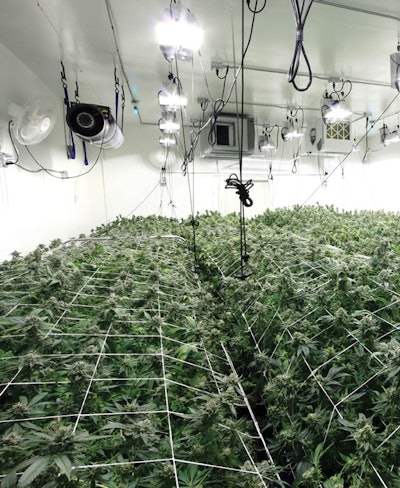
Electricity consumption is a major expense and a hot topic for legalized marijuana, its communities and the energy grid system at large. Unfortunately, to date, articles and panel discussions have focused on the issues, yet have not explored how best to leverage control strategies and best practices of other industries to address the issue.
The good news: The legal marijuana industry can develop environmentally responsible cultivation practices that can change how it generates, consumes and stores energy. The excitement surrounding marijuana legalization already is driving advancements in better-performing and more efficient product technology and equipment used for indoor agriculture.
The other good news: The industry doesn’t have to start from scratch to facilitate change. Cultivators can compare other markets’ energy-management and carbon-emission strategies to help set energy-efficiency standards and enable the use of clean, renewable energy.
Environmental concerns are front and center for many, and especially for the communities in which the industry operates; but energy consumption directly impacts costs, and can mean the difference between a thriving and a dying business.
The energy consumption situation facing the industry is no secret. In 2014, Denver’s energy demand rose from 86 million kWh annually to over 148 million kWh primarily due to the 362 cannabis grow houses established since 2012.
Scientist, research analyst and Ph.D. Evan Mills wrote a report, “Energy Up in Smoke – The Carbon Footprint of Indoor Cannabis Production,” published in April 2011, describing the impact on the utilities market. The report states that indoor cultivators within the United States represent 1 percent of all energy consumed annually. California cultivators represent 3 percent. With California poised to legalize recreational marijuana in 2016, that number will only increase by leaps and bounds.
The electric power demand of indoor marijuana cultivation isn’t a regional grid issue, rather a systemic issue. Communities are likely to implement regulatory controls to alleviate strain on the aging energy grid to contain negative impacts of energy use and to increase environmental sustainability. Some communities already have added energy levies, and if the industry isn’t proactive in addressing this issue, cost of goods will surely increase. Owners of indoor cultivation sites should address energy consumption sooner rather than later, because their future may be influenced by actions taken today.
The first step is to look at energy management—it can reduce consumption and lower costs. Here are 20 steps you can take to better understand your energy consumption and, as a result, learn how to better manage your energy use and costs. If at first some of these steps seem complicated, you will quickly learn that they all support a basic concept of monitoring your energy use and applying often simple changes that will lower your usage and costs.
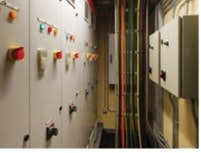
1. Create a strategic energy management plan.
Strategic energy management plans involve coordinated energy procurement and consumption control for financial and environmental objectives. Owners who develop and follow a solid plan will have a distinct advantage over their competitors.
First, establish goals you can track against. Plans include starting (baseline) long- and short-term strategies, metrics and key performance indicators (KPI) that compare the progress of energy procurement, real-time data, controls and equipment performance over time.
Include a review of peak-demand and renewable energy in your plan. Comprehensive plans address peak-demand strategies (energy companies’ highest, overall usage times—which also incur the highest usage rates) and commitment to environmental sustainability, either through energy storage, purchase of renewable energy credits (RECs) and clean, on-site renewable energy production.
2. Review your utility bill.
Once a strategic energy management plan is developed, adherence is required for success. A basic methodology is to audit your utility billing invoices to make sure your goals are being achieved. It’s easy to simply pay your energy bill, and some growers don’t have the time or the wherewithal to analyze it. If necessary, having a staff member handle this, or getting outside help, can pay off in the long run.
3. Understand local rate tariffs.
Utilities serve all eligible customers. They are not required to ensure that the customer is on the correct tariff. Electric, natural gas and water rate tariffs can be complex, but they are worth understanding in order for site-optimization strategies to take shape.
4. Understand your utility bill.
Utility-supplied electricity charges, in the simplest terms, fall into three categories:
- kilowatt per hour (kWh): the rate of energy multiplied by the amount consumed per hour;
- peak demand fee: a fixed kilowatt (kW) rate that is calculated based on the highest 15-minute interval of load demanded during the billing cycle; and
- unavoidable fees for local distribu- tion, transportation and taxes.
5. Items in the bill to review for accuracy.
Accounts payable is doing a disservice to your company if the utility invoices are paid without performing an audit that spots power- and water-usage trends, billing errors, and fee changes—all that can be detrimental to the utility expense budget.
6. Understand peak demand charges.
Peak demand charges and rates occur when a large portion of customers need energy at the same time, resulting in the utility company charging more for the increased production, the strain on the grid’s infrastructure and maintenance—all of which are passed on to the consumer as higher demand (kW) fees.
Since the consumer is charged for the highest 15-minute demand period during the billing cycle (whether or not the level is maintained throughout the billing period), growers can incur significantly higher fees.
Know the local hours when peak demand occurs. It can start as early as 7:00 a.m. and end as late as 10:00 p.m., and is dependent upon geography and energy- resource availability.
7. Educate employees on energy consumption.
Limit exposure to monthly peak demand charges by increasing employee awareness of energy use, conservation and efficiency. The lessons learned can positively impact final product cost and revenue potential. For example, since kW fees are based on 15-minute intervals, teach employees not to turn on all equipment at the same time when they walk in the door. Stagger them in 15-minute intervals.
8. Behavior and process changes can be easy ways to cut costs.
Significantly reducing energy consumption can occur through productivity, behavioral adjustments and process improvements with little or no costs to production. By taking control of energy used in production, the grower reduces costs and the negative impact to the community, energy grid and the environment.
Case in point: The Washington State Liquor and Cannabis Board (WSLCB) has curbed the impact and grid exposure of energy consumption and peak demand through regulatory oversight by limiting facility size and capping the total square footage for the state’s indoor marijuana cultivators.
9. Know what choices are available for buying electric and natural gas.
The Energy Policy Act of 1992 opened the door for wholesale electricity and natural gas procurement through energy deregulation, giving consumers and business choices in energy providers. Of the 28 states that offer energy-procurement choices for all or part of electric and natural gas supply, 18 have legalized medical or recreational cannabis.
10. Energy contract purchasing strategies can be applied for cannabis sites located in both deregulated and regulated energy markets.
Contracts can be written in several ways with terms up to 60 months. Low-risk electric and physical natural gas supply contracts can offer budget certainty with fixed rates and prevent surprises in your bill.
Another option: Block and index, and market index rates float the spot market pricing and benefit from downward market activity, flattened demand spikes and lower energy costs; but they are considered sophisticated strategies that carry increased financial risks. Energy commodity exchange contracts reported by the New York Mercantile Exchange (NYMEX) Price Charts, and Quotes for Futures, Commodities, Stocks, Equities, Foreign Exchange volatility affects the cost of energy at all times. To more easily explain this strategy, it can be compared to a personal investment portfolio that contains different types of financial strategies and products with varying risks and performance expectations that, when combined together, meet the long-term strategy goals.
11. Knowledge is power!
Know when and how you are consuming energy using real-time data management software tools. Tracking energy data in real-time is critical for success when metering, lighting, HVAC, water and environmental controls are included. The metered-level data is empirical evidence used as the basis for a performance contracts’ measurement and verification (M&V) reconciliation used in compliance with local and state regulations.
For example, marijuana licensees in Boulder County, Colo., pay a levy of 2.16 cents per kWh on any electricity or natural gas consumed that is not produced through a community solar garden, on-site renewable energy or by a county-approved equivalent. If empirical data is not provided to the county reflecting the licensee’s participation in the initiative, credit is not given, resulting in a higher energy bill.
In other words, know what drives your highest consumption level and when you’re consuming the most energy, and use this data as the basis for energy contracting, capital expense initiatives and operational changes.
12. Develop standardized energy models.
Growers that develop and utilize standardized energy- and water-consumption models (which establish a baseline energy consumption with “like” businesses and offer a deeper understanding of the industry’s energy consumption per unit of production) to interpret usage data can identify behavior, culture and technological improvements that can reduce energy by as much as 15 percent, as well as aid the community and energy grid providers in forecasting future demand and environmental impacts of cultivation.
13. Use automation controls.
Cultivators can use computer-based building management control systems (BMS) software to automatically monitor and control temperature, humidity and dew point levels of individual rooms. Implementing controls will have a positive impact on the energy budget. Process automation eliminates the potential for human error and over-consumption.
14. Make sure your equipment is appropriate to your site needs.
To maintain optimal growth environments, controls should be added to the mechanical HVAC (heating, ventilation and air conditioning); electrical system; and plumbing system. Keep in mind that over- or under-sizing equipment can significantly affect energy efficiency, costs of production and cash flow.
For example, an oversized HVAC unit is more expensive and consumes more energy than smaller units, but it never has the opportunity to reach peak efficiency. Under-sizing causes premature wear-and-tear on the HVAC unit and it may not perform as expected.
15. Produce and store energy during off-peak hours for use during peak demand.
Energy storage is a great way to reduce energy costs while lessening environmental impact. Storage technology flattens peak demand energy spikes and reduces the cost of production between off-peak and on-peak rates. When a cultivator is on a utility-contracted time-of-use rate, thermal- and battery-storage systems can produce electricity during off-peak hours for use during peak demand the next day.
The storage technology’s low-power compressors operate by using the cool night air, when energy demand is at its lowest, to create and store energy. The next day, the storage unit takes over for the high-power compressors of commercial HVAC to cool the facility. This strategy eliminates both the increased energy consumption and strain on HVAC performance caused during the day’s hottest hours.
According to the U.S. Energy Information Administration (EIA), HVAC is a significant operating expense in commercial building, accounting for 51 percent of energy use.
16. Replace older HVAC units.
Recent advancements in HVAC technology have made the replacement of units, even those just 8 years old, an appealing option for optimal efficiency.
17. Answer questions an HVAC contractor should know.
Most growers have proprietary recipes for success (and growing the best buds). However, it is critical to share certain information and know the answers to fundamental questions prior to meeting with a consultant and HVAC contractor, since equipment manufacturers, climate and geography can affect system benefits.
Tell the consultant or contractor what the environmental temperature set points for heating and cooling are for each room. Know site details, including the:
- insulation;
- construction (concrete, wood, metal or a combination);
- number and size of windows and doors; and
- if the facility is built on an insulated concrete pad.
Make sure that any new or used HVAC equipment integrates with the existing (or proposed) duct system, as each variable impacts the best equipment choice.
Once the fundamentals are covered, decisions on whether waste heat from lighting will be exhausted independent of the HVAC or if the system will include an economizer or energy recovery ventilation (ERV) system.
18. Consider an ERV to reduce ongoing energy costs.
ERV systems are designed to recover cooling or heating energy exhaust airstreams and transfer them to the intake (outside) airstream. This saves energy, gives the cooling system a break and senses outdoor temperature and inside humidity.
ERV systems typically have a payback period between two and five years. They use either dry-bulb or wet-bulb economizers. A dry bulb only senses the temperature of the air, and is less expensive to install and maintain. The wet bulb senses both air temperature and moisture content, and can cut electrical costs by as much as 10 percent.
When choosing equipment, perform a total cost of ownership (TCO) analysis that includes energy consumption and life cycle costs to uncover the cheapest long-term purchase. When deciding between HVAC equipment, evaluate the initial equipment cost, energy efficiency, life span, maintenance and disposal.
19. Know how your lighting choice directly affects your energy bill, water and performance analysis.
Of the equipment indoor cultivators use, lighting has the greatest impact on energy consumption, and a delicate dance between cost and yield exists for each lighting option. A technology race is happening among manufacturers to deliver color spectrum range that supports each growth-cycle stage and consumes less energy. Since electricity consumption varies greatly by technology and impacts costs, an analysis is required to understand the cost of energy per gram of bud and per milliliter of processed oil.
Many cultivators utilize fluorescent and high-wattage lights including 600W high-pressure sodium (HPS), and 1000W high-intensity discharge (HID) lamp fixtures, all requiring a ballast to run. Others use LED, plasma and induction lighting (Note: Since this article explores ways to lower energy use and costs, including ancillaries, only relevant light technologies are being addressed. No light technology is being endorsed.)
Linear fluorescent lamp wattage ranges from 28W to 54W. Adding side and vertically suspended high-output (HO) compact fluorescent lamps (CFLs) adds 95W to 250W to total energy consumption. Fluorescent fixtures offer a lifespan between 20,000 and 35,000 hours. Classified as containing a hazardous material, proper disposal is required, which adds costs. While disposal costs can be nominal, it is still a factor that can vary with disposal frequency and equipment type.
Light emitting diode (LED) lighting doesn’t require a ballast and is talked about as a potential holy grail for reducing energy costs. LED is a non-hazardous, electrically charged semiconductor producing light spectrums in variable color temperatures. It emits little waste heat (HVAC doesn’t work as hard) and touts energy savings up to 40 percent. Based on lighting coverage area, most LED fixtures have 1:1 (equal) replacement ratio for 600W HPS and 1000W HID lamp fixtures. Upfront cost can be significantly higher than other lighting technologies, but the lifespan is, at a minimum, 50,000 hours.
Plasma lighting generally offers a 1:1.5 replacement ratio for HID lamp fixtures and is available in a variety of wattages that can offer projected energy-consumption savings up to 70 percent. Lamp life expectancy is approximately nine months (about 6,600 hours). Plasma lighting contains what is considered hazardous material, and like fluorescent fixtures, it requires specific disposal protocol.
Induction lighting is an electrodeless fluorescent lamp designed to replace 1000W metal halides and consumes 50-percent less energy, with a lamp life up to 100,000 hours. This technology also requires proper hazardous-material disposal.
The upfront cost of a lighting solution shouldn’t be the only factor you consider. Analysis of lighting products’ energy consumption, photometrics, maintenance, replacement frequency and hazardous disposal costs should be considered.
If you are changing lighting technology, remember that other critical adjustments will be needed. Lighting waste heat, or lack thereof, will impact the temperature, humidity and dew point of the environment. Also, pay attention to the schedule for nutrients, watering and other steps to compensate for environmental changes.
20. Water is an important part of the sustainability and cost discussion.
What can you do to save water as a cannabis grower? This is a good question with no easy answer; however, addressing the basics is important. With estimates of cannabis water consumption ranging from 1 gallon per plant per day, to 6 gallons per plant per day, having an efficient operation makes monetary sense to the large grower.
The best approaches (which depend on whether the grow is indoors, outdoors or in a greenhouse) include the use of established precision irrigation methods for soil, water-efficient hydroponic methods and rainwater harvesting delivery systems.
Also recommended is the use of reverse osmosis (R.O.) systems that will clean the water of harmful contaminants, is beneficial to establish a neutral pH level and can aid in water-recirculation systems, allowing greater reuse of water, especially in a hydroponic setup. These applications—combined with sub-metering for precise consumption numbers (to deduct sewer costs for a legal grow), tensiometers (soil moisture measurers) and automatic pH meters—can be tied back into a control system to remotely monitor in real-time the system’s status.
Obviously no single water-efficiency application will work for every operation. The best option is to consult with an expert that can point you in the right direction. There is a growing concern that cannabis cultivators are significantly impacting the drought in the western United States. By promoting water efficiency, you are not only protecting the environment, but being a good neighbor as well.
The Bottom Line
Numerous opportunities exist for cultivators to manage electric, natural gas and water consumption, and improve profits through strategic energy planning and procurement, real-time data, automation and controls, and advanced technology solutions. No one-size-fits-all solution exists—due in large part to geographical and regulatory differences—but many strategies and equipment solutions are available to successfully manage energy, lower costs, improve profits and reduce environmental impacts of cannabis cultivation.
Kathleen Hokanson ([email protected]) co-founded koan energy consultants in 2013 and serves as the company’s president. Wil Wicke ([email protected]), koan’s marketing and sales director, creates strategic energy plans optimizing energy products and services for legalized marijuana cultivators.