The design and construction of a cannabis cultivation facility is a complex process that requires thorough consideration and the input from a diverse team including the owners, operators and professional consultants. And if you choose to retrofit, a variety of items should be considered. The following list, while not exhaustive, serves as a good starting point for the evaluation and layout of your building. Thinking about these items as early as possible in the project schedule will result in a process that is faster and less expensive, and yields a higher-quality and more-efficient operation.
Evaluate the Building to Determine Suitability for Cultivation
Existing buildings come in an infinite variety of types and conditions, each with their own unique set of qualities affecting how well they can be converted into a cultivation facility. Items to review include:
1. Structure Condition: Structural repairs are costly and time-consuming. It’s beneficial to have a structural engineer survey the building to confirm that no deficiencies exist. If rooftop mechanical units are planned, the structure must be evaluated to verify that it has the capacity to support the additional load or if it can be reinforced. If the site allows, it’s often preferred to mount the mechanical equipment on the ground around the perimeter of the building so the roof structure is not impacted.
2. Ceiling Height: A minimum clearance of 10 feet is desired under the roof (depending on the type of lighting used), though having more than 14 feet of clearance is even better. This allows enough room for lighting, ductwork and sprinklers, while still allowing plenty of space between plants and lights.
3. Materials and Contaminants: Older buildings frequently have contaminants such as asbestos, lead paint and mold hiding throughout. These items can be abated or encapsulated to provide a clean envelope (the separator between a conditioned and unconditioned environment), but it will require additional time and money. It’s important to be aware of this upfront so that these costs can be factored into the budget. Wood framing in walls and roofs also can be problematic, as it can affect the project’s allowable square footage or trigger a sprinkler requirement.
4. Utility Services and Capacity: Depending on the building’s previous use, the utilities (water, electricity, sanitary and storm sewers) may not be properly sized or located for cultivation use. It’s important to coordinate with the architect, and the civil, electrical and plumbing engineers to determine your facility’s utility needs early on in design, so you are prepared when evaluating sites. Finding a site with adequately sized utilities can save thousands in design, construction and utility district fees. Going a step further to confirm service from the proper utility districts with ‘Will Serve’ letters is the best way to ensure you have the utilities you need.
- Electrical: Cultivation facilities need a considerable amount of power to handle the lighting, dehumidification and cooling requirements. Depending on the lighting and mechanical systems selected, this can range from 25 watts to 35 watts per square foot. In facilities greater than 15,000 square feet, 480V/3-phase power will decrease the electrical distribution system and allow for a more cost-effective installation. If the utility cannot provide the power needed, options for site-generated power exist, but these are generally expensive.
- Water: The size of the domestic water service to the building will most likely need to be increased to handle the additional restrooms, showers and irrigation system. Depending on the age of the building and the local utility, backflow prevention might need to be added. A sprinkler system may also be necessary to satisfy building code requirements, based on the size, configuration and type of construction.
- Sanitary Sewer: The location, routing, size and depth of the sanitary drainage should be determined. If existing drawings of the system are not available, having a video sewer inspection will provide valuable information on the system’s configuration before design proceeds. Contact the local waste water department, as some call for the installation of waste-water-monitoring stations and have specific requirements on how these need to be installed.
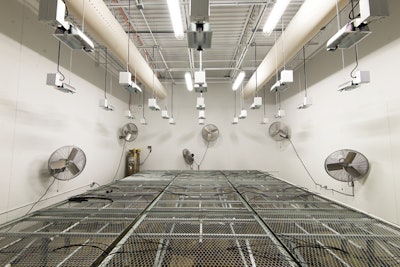
Evaluate the Site for the Best Fit
In addition to the types of buildings available, it’s important to review and compare site constraints when selecting a facility location. A great building space can be nullified by poor site access, poor utility infrastructure or site drainage problems.
5. Site Access and Parking: It is important to find a site that fits your facility’s needs, both for staff parking and ease of access for your business partners (clients, customers, distributors and suppliers). Having adequate space for truck access and movement around the site will make deliveries and pickups easier and more efficient.
6. Drainage and Grading Impact: Water pooling or ponding in the winter is a major concern and a common problem for industrial sites due to the large amount of building area (typically with flat roofs), large parking areas and loading docks. Evaluating a site to determine existing storm water drainage is imperative to avoid damage to the roof, foundation, loading dock areas and parking lot. An ideal site drains away from the building and will sheet flow water or have storm water inlets throughout the outdoor paved areas.
Look at a Schematic Space Layout and How It Will Fit in the Structure
The location and layout of the grow rooms will drive the design of the rest of the building. Sketching potential layouts will help to determine if the building is suitable for cultivation.
7. Optimizing for Efficient Operations: An efficient arrangement of spaces and functions is one of the most important aspects of your design. Carefully consider how the plants move through the building over the course of their grow cycles and processing to help ensure that time and employee productivity are not wasted.
8. Existing Structure and Proportions: Existing buildings typically come with their own peculiarities in how they are laid out. The proportions, exits, column grid and plumbing locations are oftentimes not in ideal locations. During design, it’s important to analyze which elements can be easily modified versus what needs to be worked around. There is a tendency to want to reuse existing elements such as restrooms or offices with the intent of saving money during construction. However, it usually makes more sense to start with a clean slate so that all components can be arranged in their ideal locations and constructed to current standards.
Understand the Jurisdiction Processes Beforehand
Many jurisdictions are still sorting out how to regulate cannabis cultivation. In addition to business practices and financial regulations, cannabis facility development will require local jurisdictional planning, engineering and building permitting approvals.
9. Adhering to Zoning Code: Many jurisdictions don’t have a specific cannabis cultivation facility zoning type, and these facilities can fall into several different use types per local zoning code (indoor agricultural, garden and cultivation, commercial processing, etc.). Careful review of existing and proposed zoning code for your potential site, as well as adjacent parcels, to know what is permitted is a must. Often, renovation projects incur a change in use, which will likely require rezoning or conditional approvals from city or county jurisdictions.
10. Engineering Permitting Is Separate from Building Permitting: Improvements to the site engineering, such as changes to the grade and topography, upsizing or creating new utility lines, and adding access points to the site are all engineering improvements separate from the building improvements. As such, these improvements follow a separate review and approval process, and typically need to be approved prior to building permit approval. Jurisdictions differ greatly in which submittals are required for engineering review, so it’s smart to involve an engineer early and meet with the city or county to confirm the process.
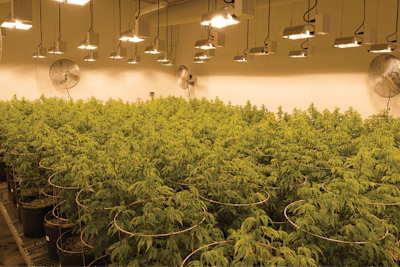
New Construction Must Comply with Current Building Codes
Converting an existing building to house cannabis cultivation or processing will typically be considered a “Change of Occupancy” by the building department, which results in the need to upgrade the building to meet current regulations. A long list of items must be considered, but primary issues include:
11. Area and Height of the Building: Code analysis will reveal if the existing area and height of the building is allowed; if not, there are ways to meet requirements by segregating areas with fire separations or installing sprinklers.
12. Exiting: The number and location of exits is one of the first elements to be established. Once these are determined, the rest of the layout will be worked around them.
13. ADA (Americans with Disabilities Act): All restrooms will need to be upgraded to be ADA compliant. An accessible path is required from the parking area leading into and through the building to accessible areas (bathrooms, breakrooms, offices, etc.). At least one building entry will be required to be accessible, which could potentially mean adding a ramp or lift.
14. Ventilation/Odor Control: The facility will be required to meet the local ventilation and odor-control requirements. The amount of outside (or ventilation) air should be kept at a minimum to reduce the amount of air leaving the facility and requiring odor treatment. Reducing outside air will also help reduce the risk of outside contaminants to the grow areas.
Potential Physical Security Upgrades
Many building-conversion projects are in unpopulated industrial areas and warehouse parks. Upgrading the building’s physical security becomes a major part of renovation and can be addressed with a wide range of options. Some worth considering include:
15. Fencing: The addition of full-perimeter fencing is a simple means of securing access to the building and screening visitors. Depending on the jurisdiction, gate access for vehicles or pedestrians may also be regulated.
16. Entryway: All visitors and employees should enter the building at a single access point that has a security desk or check-in window. Any other required exits should be considered “egress only” and alarmed so that security personnel are alerted if they are opened. If a shipping/receiving area is needed, this should be protected by a fenced and gated enclosure so that loading doors are never open to the rest of the site.
Consider Future Expansion
In many markets, especially states that are just now launching medical marijuana programs, demand is insufficient to justify large cultivation operations. In this situation, it can be best to start with a smaller operation that can be scaled up as the market matures.
17. Phasing: A phased build-out will allow for the most efficient use of your available budget by only completing construction on portions of the building that will be immediately useful. As revenue and demand increases, additional grow and processing capacity can be added. When phasing a project, it is essential to design the entire facility as it will be constructed in its fully built-out state, so that all elements are coordinated, and adequate infrastructure is installed (electrical service, water line, restrooms, etc.). From the full design, you can then work backwards to select the areas to initially build.
18. Site: Selecting a location that has additional structures on-site or space to construct new structures will allow for future expansion with minimal interruption to existing operations. Careful consideration should be given to how the original and new spaces interact with each other to minimize inefficiencies.