Cassie Neiden: Will you first tell us a bit about the DesignLights Consortium’s mission?
Damon Bosetti: Utilities are accountable to their rate payers and to their government regulators, oftentimes at the state level. These utilities need to show prudence for how they’re spending those efficiency program dollars. So, they could maintain in-house staff who can evaluate performance claims in efficacy, but to come up with a custom calculation for every single product that comes across their desks for efficiency incentives would be really time consuming and duplicative.
So what we do at the DesignLights Consortium is create these standards, called a Qualified Product List (QPL), which is a list of products that meet our minimum requirements. We’ve been doing that for many years with general illumination. Utilities can show that efficient products are being incentivized to the regulators and prove they’re spending their rate payers’ money wisely, all toward the policy goals of achieving more energy efficiency every single year.
People will always start to gravitate more toward new technology, but if we can accelerate that adoption curve by a few years, we’ll end up wasting less energy over that intervening transformation.
Neiden: Why did you decide to focus on horticultural lighting QPLs?
Bosetti: Controlled environment agriculture is one of the more rapidly growing load categories for many of our utility members. We started studying it in earnest about a year and a half ago. That process included multiple rounds of draft commentary and comments upon the drafts. We finished and published the specification on Oct. 1.
Neiden: Who did you seek out to gather those comments? And how did the comment process work?
Bosetti: Our spec-specific research list had over 400 email contacts on it. We have a very thorough stakeholder engagement process: We have a technical advisory committee; we have an industry advisory committee made up of large, medium and small manufacturers around the world; and we also have a horticultural working group of our utility members who are especially interested in horticultural topics. In addition, we did a lot of outreach and market research, trying to find manufacturers, academic researchers, etc.
One of the largest producers that we spoke with was AeroFarms, who we met at a Department of Energy horticultural lighting roundtable in Nashville earlier this year. They gave us some great information on how this extremely large, extremely high-volume lettuce production facility uses their LED light fixtures. We received very valuable commentary from two groups at Rensselaer Polytechnic Institute, the Lighting Resource Center (LRC) and Lighting Enabled Systems & Applications (LESA). There’s a multi- university consortium called GLASE (Greenhouse Lighting and Systems Engineering) that was extremely helpful and includes researchers from other universities, including Cornell and Rutgers.
Neiden: How does the incentive program work?
Bosetti: The DLC doesn’t set policies or incentives. The way utilities run their programs, how they decide to incentivize products or not, is completely up to them and their own regulatory and environmental landscape.
A utility chooses to refer to our list as part of their due diligence. They will have some kind of rebate form for incentives that the grower uses to report to the utility what their intention is. The utility would check the product code against our QPL website list. If the lighting fixtures meet the requirements, the utility would issue their approval and tell the grower to go ahead.
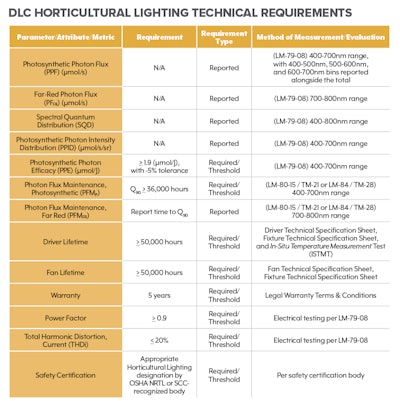
Neiden: As the DLC was developing this horticulture lighting QPL list, what was one of your big takeaways?
Bosetti: The first thing I would like to emphasize to people is that this is a minimum performance specification for a relatively new technology and application. And when you go back and look at other kinds of energy efficiency efforts, usually the first step you take with a new technology is not the most aggressive one. It is a baseline.
So, in that philosophy, we set our efficacy threshold that any qualified product must meet a 1.9 micromoles-per-joule efficacy requirement, which is about 12-percent more efficacious than a 1,000W high-pressure sodium fixture. That’s a big number. And it’s meant to be. And we’re not saying that 1.9 micromoles per joule is the best that an LED fixture can do; the sky’s the limit, and we’re eager to see how that changes in the years to come. But we think that is a reasonable thing to ask of an LED horticultural lighting fixture, and that will be a performance floor for any product to be in our QPL.
One of the common pieces of feedback we received was that efficacy is not the only thing of importance. Photon spectrum matters as well. For a given environment and crop, blue, red or green light may be more important. So in addition to the total photosynthetic photon flux output (all µmol/s, in the 400 to 700 nanometer (nm) range, abbreviated as PPF), we will be reporting the subcomponents too, in 100-nanometer-wide “bins.” Users will see the total PPF, along with specific “blue” (400 to 500nm), “green” (500 to 600nm), “red” (600 to 700nm), and “far red” (700 to 800nm) flux totals.
Also, these are not simply self-reported numbers by the manufacturers; these are going to all be reported through third-party-certified test labs.
Neiden: How will these standards be updated and adjusted, and when can we expect the manufacturer listing?
Bosetti: We are committing ourselves to a two-year major cycle, and then there’ll be a 12-month short minor cycle within it. The major cycle is going to be the next time the efficacy requirements change. The efficacy requirements will not change for 24 months, starting from Oct. 1. At month 18 of this major cycle, we’re going to go into our database of product performance and calculate the 15th percentile for efficacy. This will be that number in micromoles per joule for the fixture, that 15 percent of listed products are below, and 85 percent of listed products are above. We will notify the industry that this will be the new threshold value that goes into effect for new applications on Oct. 1, 2020. And, we will give an extra six-month grace period, to April 1, 2021, to any listed products that are below the threshold. This will give them 12 months to update or sell through their existing products before introducing new models, which is something we wanted to accommodate. Logistics constraints are real, and we want to give everyone ample notice and time to adjust.
The goal is to have the QPL populated with this first fixture listing sometime in mid-November and then work through the backlog of currently available products that will need to be qualified and listed.