the flange failed causing the blind flange at the top of the equipment to launch through the roof of the facility and land a block away. “We did the calculations, and they were totally off. Instead of 300-pound flanges, they needed 900-pound flanges,” the engineer says.
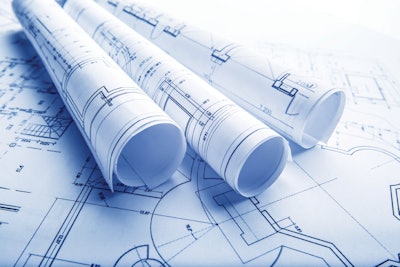
For butane and propane extraction systems, temperature is more of an issue than pressure. These types of systems generally run between 20 psi and 100 psi (CO2 systems can run well above 5,000 psi), but they can reach temperatures as low as -80 degrees Fahrenheit. In those cases, PSI engineers will take a closer look at elastomers (a natural or synthetic polymer with elastic properties). Viton is a commonly used elastomer, for instance, that loses its elastic property at around -30 degrees Fahrenheit. When an extraction system reaches temperatures even cooler than that, the elastomer can fail and leak.
“A lot of folks, especially end users, don’t understand that so another part of this [inspection process] is a field verification,” Witherell says. The Denver Fire Department was one of the first municipalities to require field inspections at extraction facilities to ensure systems are being used as designed. Now, the updated 2018 International Fire Code makes site inspections mandatory around the globe at any facility with such extraction equipment. (Each state manages its own fire code by adopting or adapting the international code. California will make site inspections mandatory in July 2018.)
Staying compliant and certified is an expensive process, says Andy Joseph, CEO of Apeks Supercritical, a CO2 extraction equipment manufacturer based near Columbus, Ohio. He says getting and remaining UL-certified costs the company between $15,000 and $20,000 annually, but the real costs come from becoming compliant. “If you’re starting from scratch, it can take one to two years to come fully in compliance,” he says.
The cost (in dollars and time) to become compliant and certified can easily explain why certain unscrupulous companies have tried to circumvent review processes.
Misleading Messages
Witherell and Joseph have both seen many instances of buyers being bamboozled by vendors who either ignore or are unaware of the regulations. For example, Joseph remembers one company calling him to see if Apeks could help UL-certify its recently purchased (unlisted) system, as the municipality in which it was trying to enter required extraction equipment to be UL-listed or peer-reviewed by an engineer.
“What we were left to say [was], ‘Sorry, you got hosed,’” as a system cannot be retroactively certified, Joseph says. In that case, it is unknown whether the manufacturer intentionally sold an unlisted product or was simply unaware of the rules. Other cases are more cut and dry.“I’ve seen fake ASME certificates for pressure vessels from China,” Witherell says. His team investigated a report from a customer about a manufacturer’s Instagram posts that showed ASME certification stickers with the same serial number. “It turns out the company in China that was making the ASME vessels is not a certified ASME company,” Witherell continues. “They were counterfeiting these tags and putting them on pressure vessels and selling them to the United States to all these manufacturers.”
Some uncertified equipment manufacturers will also try to make it seem like they are certified by using specific language such as “comply with UL standards.” “The words ‘comply with UL’ are misleading,” Joseph says. “If you’re saying you comply with UL, that means that potentially, they are buying stuff that is UL-listed, but the assembly itself hasn’t been evaluated by UL, it hasn’t been inspected by UL, it hasn’t been audited.”
Both Witherell and Joseph advise buyers never to take a vendor’s word on any certification or listing and to verify these claims on the NRTL’s or engineering firm’s websites. (See the sidebar on p. 22 for links to those databases.)
“Don’t believe it unless you see a piece of paper with an engineering seal on it,” Witherell says. Even then, buyers should double-check the online databases. PSI at one point revoked a certification after a company had a design approved, but was using the certification to sell a shoddier, unapproved system. “If the equipment [the manufacturer] sold [the processor] isn’t what we approved, the liability is not on us, it’s on [the manufacturer].”
“If it was a $300 pair of sneakers, it’s a funny story for Facebook. But this is a $300,000 piece of equipment that can make or break a business,” Joseph explains, adding that without federal oversight in the cannabis industry, “There’s nothing stopping people from [making fraudulent claims].”
Silver Lining
Between requirements for UL listings, ASME certifications and peer-review engineering reports, the cannabis extraction market is en route to becoming one of the safest processing and manufacturing industries in the country, according to Joseph. Because there isn’t one NRTL or other organization that looks at every aspect of manufacturing equipment, combining these requirements “is really the best-case scenario that you can possibly have from a safety and security standpoint,” he says.
While no state currently requires equipment to be both peer-reviewed and UL-listed, most states require processors use UL-listed products, and more and more municipalities have been drafting regulations calling for peer-reviews and site inspections.
That is one of the things he tells regulators and industry stakeholders looking to create the safest program: “Get both a peer-review and a UL listing. … You can put both of them together in a complete package.”