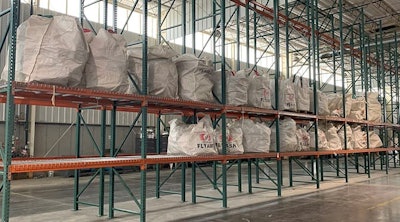
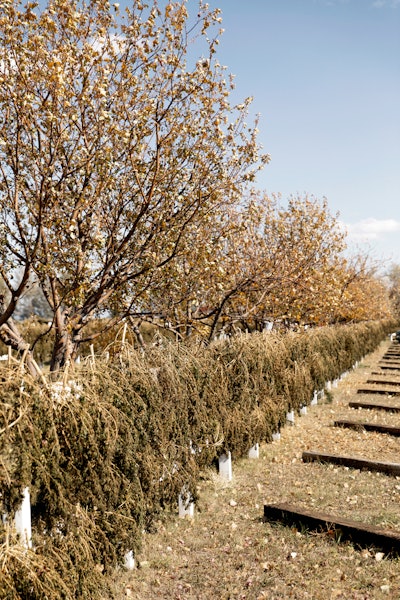
The industry’s understanding of best practices for hemp biomass storage is an ongoing learning process in these early years of licensed cultivation in the U.S., and much of what growers are falling back on comes from earlier generations’ grasp of the fundamentals or the Canadian industry. The Alberta Ministry of Agriculture and Forestry, for example, published an in-depth set of best management practices on hemp storage in late 2015, and it remains a helpful framework for how the industry approaches this matter.
And to a point, the state-legal cannabis industry (which many call the marijuana industry) in the U.S. has provided education on how to store this plant safely, as well.
Billy Chavis know this. He spent nearly 10 years in the legal cannabis space before joining Paragon Processing as lead engineer and partner. Earlier this year, the company secured a 250,000-square-foot former Columbia Records warehouse in Colorado City, Colo. (near Pueblo), and built it out with 170,000 square feet dedicated to climate-controlled storage space. The Paragon team asserts that this facility is the largest hemp processing facility in the country.
“Knowing that the [cannabis] market was heavily shifting and the price per pound of marijuana was decreasing, hemp seemed like a great opportunity,” he says of his career change. “So then I applied my skills to build larger-scale extraction equipment specifically designed for hemp. I’ve been doing that for around three to four years, and it’s led me into the position that we’re in with this company.”
And while Paragon will be storing its own hemp biomass for its processing ends, the company also accepts outside farmers’ crops for testing and storage as well. With clients’ precious product in mind, the Paragon team has developed a rigorous model for hemp biomass storage that can be used as a guide, no matter the size of your business, for examples of best practices.
Storage is key, Chavis says, because the newly legal hemp industry in the U.S. is engendering a great deal of excitement and, inevitably, overproduction. There’s a glut of raw material on the market. Prices are falling. Farmers need to know how to store their harvested and dried crops properly and line up buyers in need of biomass.
“Seventy percent of the biomass being grown this year so far does not have a predetermined buyer,” he says. When Hemp Grower spoke with Chavis in mid-October, he referenced a cold-warm spell that was moving through southern Colorado—a problem for hemp growers who still had plants in the ground.
Pre-Storage Considerations
This is an important starting point: Before hemp biomass is brought into a climate-controlled space for storage, growers must ensure that the crop is coming out of a suitable outdoor environment. Humidity levels vary by season and by geographic region. Southern Colorado, for example, clocks a dryer climate, generally, than much of Oregon. Each of those states has licensed more than 50,000 acres of industrial hemp, making Colorado and Oregon prime examples of what thriving hemp markets may look like for the foreseeable future in the U.S.
But that climatic difference is a big one. Oregon sees higher humidity and rainfall throughout the year compared to Colorado. In certain parts of the state, Oregon’s humidity levels hover closer to the 60% to 80% range with almost daily rainfall. That’s a significant obstacle for many Oregon farmers—one that those in Colorado and other states may not need to focus on nearly as much.
“That puts them into a position where they could [inadvertently] ruin their entire crop very quickly,” Chavis says. “So, even if they’re able to … get their crop down and dry it, storing it in a high-humidity environment will cause degradation of the plant material and essentially cause major losses, somewhere in the neighborhood of 20% to 100% loss.”
Paragon Processing works with farmers from those varying climates, and Chavis says his team focuses on that moisture content in each super sack (flexible fabric bags that can hold hundreds of pounds) of hemp that crosses his facility’s property line.
Before actually storing any hemp, Chavis advises farmers to quarantine each batch of biomass product and test random samples—just to be clear about what’s coming into the controlled storage space. He recommends three separate samples from each bag to ensure well-rounded data points. This 24- to 48-hour process may play out in quarantined trailers, somewhere away from the storage facility. In following this lead, growers avoid the possibility of contaminating hemp already being stored inside.
Farmers should know precisely what is going into any storage space. Beyond just the actual mass of the dried hemp product, it behooves them to test each batch and to prevent any microbials (mold spores), heavy metals or pesticides from ever entering the climate-controlled space. Whether growers are storing other businesses’ hemp biomass or only storing their own products, this is an important defense measure and an added layer of data to maintain a rigorous paper trail for federal or state compliance or to defend against potential litigation. Paragon also conducts random testing each month for longer-term storage needs.
Important Storage Variables
Once inside the storage facility, Chavis says that proper storage revolves around a few important variables. Chief among these climate considerations is a constant 10% moisture content for long-term storage. (Getting the humidity down a bit lower is even better.) If you’re storing your hemp for future cannabinoid extraction, starting off with a drier biomass product is going to help maintain the integrity of those chemical compounds; extraction of biomass with higher moisture content ends up costing up to 20% of the plant material’s cannabinoid content, Chavis says.
“Being able to dry [the hemp biomass] in a climate-controlled, low-humidity storage environment at the right percentages of moisture gives [growers] the longevity of being able to make the right decision for their company instead of having to rush into a decision that’s forced by a timeline,” Chavis says.
When it comes to temperature, growers encounter a classic Goldilocks scenario.
“Anything too hot is going to start to degrade your product,” Chavis says. “Anything too cold is going to put you in a position where the moisture content is going to start to have an effect of sweating when it turns out. Ideally, we keep our temperatures between 68 and 78 degrees Fahrenheit, which allows for perfect climate-controlled storage on top of that [10%] humidity level we’re trying to achieve.”
Because Chavis has spent much of his career in the legal cannabis space, he is well aware of the fundamental lesson in dried cannabis storage: The prevention of mold is of the utmost importance. Disregarding the nuances of climate controls or allowing products with varying moisture content to sit alongside one another in your facility will undoubtedly create conditions for mold growth and uncontrollable proliferation. This is a recipe for disaster, and it’s averted with ease by applying these tenets of storage to your facility—or by ensuring that your contracted storage supplier or processor is doing the same.
“If you don’t have an ideal storage environment, you can promote the growth of mold,” Chavis says. “And one little mold spore in a room can contaminate an entire storage or curing room—as you would call it on the cannabis side. If you were to do that, you could ruin hundreds of thousands, (if not) millions of dollars’ worth of product. Those lessons that you learn are very expensive, because they’re happening firsthand. So, one of the major, most important things that I learned was not to bring mold into a facility that can promote mold growth, to prevent mold at all costs and how to treat mold if there is an issue.”
And while Paragon’s 170,000 square feet of storage space is on the higher end of the spectrum in the legal U.S. hemp industry, Chavis says that scale isn’t a significant factor here. On one hand, larger facilities will simply provide more tasks—more data and product to monitor. But the fundamentals remain the same.
Over time, of course, cannabinoid content degrades naturally. Those cultivating and processing hemp for cannabidiol (CBD) can take pains to mitigate that degradation by monitoring climate controls. But, in an industry that relies almost entirely on cannabinoid content, this is an important statistic to track for all cultivators; any product that clocks a tetrahydrocannabinol (THC) reading above 0.3% should not be stored on-site, as it is already in violation of federal law. Chavis says one of Paragon’s first clients ran into this problem, and the team had to turn the product away.
Day-to-day monitoring is critical. His team is on the lookout continuously for drips in the ceiling or water lines. Any sign of standing water is an immediate red flag. Humidity levels are checked and double-checked throughout the day.
“These are valuable products that they’re sending over, especially in the neighborhood of the hundreds of thousands of pounds that each farmer is going to be bringing over here,” Chavis says. “So, to them, this is worth a lot of money. They want to know that it’s secure.”