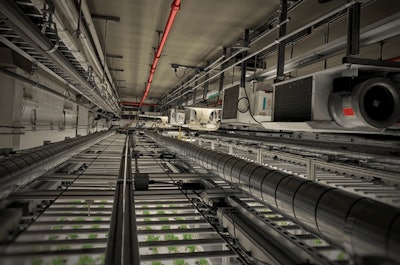
As a project engineer and manager, Luz Elena Parra’s most important role is examining architects’ and engineers’ layout drawings for cultivation and processing facilities and recommending how they can improve the layouts, budgets and more.
Parra, who owns Parra Projects Inc., works with cultivators, extractors and processors in Canada to ensure they build facilities that align with Health Canada requirements and are eventually approved. The stakes are high: The facility must be built before the license is approved, so it’s important to stay within federal regulations.
“Before, let’s say three years ago, you applied to Health Canada for the license, and once you got the license, you go and build. But what Health Canada found was that many people were applying, and not many people were building because it wasn’t easy to find the money,” she says. “Now we have to build, and once the facility is built, send video evidence capturing readiness, photos and other documents to Health Canada for revision and potential approval.”
Parra’s priorities must therefore align with Health Canada’s priorities: proper sanitation and security. But the process also begins with reviewing the bottom line.
Smart LayoutsCareful planning is critical to stay within a given budget and avoid costly mistakes. That’s why Parra first examines the design to make sure the flow makes sense and that potential contamination and security problems are mitigated.
“People create these beautiful layouts that probably will not be approved because the flow of the operation could create problems of cross-contamination,” Parra says.
Security can be strengthened with a thoughtful layout. Sometimes plans include outside access to final production rooms where cannabis is present, for example, which is not in line with Health Canada recommendations nor standards.
Also, plants should move from cultivation to drying, processing, packaging, storage and shipping in a logical sequence to avoid cross-contamination, and not back and forth through the cultivation area, for example. “When you go from one side of the building to the other side of the building, there is more potential for cross contamination, so the plant needs to be close to the next step,” she says.
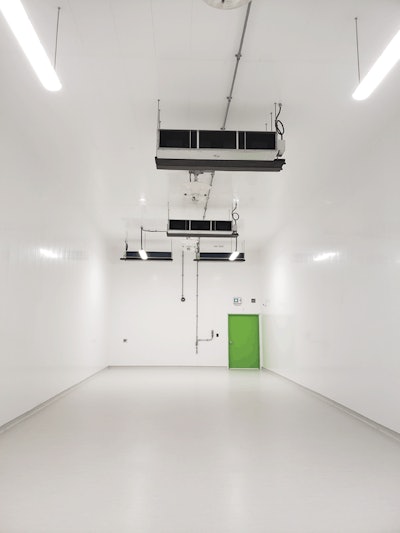
Functional, Not Fancy
One common oversight Parra sees in many designs is budgeting for materials that are overly expensive and unnecessary, she says.
“[Some] architects tend to build really fancy things, and we don’t really need fancy things. We need a functional, efficient facility,” Parra says. “One of the biggest is the HVAC system. I find two [problems]: a system that is not going to be what they need for cleanliness for good manufacturing practices (GMPs), or a system that is oversized that is going to cost a lot of money. [One project] had this system that was really crazy and really expensive, and through my research, I found Surna. I looked at the system, and found it was a more efficient system for half the price. I try to find things that are less expensive and more efficient.”
According to Parra, another common material people tend to overspend on is flooring, which Health Canada also examines very closely in the review process.
“The reality is the flooring doesn’t need to be fancy,” she says. “The flooring needs to be food grade, something used in hospitals and kitchens. [Often] they put in [a material] that is very expensive, that is not durable or that could potentially crack in the future.”
For indoor environments, Parra recommends a vinyl material that extends at least 4 inches up the wall to ensure a smooth, clean environment. In addition to saving money, these materials can prevent disease outbreaks.
“The hvac is my biggest concern when I see a design. You need to pick the right system and a system that has been proven in cannabis.” – Luz Elena Parra, Parra Projects Inc.
“[Many] cultivation areas are sealed concrete, and I am convinced that is not how you should do it,” Parra says. “Because the problem with sealed concrete is first it wears out fairly quickly, it can crack, especially [in Canada] with the huge changes in the weather here. Cracks are a huge problem for contamination. But if the concrete cracks and you have flooring on top, there is no issue for the plants. Health Canada pays attention to floors, and if we want to get the facility approved, flooring is big; flooring and walls are very important to get certified.”
Unexpected construction costs can also derail budgets. Although not always possible, when hiring a firm, Parra tries to find companies and teams nearby because it often makes the most financial sense.
“If I’m going to build a facility in a town, I want it to be mutually beneficial for the town, so we get the support. The other thing is it’s going to be cheaper for the cultivator if we don’t have to pay for transportation and other accommodations,” she says, adding that construction companies bill for truck and transportation costs.
_fmt.png?auto=format%2Ccompress&fit=max&q=70&w=400)
PRIORITY: HVAC
Materials and design are important for maintaining clean growing, extraction and processing rooms. But a proper HVAC system with the appropriate number of air exchanges for the space is one of the most crucial defenses and an aspect that is often overlooked.
“Cultivators know what temperature they need the room to be and the humidity, but they don’t pay much attention to the air exchanges you need per hour to avoid contamination,” Parra says.
Sometimes architects and engineers who are not experienced in designing for cannabis cultivation recommend HVAC systems meant for home, office or industrial use that are not aligned with the specialized requirements needed in plant production and processing. Another common aspect those without cannabis experience overlook is that separate HVAC systems are needed for each area to avoid cross-contamination. When Parra first reviews the plans, often only one HVAC system is planned for the whole facility.
“Sometimes plans only call for 10 air exchanges per hour, for example, when 30 or 60 are usually necessary,” Parra says. “Often, it’s difficult to find construction companies with this level of expertise. …
“The HVAC is my biggest concern when I see a design. You need to pick the right system and a system that has been proven in cannabis. [Otherwise,] the plants are going to get sick. Production is not going to be as efficient as it should be. People bring contamination on their hair and their skin, and the only way to clean this is with a good ventilation system. HVAC problems are very complicated to fix.”
Patience is also important in the planning and construction process. In a fast-moving, evolving industry full of difficult deadlines, this sometimes isn’t easy, but it’s essential.
“Stop, sit, let’s review, because in the end it’s going to be faster than if we just start building the facility, and in the middle of the project, find we need to stop, review, and redo,” Parra says she advises clients. “And it’s obviously more costly than doing it properly from the beginning.”
Navigate the Build Your Grow Special Report
Critical Considerations When Launching a Cultivation Facility