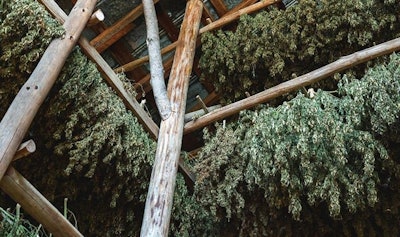
The Asheville Hemp Project team recently pulled more than 3,000 lbs. of hemp biomass out of their fields in the lush Blue Ridge Mountains. Situated among old tobacco barns, the hemp operation is uniquely suited for the demanding dry-and-cure process of the burgeoning hemp market.
Asheville Hemp Project’s products include CBD chewing gum and hemp pre-rolls, and Hoffman says this year’s crop includes the Oregon White CBG variety—an exciting addition for a marketplace eager to learn more about minor cannabinoids. Now that the plants are out of the ground, though, co-founder Leslie Hoffman and her team turn toward the barns and the important drying phase of their production.
She says it’s been a great growing season in Asheville, but the process doesn’t end at harvest. Drying and curing are integral parts of proper hemp cultivation. After she purchased the 23-acre property in 2015, its background in the rich North Carolina tobacco industry offered an enticing path into the future of an American hemp revival.
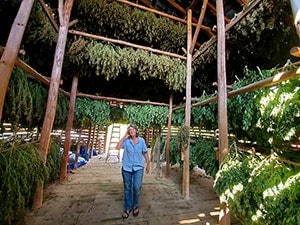
“The beauty of that remaining infrastructure from the Golden Age of tobacco is that we have these natural air flow drying barns that were originally built to drive Burley tobacco, which is a very tasty tobacco,” Hoffman says. “It's a slow dry and cure, which is very good for hemp. The barns are on high spots on the land, and they're raised up a little bit so that you get to the drying section of the barn by going up a little ramp. That enhances the convection currents of warm air rising.”
Here are three quick tips for hemp growers eager to get from harvest to processing this fall.
Enable Air Flow
This is the big one. Each of Asheville Hemp Project’s drying barns are slatted on the sides to bring in the outside air and allow it to move through the hanging hemp plants. The team supplements that natural air flow with large, slow-moving belt-driven fans. “It’s all about air flow,” Hoffman says.
The goal is to draw out the moisture of the plants and circulate dry air around them. This can be done naturally or in a tightly controlled environment (or both), but the movement of air is a critical variable that all growers must monitor.
RELATED: Asheville Hemp Project Is Sharpening Its Brand as Marketplace Continues to Expand
If you take the plants down while they still has too much moisture, mold is nearly guaranteed. “That’s a disaster, so you don’t do that,” Hoffman says, citing 12% moisture content as a good benchmark.
Think Ahead
“I think the biggest mistake that a lot of farmers make is not to be aware of how much space and how much time it takes to manage, handle, hang, dry, and then store all of this,” Hoffman says. “It's easy to put a lot of plants in the ground and then end up saying, ‘Oh my gosh, what am I doing?’ With several years under our belt, we've got a pretty good handle on what our capacity is, and we're sticking to that and working with other farms as we need more products.”
Inside Asheville Hemp Project’s drying barns, 80-year-old tobacco sticks running lengthwise across interior support beams (and just a bit longer than the beams themselves).
“We hang the whole plant [from those tobacco sticks] and provide plenty of air flow around each plant,” Hoffman says. “We probably get two full-sized plants on a tobacco stick. They're hung and then we space those sticks so that the plants have plenty of air flow.”
With different varieties coming off the field for different end products, the Asheville team makes sure to keep them separate inside the drying barns. From there, though, the process remains much the same.
“If you're really fussy about color—like if you want to end up with nice nugs that look like marijuana—then you will be a little more fussy about whether or not it sees any light, but basically controlling your humidity and temperature and airflow is the process,” Hoffman says.
Watch the Weather
This is common sense for anyone, especially with the year we’ve been having, but hemp growers eager to dry their crop properly must know the weather conditions outside their facilities.
“We aim for getting good drying weather, of course,” Hoffman says. “It certainly helps. And, really, what it ends up doing is affecting the amount of time and when we pull it down. We won't pull it down until it's dry and ready to be bucked down and bag.”
Take a stem and bend it a little bit, Hoffman suggests; you’ll want to feel a little bit of a snap. If it’s too moist, Hoffman says, it won’t snap in your hand and it should remain on the rack.
“If the weather isn’t cooperating, it takes a little bit longer,” Hoffman says.