_fmt.png?auto=format%2Ccompress&fit=max&q=70&w=400)
Traditionalists say there’s nothing like a hands-on approach to cannabis production. Many growers are adamant that individual attention to each plant ensures the highest quality. But cultivators who want to take advantage of new market opportunities will likely need to embrace best practices often observed in industrial environments, such as automation, to scale their operations accordingly and increase efficiencies and profit margins.

Automated potting equipment can help growers boost productivity while still reaping the benefits of the hands-on care they have practiced on the smaller scale.
The path to automated potting can be a bit tricky to navigate for novices. “In the marijuana industry, there is a big bubble emerging,” explains Edwin Hoenderdos, CEO and principal consultant for Hove International Inc., a technology provider and consultant for the agriculture and horticulture industry. From his perspective, as new laws pass and cannabis operations expand, growers need to begin investing in new equipment and potting tools to differentiate themselves by cutting production time and costs. But that process requires a bit of learning.
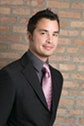
“Most of these growers come out of the basement with maybe 10 or 20 plants, and they never even thought about things like potting machines before,” he says. “They didn’t know they existed.”
The Potting Advantage
The fundamentals of potting machines are fairly simple. They are built to automate pot-filling operations in large-scale facilities and greenhouses. Basic units carry pots along a conveyor system and fill them with a custom mix of soil. Some units are equipped with a drill or dibbler to form a hole in the center of the soil where workers can then quickly drop in plants or seedlings, and the pots continue down the conveyor line.
Advanced systems take this a step further. They can be designed to deliver, fill and drill pots, and then automatically insert the plants and pack the soil to the desired consistency. They can even blow or sweep away excess soil and collect it for reuse.
The advantages of this system can be dramatic. In highly-automated systems, potting Highly-automated machines can process about 6,000 pots per hour, depending on the plant size. When moving from hand-filled operations, that can mean a tenfold productivity increase. And that means saving a lot of time and money for what would otherwise be a long and tedious process.

“It all comes down to the number of plants the grower does,” Hoenderdos explains. “If a grower has, say, 10,000 plants, they can fire up a machine on Tuesday morning and by midday on Tuesday, they have all their plants done for the week and the workers can do something else.” In a half-acre facility, potting machines can save an average of about two days of work per week per worker, Hoenderdos says.
Depending on size and options, potting machines can cost from $15,000 to $70,000. Options may include a pot de-stacker, pot take-off arms and conveyors, and remote online service assistance.
Hoenderdos says there is a minimum crop threshold he recommends before investment. “Greenhouse operation[s] ... really need at least a half an acre to justify these costs,” he says. “With half an acre, you have 16,000 square feet of growing space, roughly, so about 16,000 pots. That means, if you have a 10-week growing cycle, you have 1,600 pots to fill every week.”
At this rate, most growers can realize a payback for the machine in about four to five years, Hoenderdos says.
Getting Started
There are several factors growers need to consider prior to purchasing potting equipment. “Basically, there are different tools for every different application — focus is often only on the application, but also should encompass labor efficiency, quality and throughput,” explains Bill Bissell, senior process design specialist at AgriNomix Inc., a provider of automation solutions for the horticulture industry. Bissell recommends that growers consider the following factors:
- Throughput: “The first thing we ... ask is how many pots per hour do you need to fill?” he says. This helps narrow the product range. For example, an economy-scale machine can fill about 300 to 500 pots per hour, Bissell says. Meanwhile, AgriNomix’s highest-capacity fully automated machines can process pots less than 5.5-inch in diameter at speeds up to 8,000 an hour. These higher-end machines can cost around $45,000, he says.
- Soil: Different soil types will impact the type of machine required. This includes peat mixes, bark mixes, sandy soil or compost mixes. These considerations are important for finding the right conveyance for the potting equipment, Bissell says. “The more gritty or aggressive your soil is, the more it will wear and tear on machinery,” he explains. “For aggressive soil mixes, we would enlighten the customer of the ... benefits of the conveyor belt machines rather than chain and flight systems.”
- Machine options: Options can increase costs; to help growers understand which are necessary, AgriNomix lays out computer-assisted design mockups of an ideal potting system, including empty pot infeed, soil filling, dibbling, soil blow-off, clone trays, work stations and other “bells and whistles” a cultivator may need to pot plants efficiently.
Potting Systems: A Look Ahead
In the next few years, Bissell says potting systems, along with other types of automation, will become an essential part of a cultivator’s production toolbox. “As the industry continues to expand ... it’s going to become survival of the fittest, with low-cost producers taking the lead,” he says. “As you expand, you will need many types of automation to help improve the quality and survivability of your plants while keeping labor to the minimum. Tools like these are one way to do just that.”
Cannabis industry consultant Michael Mayes of Quantum 9 Inc., which provides construction and design services for growers, agrees that potting systems will become increasingly important as growers expand their operations. In fact, despite concerns by many growers, he says automation actually improves quality.
“We automate and systemize all processes to reduce human error,” Mayes says. “This ranges from irrigation to automatic potting devices to ensure the highest level of quality assurance. The less human interaction, the more accurate the process. This is not without constant quality checks to ensure the mechanized equipment is performing the tasks correctly.”