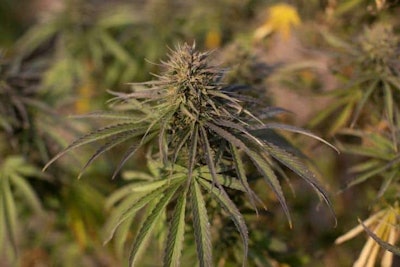
Editor’s Note: This is Part I of a two-part series on hemp harvesting. Part II, set to run in the July issue of Hemp Grower, will look at best practices for drying and storing hemp.
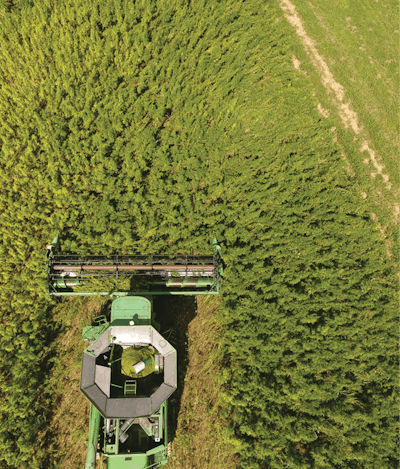
When Andy Fogle harvested his first hemp crop in 2018, it took almost a week to get the plants out of the 48-acre field and then dried, processed and into storage. While time-consuming, the process was essential to ensuring the quality of the cannabinoid-rich biomass—and profit.
“We had to make it as cost efficient as we could,” says Fogle, chief operating officer for Nature’s Highway CBD, based in Charlotte, N.C.
Growers in 34 states that reported data planted 70,530 acres of hemp for grain, fiber and cannabidiol (CBD) in 2020 but harvested less than 50% of their crops due to factors like non-compliance and crop failure, according to the nonprofit Vote Hemp. Even if hemp plants thrived in the field, poor harvesting, drying and storing practices could further reduce yields, potentially leaving growers with little to sell.
“It’s a big learning curve, and it’s important to learn how to do it well before scaling up,” Dr. Shelby Ellison, Ph.D., assistant professor at the University of Wisconsin-Madison, says of hemp harvest and post-harvest practices. “You want it to be a learning experience, not a losing experience.”
Here, growers and researchers lend their advice for this make-or-break step of the cultivation process.
Get the Timing Right
Timing is everything when it comes to harvesting hemp.
Dr. Bob Pearce, Ph.D., director of the College of Agriculture, Food and Environment hemp program at the University of Kentucky, notes that waiting too long to harvest hemp grain can cause seed shattering, leading to seed loss. (Editor's note: For more on seed shattering and other harvest terms, which are italicized throughout this story, see the "Hemp Harvesting Glossary" below.) Meanwhile, fiber left too long in the field degrades in quality, and a delayed harvest of hemp grown for CBD can cause the crop to go hot, ruining the entire harvest.
“Newer growers often have issues with what to look for” as they’re trying to determine when to harvest, Pearce says.
Although hemp takes between 100 and 120 days to mature, some varieties mature faster than others. Instead of relying on a set date to determine the ideal harvest time, Pearce suggests regularly walking in the fields or greenhouses to look for signs that it’s time to harvest.
When harvesting for cannabinoids, regularly check trichomes; a change in their color from white to a milkier, off-white color is a sign that it’s time to harvest. Those growing for CBD production should also test tetrahydrocannabinol (THC) levels on a regular basis. As CBD levels increase, so too do THC levels, putting these growers at higher risk for hot crops.
Meanwhile, growers should harvest hemp for grain as soon as the seeds begin to shatter. And hemp for fiber should be harvested after the plants bloom and before seeds set, says Pearce.
Monitoring the weather is also essential. It’s easier to harvest hemp before damp fall weather sets in because moisture increases the risk of mold or mildew spoiling the crop. Severe storms can also delay harvest, impacting the quality of the hemp grain or fiber, or causing the crop to go hot.
Balancing Labor with Mechanization
In addition to monitoring the fields for signs it’s time to harvest, growers must line up labor to get the hemp out of the fields and prepared for processing.
For Paul Sproule, who grew 1,100 acres of hemp for grain in 2019 and cut back to just 100 acres in 2021 on his North Dakota farm, Sproule Farms, harvesting is a one-man operation: Sproule climbs onto a combine, makes several passes across the hemp field, loads the harvest into a truck and heads back to the farm where it’s unloaded, dried and stored.
“One man, in one day, on one machine, can harvest 100 acres [of hemp growing for grain] with a combine,” Sproule says from experience.
At Nature’s Highway, Fogle is growing for biomass. His farm produced 800 pounds of flower per acre last season, but with prices dropping, he says margins are too slim to accommodate manual harvesting. Instead of hiring seasonal workers, Fogle uses a silage cutter with a stripper head to strip the flowers in the field. After harvest, he uses a tractor to till the remaining plants under in the field.
“Mechanical picking is great because I don’t have to bring in 20 workers for two to three weeks for hand-cutting and stacking in a barn; what we’re doing now is much more efficient. It takes two people: One to drive the silage cutter and one to drive the wagon it gets spit into ...,” Fogle explains. “The whole point is scalability.”
Harvesting is much more labor-intensive at East Fork Cultivars in Portland, Ore. Mason Walker, CEO of the craft hemp farm, hires up to seven seasonal staff to work alongside 12 salaried year-round employees for six weeks during the harvest period. It takes the entire team working together to harvest 9 acres of premium hemp flower.
“We’re primarily a hand-harvested farm, but we do have some mechanization,” Walker explains. “We do incorporate machines to help with the de-stemming and grading process, but the actual cutting plants out of the field is still done by hand. We don’t use a tractor, thresher or combine.”
East Fork Cultivars runs concurrent harvests: One team first harvests the largest flower-bearing branches that are hang-dried for premium flower, and a second team follows behind, harvesting the lower branches with smaller buds, stripping them in the field and preparing them to be kiln-dried.
Seasonal staff have a half-day orientation and continuous on-the-job training to make sure the hemp is harvested, dried and stored correctly.
“It requires constant training, but we’re fortunate that we have a larger year-round, salaried staff than most farms,” says Walker. “For harvest, we have mini teams … that are led by our year-round staff.”
Ellison believes labor is one of the biggest issues for those growing hemp for CBD and other cannabinoids, explaining, “Harvest is absolutely the pinch point. Getting the plants out of the field takes a lot of labor, and bucking the biomass takes a lot of labor … and growers are often relying on friends and family to get it done.”
While Walker admits the farm’s remote location in Southern Oregon makes hiring temporary labor a challenge, a strong company culture and above-average wages of $20 per hour—plus lots of advertising on social media and hanging flyers in local businesses—have allowed East Fork Cultivars to recruit a sufficient number of workers. Several seasonal hires return year after year to help with the harvest.
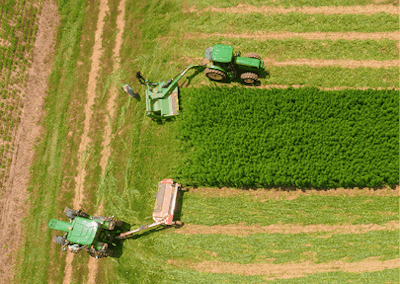
Determine Equipment Needs for Harvest
For Walker, who charges up to $600 a pound for premium flower at wholesale, hand-harvesting is worth the effort and expense because it preserves the pristine quality of the floral material better than machinery, he says. However, he still looks for opportunities to boost efficiencies. Golf carts shuttle bins of harvested hemp to climate-controlled facilities to be dried, and the harvest team uses a Munch Machine, made specifically for bucking hemp, on fresh plants in the field; it’s a huge upgrade from the jerry-rigged garden cart with metal strip plates that that staff used during their first hemp harvest in 2016.
Walker borrowed a Munch Machine and says it reduced the amount of labor he needed by 35%, so he purchased a similar machine the following season. He continues exploring mechanization possibilities that can still maintain the craft quality of East Fork’s hemp.
“One of the things I often [regret] looking back on our first few years of hemp cultivation is that we didn’t bring in enough traditional farming experience and [didn’t] force ourselves through the discomfort of mechanization,” Walker says. “In the connoisseur-grade cannabis world, there’s a common rejection of mechanization … that it strips some of the magic from the plant, and we listened to that voice for too long to our detriment.
“Machines are not going to replace people,” he adds. “Machines make it so we can remain cost-competitive and stay in business.”
Mechanization can be a challenge because the burgeoning industry lacks sufficient hemp-specific harvesting equipment, leaving many growers to rig up machines to help with the process. Thanks to the rapid growth of the hemp industry, Ellison notes that a growing number of companies have started developing machines that can help with harvest.
“There are a lot of machines that are reasonably affordable,” she says. “There are lots of different options, from semi-manual to more mechanized [including brush cutters, buckers, hand-strippers, stripper headers, sickle bar mowers and balers]. There is more equipment to help and the prices are coming down and, with some people getting out of the industry, you can get [used machines at better prices].”
Producers growing hemp for grain or fiber typically have the advantage of being able to utilize more traditional farming equipment. However, they might need to retrofit some of the parts to ensure the equipment functions in the field, according to Pearce.
“Growing for fiber, there are issues because the fiber can get wrapped around anything that spins, [like] shafts and bearings, and cause some real problems with the equipment. It’s the same with grain as it goes through the machine,” he says. “[Growers] may put a PVC sleeve over a spinning shaft to keep the material from binding up or [have] guards in place to keep hemp out of the bearings.”
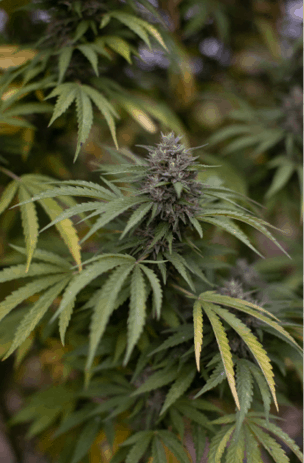
Marty Mahan, co-founder of Heartland Hemp Cooperative and a board member for the Hemp Chapter of the Indiana Farmers Union, uses conventional farming equipment like combines and hay rakes to harvest his 10 acres of hemp grain in Rushville, Ind.
During harvest, he uses a mower-conditioner to cut the crop and leaves it to ret in the field for up to a month to allow moisture to break down the fiber, which makes it more pliable. He turns the crop at least once during that process using a hay rake and leaves the hemp in the field until it’s fully dried.
The cost of a combine might be out of reach for most small-scale hemp farmers, but Mahan believes growers can attach inexpensive sickle bars or hay rakes to their tractors to boost efficiencies and reduce labor costs at harvest time.
Custom harvesting—or hiring a farmer with the right equipment to help with the harvest—is also an option. It’s common on farms growing cotton, corn, wheat and other row crops and could be a cost-effective solution for farmers growing hemp for grain and fiber. In fact, Mahan, who doesn’t own a baler, hired a local farmer to tackle the task. The farmer used his baling equipment to bale all of the hemp in Mahan’s field, and Mahan moved the 600-pound bales into his barn. “Custom baling is extremely common in the hay world,” he says.
Whether growers harvest their hemp by hand or mechanize the entire process, planning ahead and lining up the labor and equipment needed is essential—but it’s also just the first step of the harvesting process. To achieve maximum yields, growers should pay just as much attention to their post-harvesting processes too.