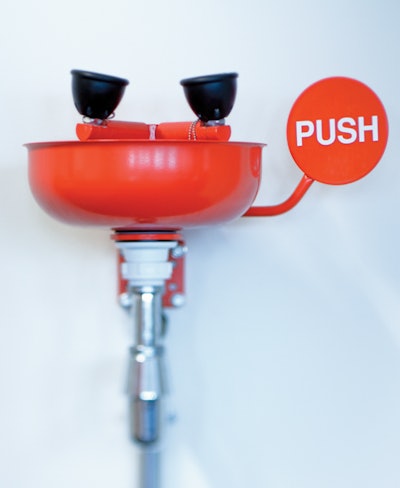
Providing your employees a safe and healthy workplace is not merely the right thing to do or a smart business practice; it is the law. The federal workplace safety standards of the Occupational Safety and Health (OSH) Act have been law since 1970, and, despite cannabis’s illegal status at the federal level, cannabis businesses are subject to workplace safety regulations just like every other private industry in the U.S.
Since Occupational Safety and Health Administration (OSHA) citations are public record and can be found on OSHA.gov, a cursory search of citations over the past several years shows that OSHA has been paying close attention to the cannabis industry. It is following the growth of the industry and issuing citations to dispensaries and grow operations. In reviewing 10 OSHA citations of cannabis dispensaries from 2016 and 2017, a clear pattern emerged: All citations were related to violations regarding hazard communication and employee exposure to hazardous materials. The following are the most common citations
- Lacking an adequate written hazard communication program for the workplace.
- No eyewash station or safety shower where employees may be exposed to corrosive or injurious materials.
- Respiratory protection violations.
OSHA compliance requires continual oversight, planning, review
Below are general guidelines every business owner should be following to avoid the common mistakes (and costly fines) made in these three areas.
The reality is that most of your employees are not going to follow all the rules all the time. Accidents happen, and mistakes get made.
Hazard Communication
The Hazard Communication citations were mostly due to either missing Safety Data Sheets (SDSs) or because employees had not been properly trained in the company’s hazard communication program. Any employee who may come in contact with any hazardous materials at the workplace must be given proper training to do their job safely and must have access to information about the hazardous materials in the form of SDSs.
Keep an inventory of all materials that come through your dispensary or facility. Make sure that you have a system in place to classify hazardous and non-hazardous materials. Ensure that:
- you are requesting and receiving the SDSs for all materials you receive from your supplier or distributor;
- all employees know where to access this information and have been trained and understand the information within the SDSs;
- all proper signage is in place; and
- all chemical containers are properly labeled.
OSHA’s Hazard Communication standard is in Subpart Z of the 1910 standard and can be searched under its standard number: 1910.1200.
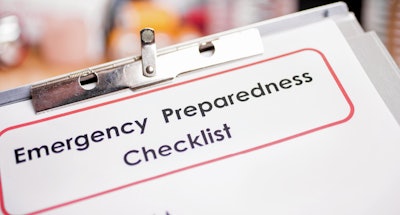
Eyewash Stations
Eyewash stations and/or safety showers are required in any facility where an employee may be exposed to an injurious or corrosive material. (OSHA’s requirements for first aid are brief and can be found under Subpart K of the 1910 standard (standard number: 1910.151).) Eyewash stations and safety showers can be easy to overlook, particularly when a new hazardous material introduced to the workplace may require an eyewash station that was not previously needed.
Many effective
Hazardous materials at a dispensary could include common cleaning supplies, such as isopropyl alcohol or bleach. The presence of anything classified as hazardous by the OSHA Hazard Communication Standard requires a written HazCom program. The best practice is to keep an SDS for every chemical in use or stored
It is the employer’s responsibility to provide a safe workplace, not the employee’s.
A safe workplace is the shared responsibility of everyone on the job, but because of the way the OSH Act is structured, in the eyes of OSHA, it is the employer’s responsibility to provide a safe workplace, not the employee’s. That means that the burden of proof lies with employers to demonstrate that they are taking the proper precautions, putting the safety policies and programs in place, and following OSHA regulations.
The reality is that most of your employees are not going to follow all the rules all the time. Accidents happen, and mistakes get made. A common defense against an OSHA citation is that the violation was a result of employee error. But to prove that, employers must provide evidence to show that they did their due diligence, provided the proper training to the employees, did everything in their power to prevent that unsafe condition, and was unaware of employee misconduct at the time of the incident.
That is why regular, documented safety training is so important. In addition to giving your employees the knowledge to work safely (which cuts down on incidents and workplace injuries), it gives you, the employer, an invaluable, ongoing affirmative defense. The more documentation you have, the better off you are. Records of employee safety training show that you are actively engaged in keeping your employees safe and doing everything you can to give them the knowledge they need to do their jobs safely.
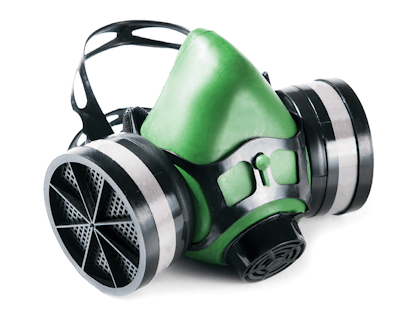
Respiratory Protection
Respiratory protection requires meticulous planning and attention to detail. This is especially important for vertically integrated operations that operate cultivation facilities. What hazardous vapors, gases or particles are your employees being exposed to? Is there adequate ventilation in the work area to mitigate the respiratory hazards? Can fans or a negative pressure ventilation system control the respiratory hazard? If you are unable to determine the severity of the respiratory hazard, an industrial hygienist may need to be brought in for testing.
Keep in mind that having your employees work
Prior to using a respirator, OSHA requires two things: a medical evaluation and a fit test. All affected employees must be evaluated by a medical professional to determine that they are medically able to work
Fit testing must be performed annually or any time a new tight-fitting respirator model is used. The employer must pay for both the
Remember, fit testing is even required when using a “dust-mask” type of protection also. So long as it is rated as a respirator and designed to protect against hazardous vapors,