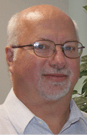
After a historic election night where eight of nine states passed new cannabis laws, cultivators and cannabis business owners across the country are eager to jump in to these new markets.
One thing that is often overlooked in that excitement and scramble is the importance of proper lab testing.
The American Association for Laboratory Accreditation (A2LA) is “the only independent, non-profit, internationally recognized accreditation body in the United States that offers a full range of comprehensive laboratory and laboratory-related accreditation services and training,” according to its website.
Cannabis Business Times’ Associate Editor Brian MacIver spoke with Roger Brauninger, A2LA’s Biosafety Program Manager, about the challenges with lab testing and why lab testing standards are so important in the cannabis industry.
Brian MacIver: What are some challenges with lab testing in general?
Roger Brauninger: In this industry, there is a lack of consistency in the competence of laboratories. In many cases, the underlying issue is a lack of experience in establishing a quality management system appropriate for quality control testing. We also encounter an absence of supporting infrastructure, such as fully validated analytical methods, relevant proficiency testing programs, and reference materials of relevant concentrations. … [With] no Federal involvement, each state is being forced to find a means to regulate ... cannabis on their own; something they may not have the necessary technical and financial resources to accomplish.
BM: What is A2LA proposing?
RB: In order to ensure there is confidence, competence and quality associated with the testing being performed, A2LA proposes that the cannabis industry adopt the world’s most commonly used laboratory competence standard, ISO/IEC 17025, as the baseline laboratory accreditation requirements for all of the testing laboratories involved in providing quality control and safety data for cannabis products on the market. We also propose that an assessment of each laboratory include the additional cannabis-specific program requirements detailed in the Americans for Safe Access (ASA) Patient Focused Certification (PFC) programs.
BM: Why is lab standardization important?
RB: In all other contexts within the realm of treatment of medically fragile patients, medicines are carefully manufactured (as required by the FDA) in such a way as to reduce contaminants and possible adulterants to the level of least possible risk of side effects. Attaining this level of least possible risk is always independently verified to ensure therapeutic efficacy and lack of harm, since the last thing one would want to do is to allow poisons such as pesticides, heavy metals and manufacturing solvents into cannabis products. Since the legal liability for producing a safe, unadulterated and contaminant-free product ultimately rests with the growers and processors, having a legally defensible and consistent approach to quality assurance should be of paramount importance to them as well.
BM: What impact would standardization have?
RB: Competent testing lends validity to an industry that has been the subject of much skepticism and controversy. Accreditation of this testing provides an additional layer of trust in the safety of these products and ... ISO/IEC 17025 is already a well-established mechanism that is used worldwide to provide confidence in testing for numerous and varied industries.
BM: What are some challenges with bringing lab testing standards to the cannabis industry?
RB: The lack of familiarity with ISO/IEC 17025 and a lack of understanding of its importance to the industry. Thus, one of A2LA’s current focuses in the industry is education: educating regulators about the need for ISO/IEC 17025-accredited testing; educating laboratories about how accreditation will ultimately benefit their operations; educating the overall industry on ... why there is a need for laboratory standardization. Using ISO/IEC 17025 as the foundation when first creating a cannabis testing laboratory will ensure smoother, quality operations than working backwards to establish quality procedures once the laboratory is up and running.