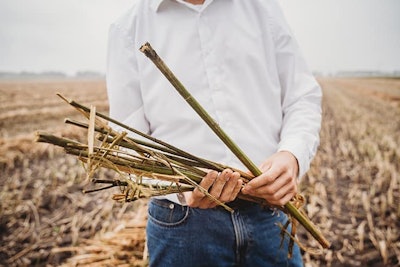
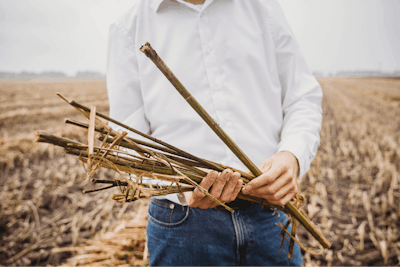
Capable of being used for everything from car parts and housing insulation to food and bedding for animals, hemp is renowned for its versatility.
HempFlax, based in Oude Pekela, Netherlands, knows this well. It utilizes just about every part of the plant to serve multiple industries.
The stalk? It makes up those animal beds and car and house parts.
The seeds and leaves? They are used for food and nutraceuticals.
The root? It’s left in the field to fertilize the next crop.
But it wasn’t easy to master wrangling sinewy hemp. “In the first years,” CEO Mark Reinders says, “if you looked at HempFlax, our courtyard looked more like a graveyard for burned-down agricultural machinery because hemp is one of the toughest crops in the world to harvest. The fiber is, I will say, the Kevlar fiber [of] the natural fibers. It’s so tough, so strong, even the strongest harvesting machine will break down [from] hemp if you do not modify it.”
Now, after more than 25 years in business, HempFlax has developed harvesting attachments for John Deere combines and breaker mills for decortication. The company contracts with growers in the Netherlands and Germany and grows its own hemp on nearly 1,500 acres in Romania. To allow for its consistent manufacturing of a varied line of products, the company handles harvesting and processing the hemp in all three countries.
HempFlax rose out of what cannabis breeder Ben Dronkers imagined when, in 1994, he founded the company about a decade after he launched the Hash Marihuana & Hemp Museum in Amsterdam with cannabis cultivator and book author Ed Rosenthal.
“In the museum, a lot of people told [Dronkers] … that hemp will never become an industrial crop [again],” Reinders says. “So, actually, he founded HempFlax to prove to those people that they were wrong. And now, 25 years later, I think he succeeded in proving his [point].”
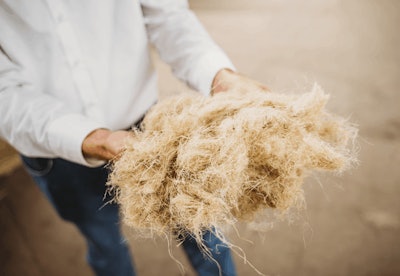
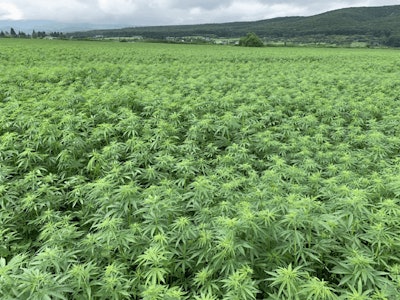
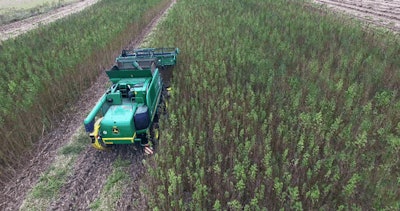
Sustainably Grown
As it works to help reestablish hemp as a major crop, HempFlax outlines a commitment to preserving the environment in its mission and vision.
“As a society, we need to move towards a more sustainable way of living without necessarily losing [out] on luxury and comfort,” Reinders says. “Hemp is bringing a sustainable alternative to the market with often better properties compared to the non-sustainable solutions.”
Reinders learned how to grow crops sustainably early on. His father, Jan Reinders, operates a roughly 85-acre farm in the Northern Netherlands, growing hemp, sugar beets and starch potatoes. The younger Reinders grew up working with his father on the farm.
“Farming is lovely,” Reinders says, reflecting on those formative years. “I like to drive on a tractor, but I don’t like to remove weeds by hand in the field. That’s why I liked hemp so much.” The family spaced hemp plants out so they would out-compete germinated weed seeds for sunlight and suppress the weeds. And the family still grows that way, planting 120 plants per square meter and avoiding unnecessary weed-control inputs in the process.
“We also experience that in the year after the hemp crop, we have less weeds in our other crops, so we have to apply less pesticides to protect those crops against weeds. I think the total sustainability of the farm increases a lot if you [use] hemp in your crop rotation,” says Reinders, whose father began growing hemp to replace wheat, which wasn’t as lucrative.
Following an internship at HempFlax in the early 2000s and working in the recycling industry and potato trade for a few years, Reinders joined HempFlax full-time in 2008 and became CEO in 2016. He has bachelor’s degrees in crop production and agricultural business and a master’s degree in management.
When he worked in recycling, Reinders says he saw many of the positives of the process. Recycling plays a role in solving environmental problems, he says, but growing and using hemp for various end uses can help prevent many of those problems from occurring in the first place.
The crop can sequester atmospheric carbon dioxide (CO2) that it only releases back into the atmosphere when it is burned or composted, according to a Guardian article penned by Mike Lawrence, Ph.D., director of the University of Bath’s Building Research Park in England.
End products created with hemp also have sustainable properties, such as hempcrete’s ability to absorb CO2, as noted by researchers from India’s Central Building Research Institute and the Entrepreneurship Development Institute of India.
Also, manufacturing hemp for one cubic meter (m3) of insulation material emits at least 15 times less CO2 than manufacturing foam glass for one m3 of insulation and at least seven times less CO2 than manufacturing expanded glass for one m3 of insulation, according to waermedaemmstoffe.com, a German informational website about insulation materials. HempFlax uses hemp to manufacture insulation for car parts, which Reinders says is more commonly done with glass fiber, adding, “… you’re not producing glass fiber, you’re making the car lighter, you have less energy use,” he says. “Those steps are plus, plus, plus, plus, plus on the sustainability level.”
This commitment to sustainability, along with a plan to expand market share, is reflected in HempFlax’s May 2020 launch of a building supplies division after it acquired German natural fiber insulation manufacturer Thermo Natur.
“Vertical integration is the most effective way of ensuring high standards are adhered to whilst also extracting maximum value from a synergistic supply chain,” HempFlax Chairman Guy Winterflood said in a press release announcing the launch of the building supplies division. “This is what we have achieved through this transaction, which is yet another avenue for HempFlax to capitalise on the fast-growing trends toward sustainability.”
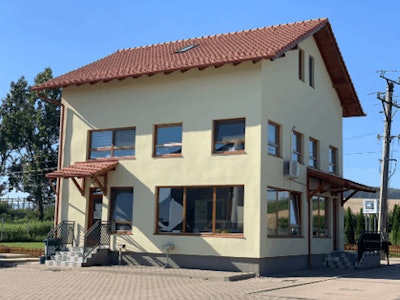
Precise Farming and Harvesting
Since he learned how to avoid pulling weeds out of the hemp field, Reinders and his team of 70 have established many more growing and harvesting procedures to ensure HempFlax’s success.
The business grows varieties registered for use in the European Union, where the tetrahydrocannabinol (THC) limit is 0.2%. HempFlax often uses Futura 75, a later-flowering, taller variety of hemp that can reach a height of 3 to 4 meters (9.8 to 13.1 feet) when fully grown; this variety grows taller in the Netherlands than in Romania, Reinders says, because of the longer days.
Due to HempFlax’s stake in so many industries and the high expectations of its business partners—ranging from product suppliers for Porsche and BMW to Dronkers-founded cannabis seed bank and hemp product retailer Sensi Seeds—diversification in growing is a must. The company has split its production for 2020 in roughly the following way: 1,236 acres contracted in the Netherlands, 2,224 acres contracted in Germany, and 1,483 acres at its farm in Romania. This is down from the roughly 8,600 acres that HempFlax, Europe’s largest independent hemp processor based on growing space, originally planned to farm in 2020. A lack of spring rain along with contracted farmers’ desire to grow other crops this year affected these plans.
HempFlax’s contract farmers in the coastal climates of the Netherlands and Germany grow primarily for fiber, leaves and “shives”—from the stalk’s woody core, or “shiv.” In addition to growing for all of this in Romania, the company also harvests seeds there. “In Romania, we have a more continental climate, and we are [at] a lower latitude where we can sow four weeks earlier compared to the Netherlands, and [hemp] flowers earlier compared to the Netherlands,” Reinders says.
Each climate has positive and negative aspects, Reinders says. For instance, Romania has worked better for producing seeds, but the region’s low rainfall and humidity compared to the northern regions results in less effective retting. The climate-diverse locales also help HempFlax avoid weather-related risks. “Climate risk these days is very severe,” Reinders says.
HempFlax has also spread its business risk—and improved its overall efficacy—by diversifying even beyond managing the cultivation and manufacturing of hemp. It also creates production solutions, including the attachments it has created for John Deere combines to harvest hemp stalks and leaves in one pass, Reinders says.
Using the combines, the stalks are cut to about 2 feet in length (at 15 centimeters above ground level) and left in the field for swathing, drying and retting. The business uses a turning process called “tedding” multiple times for an equal retting; rets until the stalks have a moisture level at or below 15%; and then swaths everything together.
Then, it's baled and transported to their facilities.
The roots, which stretch about 2 feet deep and spread out in all directions, improve the soil structure. So, HempFlax leaves them in the ground, Reinders says, though he adds, “If tomorrow a customer has a demand for roots, I’m pretty sure we will find a solution to harvest [them].”
Nothing Gone to Waste
At HempFlax, so named because the company used to use flax processing equipment, each part of hemp seems to have a purpose—and a specific means of manufacture.
The company’s nutraceutical offerings include hemp seeds and protein powder, and hempseed oil—created through cold-press processes, according to HempFlax product information—and cannabidiol (CBD) products that are extracted using CO2, Reinders says. The company white labels its nutraceuticals.
When processing and manufacturing fiber, HempFlax begins with decorticating the stalk using its in-house designed breaker mill system, Reinders says.
Following decortication, HempFlax uses the shiv for animal bedding and litter, and construction materials. The shives meet a large sieve that separates them into various-sized particles. Then, the packing department uses machines to bale the fiber into their end-use products.
HempFlax markets its animal care products as highly moisture-absorbing and non-clotting. They’re also “dust-free,” allowing animals respite from “allergic reactions and respiratory problems.”
The company also uses other parts of the hemp plant in animal products. “Hemp fibers are a good nesting material, which can act as replacement to the synthetic wool nesting materials ...,” Reinders says. “In the animal feed sector, hemp proteins, oils, and CBD can all be used in animal feed products.”
After decortication of the hemp, HempFlax takes the fiber to a refining line, where it is heckled to separate the plant fibers and cleaned multiple times. “We reach up to a fiber purity of about 98% ..., refined and cut to length,” Reinders says. “We can do 40-millimeter, 60-millimeter, 100-millimeter length.” This is used for multiple purposes, including insulation for homes and automobile door panels and dashboards.
True to whole-crop-model form, HempFlax uses a vacuum in both its Netherlands and Romania factories to filter air and dust. Another good sieving separates all of the vacuum-collected hemp particles into different grades. Some of the larger-grade particles are used for injection-molded pallets and layers of horticultural pots.
What remains—the smallest particles, which Reinders calls “fine dust” or “flour”—heads to another destination. “It’s being sold to a company that blends it with manure from chicken and horses,” he says. “They pelletize it, and it’s being sold as a growing medium for the rose-breeding industry.”
From using the stalk to the “flour,” HempFlax makes the most of what the hemp plant has to offer, growing its business across Europe and ensuring its place as a major force in the hemp marketplace.