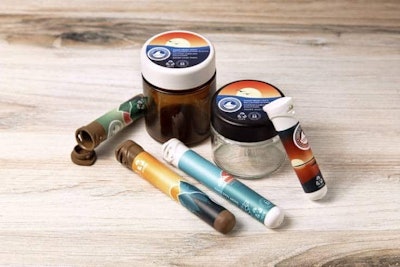
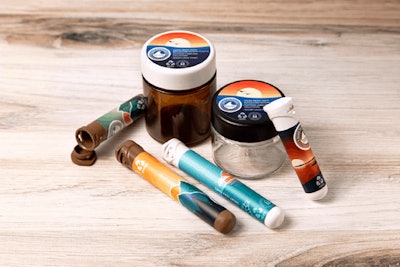
When James Eichner and Ron Basak-Smith met as graduate students at the University of Colorado, they bonded over music, a love for cannabis, and a frustration over the cannabis industry’s plastic waste problem. Shortly after they met, a joint business-school project on reducing waste led the duo to launch a business with the same goal.
And their initial mission to reduce plastic waste in the cannabis industry has resulted in a full-circle solution: packaging made, in part, from Cannabis sativa L. (specifically, hemp).
In 2018, Eichner and Basak-Smith founded Denver- and Los Angeles-based company Sana Packaging, which manufactures cannabis packaging out of hemp hurd, as well as ocean plastic waste. In just a few years, the founders have turned their class project into a business that now serves more than 350 customers throughout North America.
How It Started
“We originally came at this whole thing from a point of pure frustration as consumers,” Eichner says, adding that he and Basak-Smith knew they wanted to find more sustainable cannabis packaging options for their project. Many cannabis companies use traditional petroleum-based plastic for their varying product and packaging needs, including vape cartridges, pre-roll containers, boxes and bags for flower. And while some of it may be recyclable, much of it ends up as waste—recycling rates for plastic products hover at less than 10%, according to the U.S. Environmental Protection Agency.
So, Eichner and Basak-Smith began experimenting with plant-based plastics, which are both recyclable and biodegradable when sent to industrial composting facilities. And while composting facilities are still relatively rare across the country, plant-based plastics still offer sustainable benefits over the alternatives. They reduce the dependency on fossil fuels, which are limited, and instead use plants, which are a renewable resource and can pull carbon from the atmosphere.
Eichner and Basak-Smith first researched corn-based plastics but realized those have their fair share of problems. For instance, corn is traditionally cultivated using pesticides and monocropping or double-cropping systems, which limit the biodiversity of an area.
Eventually, the two stumbled across hemp—which is regarded as a more renewable and regenerative feedstock—as a plant-based alternative, and they worked with engineering students to develop hemp-based packaging. Their formulation still needed to include corn, as it is an easier and more common plant-based material to work with than hemp. Still, Eichner and Basak-Smith believe reducing the amount of corn in plant-based packaging is a significant improvement.
Others agreed, and the two won their class-wide pitch competition in 2017 with a 100% plant-based 3D-printed prototype made with hemp filament and bound together with corn polylactic acid (PLA) plastic. (Hunter Lovins, an environmentalist and co-founder of the Rocky Mountain Institute, was among the competition’s judges.) From there, Eichner and Basak-Smith received funding, mentorship and other resources from the Colorado-based CanopyBoulder accelerator program to found Sana Packaging. Their business was now up and running.
Difficult Material
Sana’s hemp plastic packaging is made of about 30% hemp hurd and 70% corn.
Improving that ratio has its challenges. For one, hemp hurd is difficult to work with. It’s rigid and opaque, allowing for limited uses. And with little history available on how hemp hurd interacts with injection molding equipment (which shapes plastic pellets into products), it’s been a balancing act of finding manufacturers who will take on the challenge and working with them to experiment with input proportions.
“Usually, you design a mold to work with the material. But because it’s an emerging market and people didn’t really know how to work with [hemp hurd], we had to do that while also designing material that would work with the mold,” Eichner says. “We were tweaking prototype molds and also tweaking formulation at the same time.”
Finding a steady supply of hemp has also been a challenge for Sana, Eichner says. The founders wanted Sana to be as sustainable as possible, so sourcing the hemp from U.S. growers was a must to avoid the environmental impacts of shipping it from other countries. But farmers growing hemp for fiber in the U.S. are still few and far between compared with cannabinoid producers, and infrastructure down the supply chain is even less developed.
However, Eichner says Sana has secured two suppliers in North Dakota and North Carolina who contract with farmers to grow the material. The suppliers compound the hemp into plastic pellets, and Sana makes its products by injecting the pellets into molds.
The company produces two different sizes of plastic tubes for pre-rolls and vape cartridges, and a plastic box for flower, concentrates, vape cartridges, and edibles.
Eichner says Sana has used a total of 57 tons of hemp plastic since its inception, equating to about 17.1 tons of hemp hurd.
“We by no means think it’s a perfect material, but we absolutely want to support the industrial hemp space,” he says.
The Long Haul
Sana Packaging also offers cannabis packaging made from reclaimed ocean plastic. The company now offers three hemp-based packaging products and five ocean plastic-based products, the latter of which have a slightly lower price point than the hemp products. As such, Eichner says a majority of Sana’s customers are opting for the ocean plastics: They account for about 60% of Sana’s sales, while the hemp-based plastic products make up the rest.
While the hemp-based packaging hasn’t necessarily been a profit driver, Eichner wants to continue working with it.
“We almost knew the hemp plastic products were kind of a loss leader in the sense that the plant-based future is something we’re still moving toward …. But it’s something we’re going to keep pushing,” he says.
Eichner adds that he’s looking forward to hemp-based plastic formulation improvements. “Right now, the stuff on the market is composites. The next big change will hopefully be material compounders starting to derive polymers from [the] hemp plant,” Eichner says. “That will make hemp-based bioplastics significantly easier to work with.”
The company is waiting for those advancements before it releases any new hemp-based packaging products, Eichner says. He acknowledges that could be years down the line, but he’s in it for the long haul.
“We think once there’s a better hemp bio-composite to [work] with, our other hemp products will become obsolete,” Eichner says, adding that hemp is “the most ideal feedstock for bioplastics, or one of the most ideal, especially from an agricultural perspective.”