1. What past experience brought you into the cannabis industry?
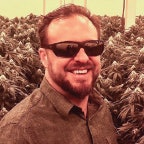
I grew up in the HVAC equipment sales industry. My family owns a large firm in upstate New York selling engineered application-specific equipment. We focused primarily on humidity- specific applications such as swimming pools, 100-percent outdoor air systems, clean rooms, surgical suites and processed critical manufacturing facilities. Many of the lessons I’ve learned from that work directly apply to cannabis.
2. What was the most difficult aspect of designing automated controls for cultivation?
Nighttime dehumidification. We did not expect the lights-off humidity load to be as great as it was in cannabis production, nor did we expect the cold and dry conditions that growers wanted to achieve late in their flower cycles. It’s more difficult to remove moisture from colder air because colder air has less ability to retain moisture. For example, it takes much more energy to remove a gallon of water from air that is 65 degrees Fahrenheit and 50-percent relative humidity than it does to remove a gallon of water from 80-degree air at 50-percent relative humidity—it takes two to three times more energy.
3. What is the most interesting lesson you’ve learned in this industry?
One of the most interesting things that we have learned is that in order for plants to transpire when lights are off in an indoor environment, you must introduce a fairly large amount of heat to assist in changing water from liquid to vapor. Our first systems were able to dehumidify and recover enough energy to put neutral air back into the room. This, however, was inadequate; we were not recovering 100 percent of the cooling coils’ heat energy to be used as reheat for the system. We went through multiple iterations of reheat coil design in order to finally capture 100 percent of the energy available in the system to be used for reheat.
4. How can growers plan ahead to ensure their automation is giving them the best benefits possible?

Anyone relying solely on thermostats and humidistats has no true idea of what is occurring in their space. Automation creates and monitors a stable environment, and is the only thing that can eliminate and identify specific variables in production. Every grower should have a complete direct digital control (DDC) system controlling and monitoring their grow rooms. Facility managers should be paying close attention to trend logs and examining all data from the DDC system. Growers should set up automated alerts for when their room exceeds acceptable deviations.
5. What can growers do if they experience an equipment issue after business hours?
We are very excited about our software system. This highly functional program will walk cultivators through a questionnaire and allow them to simulate their grow facility. By examining lighting, growing media, watering amounts, techniques, volumes and intervals, lights-on and lights-off temperature and humidity set-up points, we can accurately size their equipment, as well as make capital and operational expenditure comparisons for those variables. We have also recently acquired a service company to offer 24-hour support for all our projects via remote connectivity to all of our controls.