
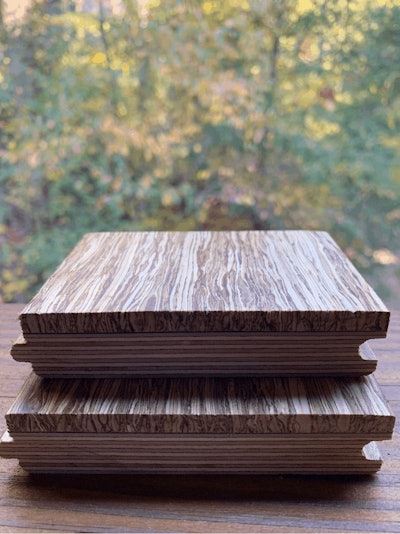
Entrepreneur Greg Wilson has more than a decade of experience in wood flooring, but his latest idea, flooring made from hemp, is a potential game changer.
“This is the eighth business I’ve started … with a similar idea and manufacturing process, which is taking fast-growing renewable plant fiber and using that to replace old-growth forest,” Wilson says. “I can say we have 10 times the amount of market interest as we’ve had for any of the other products, and some of those have gone on to become billion-dollar-a-year product lines.”
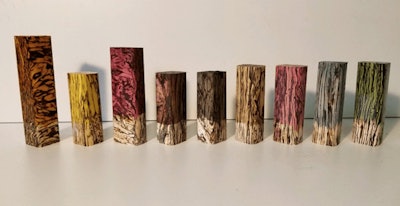
Wilson co-founded Fibonacci LLC in 2018 and has trademarked and patented HempWood, which is made from compressed hemp stalks and sealed with a soy-based adhesive. HempWood was developed to mimic the hardness, density and stability of oak, a popular building material. The Fibonacci team studied the process used to create popular bamboo flooring to develop a similar, but stronger, wood-like product from the hemp plant.
Fibonacci developed a relationship with Murray State University, purportedly the first in the country to participate in the national hemp pilot program established in 2014. In August 2019, Fibonacci opened its 16,500-square-foot facility in Murray, Ky., and started shipping its product in September.
Fibonacci has contracts with the university and other Kentucky growers for more than 2,000 tons of hemp stalks and plans to purchase 20% more in 2020, according to a company press release. All the hemp used in HempWood comes from within 100 miles of the facility.
The Kentucky Department of Agriculture estimates farmers in the state harvested 24,900 acres of hemp in 2019. Of that, 92% was for cannabidiol (CBD) and 4% for fiber. Wilson says he is one of the only, if not the sole, large-scale hemp fiber buyers in the state. He often buys it as a second or third product from farmers.
“We’re using not only hemp, a renewable product, [but we’re also] using the secondary or third product from our farmers because they’re getting flower and grain and fiber from the same plant,” Wilson says. “It really helps with the diversification away from what’s happening with the CBD right now. There’s a lot more on the market than is needed.”
Using wheat straw harvesting as a model, Wilson says farmers use their standard combine and set the header up about 6 feet to cut the top of the plant for flower and seed. A few days later, they go back through and cut the bottom of the plant in the opposite direction, which can pull back some of the knocked-down stalk.
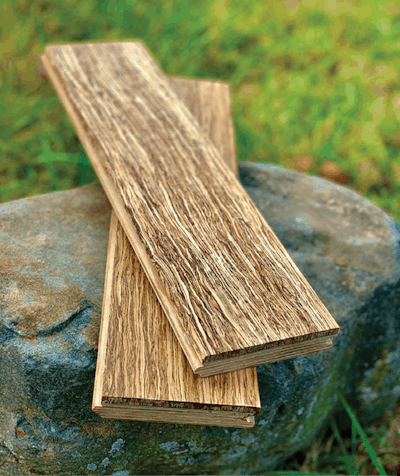
Wilson estimates the machines run over as much as 40% of the stalk on the first cropping. The harvesting process might need refining, but even so, the yields are still impressive. In about 120 days, Wilson estimates each acre of hemp can be a replacement for 15 to 30 solid oak trees that took 60 years to grow.
In addition to less growing time, Wilson says HempWood’s wood boards and blocks are designed to be 20% denser than oak.
HempWood is a face grade wood that can be cut, sanded and stained just like traditional oak and used for a range of products, including flooring, furniture and woodworking projects. Wilson says he also fields nearly daily requests for baseball bats, pickax handles, pool cues, guitars, ukuleles, drumsticks and a host of other ideas.
“The market is there. I get anywhere from 50 to 100 inquiries a day from people that aren’t just interested because it’s a new product but because it’s a new product and renewable,” Wilson says.
Fibonacci is currently shipping HempWood to end customers and downstream manufacturers, but it is looking to launch a retail program this year. The company’s plant has one processing line, but Wilson hopes to add a second shift this summer and get a second press for the 2020 harvest. Fibonacci has also started working with a West Coast university and is hoping to add a second plant in Oregon in 2021.