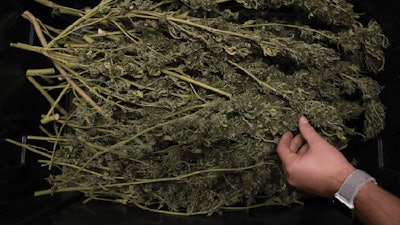
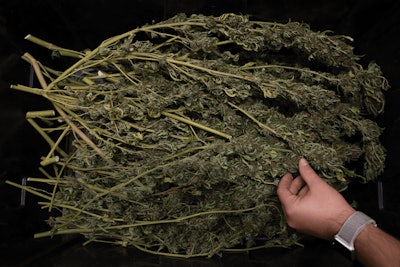
Editor's Note: This is Part II of a two-part series on hemp harvesting and postharvest processes. Part I, which ran in the June issue of Hemp Grower, focused on managing operations in the field. It also included a glossary of essential hemp harvesting terms.
From September to November each year, a team is dispatched to harvest the hemp growing in the fields of East Fork Cultivars’ 33-acre farm in Josephine County, Ore.
Hand-harvesting the hemp plants is just the first step in East Fork’s process. Once the premium flower is out of the fields, ensuring it’s properly dried and stored to preserve its appearance and potency is critical, according to Mason Walker, CEO of East Fork Cultivars.
The right postharvest handling and storage techniques help producers ensure their hemp—whether grown for fiber, grain or cannabinoids—is ready to hit the market while avoiding mistakes that can impact quality and profitability.
Drying It Right
The steps each grower takes during postharvest handling depend on the crop's purpose: Hemp fiber generally requires the least effort; grain needs more handling; and drying hemp flower grown for cannabinoids can range from simple to complex, depending on the crop's final market.
Fiber
Research published in the journal Biosystems Engineering showed that stripping leaves and heads from stems after harvest helped hemp fiber dry significantly faster than unstripped stems; turning harvested material in the field, especially if it was chopped, also accelerated the drying process. Growers can also use industrial hemp dryers to speed up the process. The goal is to reduce stalk moisture to less than 15% before baling, according to a report from the Alberta Ministry of Agriculture and Forestry (AF).
At his farm in Rushville, Ind., fifth-generation farmer Marty Mahan cuts the hemp stalks and lets them ret in the field, then bales the dried hemp and stores it in a barn on the farm.
“It’s baled into large round bales or large square bales, depending on your processing equipment,” says Mahan, who is also a member of the Indiana Farmers Union Board of Directors.
The AF report recommends using twine made from natural fibers because polypropylene twine (made from plastic) can contaminate the fiber; the report notes plastic netting may also work because it can be easily removed.
Grain
Hemp grain (seed) requires a higher level of postharvest handling than hemp fiber, according to Dr. Shelby Ellison, Ph.D., assistant professor at the University of Wisconsin-Madison.
“In the world of hemp, one of the best practices for grain production is to remove moisture,” she explains. “If you have moisture in your grain, that moisture will facilitate bacterial growth … [and] those bacteria will generate heat, and it’ll spoil the hemp.”
Immediately after harvest, growers must transport their hemp grain from the field to facilities that can blow air on the grain to reduce the moisture content and dry it quickly.
Paul Sproule grows 100 acres of grain—along with other crops like wheat and corn—on his North Dakota farm, Sproule Farms. Although he often leaves other crops in his truck overnight after harvesting, he says it would be a mistake to do the same with hemp grain. “If the seed is exposed to the elements, it’ll go rancid,” he says.
Sproule hauls truckloads of hemp grain from the field to where it’s dried and stored in grain bins.
The process requires gentle handling to keep the seeds from being damaged. To avoid damage to hempseed, machines should be set to lower speeds, according to the AF report. In the field, use slower combine unloading speeds, reduce auger speeds (or, like Sproule, forgo the auger altogether), and use a conveyor or belt trailer to unload the grain. In grain dryers, heat should not exceed 95°F, per the AF report; overheated hempseed will oxidize, reducing its quality and suitability for food products.
The seed bracts that hold the grain reach up to 19% moisture in the field and need to get dried down to 8% for storage, Sproule says.
“Sometimes, there’s enough moisture in [a hemp crop] that typical drying bins [used for other crops] won’t work as well because we can’t get enough air flowing through them,” says Dr. Bob Pearce, Ph.D., director of the College of Agriculture, Food and Environment hemp program at the University of Kentucky. “We may need to look at using smaller-batch drying systems and then transferring the grain into larger storage bins; that’s an area of open research.”
Sproule runs harvested grain through an air-jet sieve (a fan that blows air across the grain to remove dust and other bits of material clinging to the seed) and moves it into a bin where fans continue to lower the moisture content. He uses an app to monitor the moisture levels in the bin so he’ll know when to turn off the dryers. Depending on air temperature and humidity, he can reduce the moisture to the desired 8% within a period of a few hours to a few days.
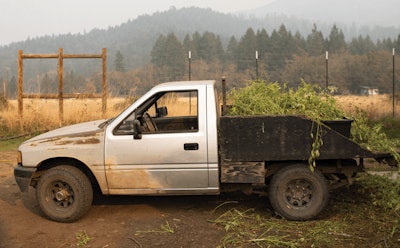
Flower
At East Fork Cultivars, Walker uses two different methods for drying hemp for CBD, depending on its final market. The hemp sold for premium flower, which fetches a wholesale price of up to $600 per pound, is hang dried on the stem in a climate-controlled building to preserve its look and quality. All the hemp flower sold as ingredients for use in products like beverages, topicals and tinctures is kiln dried.
“[Hang-drying] is a very laborious approach,” he admits. “The kiln-dried method is a more industrial approach … and [we use it] if the physical appearance of the flower and the flower structure doesn’t matter quite as much.”
Each climate-controlled building used to slow dry hemp has been insulated with spray foam and outfitted with commercial dehumidifiers. Walker also divided the buildings into zones, each with their own heating and cooling systems to maximize efficiency. “We’ve found that we can get the best quality by segmenting the buildings into smaller rooms for better climate control,” he says. “[The hemp] is dried for a full week and will remain on the stem for one to four months, allowing the chemical profile to settle and the moisture content to balance out.”
East Fork Cultivars tries to keep its slow-drying facility at 60% relative humidity, Walker says. Under these conditions, it takes a week to 10 days to fully dry the flower. The operation can also maintain a low temperature, which Walker says is important for maintaining terpenes and flower quality.
Postharvest, hemp contains up to 80% moisture, and drying helps preserve cannabinoids before extraction, per research published in the American Journal of Plant Sciences (AJPS). Kenneth Morrow, owner of cannabis R&D company and consultancy Trichome Technologies, says the optimal moisture content for cannabis and hemp flower is 8-12%.
Drying flower requires an optimal balance of humidity and temperature. Reducing moisture content to 15% can take anywhere from 11 to 36 hours when plants are hang dried at temperatures between 86°F and 122°F, per the AJPS. However, the research notes that drying hemp at temperatures above 37°C (98.6°F) could negatively impact cannabinoids and terpene levels.
The research also shows it takes fewer than five days to reach 11% moisture when material is stored in paper bags (versus hung) to dry in climate-controlled facilities where temperatures are 21°C (70°F) and relative humidity is 40%.
Andy Fogle, the chief operating officer of Nature’s Highway CBD, sells all of the hemp grown on the Neeses, S.C., farm as biomass and focuses on making the drying process as efficient as possible.
“The first year, we hang dried [our hemp]; it took a tremendous amount of square footage and it still didn’t dry that great,” Fogle admits. “We had 10 commercial dehumidifiers going, and the humidity levels would still be 90% in the mornings.”
Now, Fogle uses commercial belt-fed heating dryers to reduce moisture content, which he says are more effective and efficient than hang drying.
The Storage Sweet Spot
Proper storage ensures all the effort that went into drying hemp isn’t wasted. Just as the purpose for each hemp crop determines best practices for drying, hemp grown for fiber, grain and flower require different storage methods.
Fiber
As long as hemp fiber is dried before it’s baled and is stored out of the elements, Pearce notes that climate-controlled facilities or other special considerations aren’t needed. “After it’s retted, raked and baled, [hemp fiber] can be stored indoors indefinitely,” he explains.
Large bales stored outdoors have the potential to absorb rainfall, and the added moisture can lead to rotting. Similar to hay—which shouldn’t be stored outdoors under plastic because moisture can wick up from the ground and spoil the bales—the AF report also suggests that hemp fiber should be stored off the ground to keep the bales from absorbing moisture. (Hemp fiber is sometimes stored on wooden pallets.)
Mahan stores his round bales in a hay barn on his farm. “Definitely don’t leave them sitting on the edge of your field; that’s not an option," he says. "Proper storage is important.”
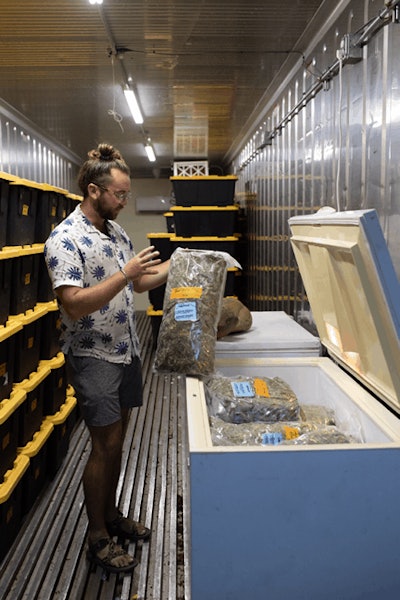
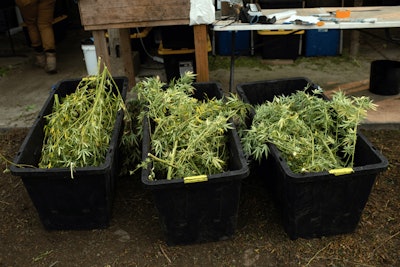
Grain
Hemp grain can be stored in metal bins with aeration and temperature control to keep it cool, says Ellison. (With poor temperature control, the condition of dried grain degrades.) The bins should also be sealed, which keeps critters from feasting on the freshly harvested grains, she adds.
Regular monitoring of stored grain is essential, according to the AF report. Some bins have automatic monitoring systems to detect hot spots, but wireless probes, which can be inserted into the grain via access points near the access doors, also work. If hot spots are detected, aerating and turning the grain in the bin can help with cooling, the report states.
On Sproule Farms, Sproule stores grain from a 100-acre field in silo-shaped bins; each can hold up to 7,500 bushels of grain. “The bins are sealed airtight, and the grain can be stored in there until it’s sold,” Sproule says.
Flower
Careful storage is also essential for hemp flower; exposure to light, heat and oxygen can degrade cannabinoids.
Little research exists on the best storage for hemp grown for CBD, other minor cannabinoids and terpenes, but data published about cannabis storage in the AJPS found that fresh biomass stored at temperatures between 33.8°F and 41°F for 30 weeks maintained its THC level. However, storing at higher temperatures led to decomposition of THC. Ellison believes the impact on CBD would be similar, so growers should prioritize proper storage.
At Nature’s Highway, Fogle stores biomass in 15-pound vacuum-sealed bags to protect it from light and air and preserve the cannabinoids. He notes that some growers also store biomass in 55-gallon drums (and Ellison has also seen growers use opaque bulk bags that hold hundreds of pounds of biomass).
Cardboard boxes also work and are the preferred storage method for Walker, he says.
After the hemp is dried, he uses a Twister Trimmer to grade flower, separating it into A flower, B flower and shake/trim. He then stores the product in food-grade plastic liners sealed with reusable zip ties, which he in turn stores in opaque cardboard boxes. The boxes are labeled with the cultivar and grade (as well as the required U.S. Department of Agriculture (USDA) and USDA organic certification labels) and stored in a climate-controlled building.
“We’re always careful about managing light, heat and oxygen through the whole process postharvest, and that’s how we maintain quality,” Walker explains. “We can store our hemp flower and it’ll look great and keep its color, [aroma], terpene profile and cannabinoids and potency, if we do it right, for two to three years.”
With the right processing and storage, East Fork Cultivars can slowly sell its crop throughout the year.
“It’s a common misconception: People think it has to be [sold] quickly or it won’t be fresh,” adds Walker. “It’s really not true; if you store it correctly … [hemp] can be shipped out to our customers one, five or 50 pounds at a time … for years.”