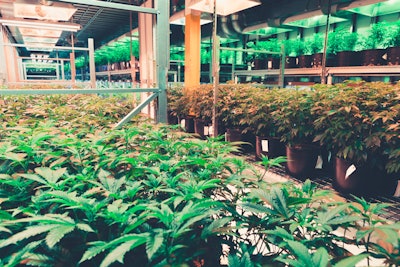
As a consultant, sometimes you take on “interesting” projects. In this case, I visited a commercial cannabis grow facility that also served as a demonstration site for a garden lighting manufacturer. I was there as part of a job interview with the light manufacturer to see their lights in action. Along the way, I pointed out a few issues I saw with the grow. Eventually, I asked if we should begin with a short consulting engagement to “green up” the grow before I came to work for them. Unfortunately, they said yes.
After my initial visit, I thought I had a handle on the problems that needed to be overcome. By commercial standards, the facility was fairly small (about 3,600 plants), so it should have been fairly easy to get in shape, right? The plants were watered and fertigated by hand and grown in fabric pots using a hand-mixed, soilless grow media. The two head growers were let go.
The grow spaces were very dirty—soil on every surface and dead leaves everywhere. Every plant was nutritionally locked out; there were purple stems and yellow leaves as far as the eye could see.
I honestly thought I would green up the place, reduce labor, simplify nutrition, train my replacement and move on in 12 weeks. What could go wrong?
What I Didn’t Know
Walking in the door I was confident. I knew exactly what needed to be done. Or did I?
System Upgrades and Facility Redesign. It turns out many changes, which I knew nothing about, were planned to begin within weeks. Decisions had to be made immediately regarding facility layout, growing systems and media, and watering and fertigating methods, as new systems were being designed and built. Construction was planned to add hallways and reconfigure the grow rooms into similar sizes.
Double racks, both stationary and mobile, were being installed as the rooms were converted. A programmable logic controller (PLC)-based control system was being installed to water and feed the garden, control HVAC, manage CO2 and eventually support a sensor network. And if that’s not enough, the plant count was also increasing to 6,000. Trying to plan all these changes while also working to fix the grow in 20 hours a week (the agreed-upon amount of time I would spend there) was simply not possible.
Pest Problems. The garden had many pest problems including spider mites and root aphids, both widespread. The previous growers’ assault included spraying every three days for mites and drenching every five to seven days for root aphids. This heavy pest control regimen was leading to phytotoxic loads on the plants. In other words, the accumulated concentration of pesticides was becoming toxic to the plants.
Environmental Challenges. The entire facility had environmental issues. For example, the largest grow room’s air conditioner was dying and needed to be repaired several times during my stay. This led to the manual on and off cycling of banks of grow lights all day to give the plants some light, but not raise the garden temperatures (even though reduced light inevitably leads to reduced harvests). Every grow room suffered from a lack of air movement, as most of the wall-mounted recirculating fans were old and needed to be replaced as well.
Organizational Issues. I had not even considered possible organizational problems. In this case, the person ultimately in charge of the facility was an owner, who had worked for decades as a general contractor, but had no cultivation experience. His leadership skills weren’t best-suited to lead a team that nurtures a large number of living organisms—24 hours a day and 365 days a year—especially when the organisms largely call the shots. The only person in ownership with grow experience was working in a sales and business development capacity.
Steps in the Right Direction
We started by flushing the plants. In addition to the heavy pest management regimen, the previous head growers were chasing every nutrient deficiency they could think of and “throwing everything at it,” hoping something might work. This led to extremely high levels of nutrients bound up in the grow media, which locked out the plants (reduced their ability to uptake nutrients). Flushing helped—the nutrient concentration (PPMs) of the run-off solution lowered and the plants visually looked better.
Next, the facility was cleaned from top to bottom. There was soil everywhere—on the fans, lights, conduits, floors. Just about all the old, unused nutrients and growing media were thrown out.
Then we switched from hand-mixed loose grow media to rockwool, starting with new transplants. This change reduced the mess from mixing loose media and significantly reduced transplanting labor—from three people working two days each (six total days) to two people working four hours each (one day).
Predator mites were released to combat the spider mites while reducing pesticide exposure. Initially P. persimilis were released as they are very aggressive, followed by N. californicus, who hang out longer and sustain on less prey.
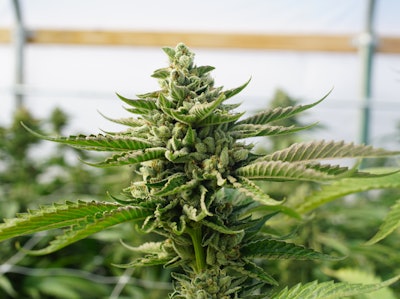
Trouble in Paradise
Everyone started saying, “the grow looks so much better.” And then trouble began.
The owner in charge left to attend a conference for most of a week, then a personal matter took him away for another week soon thereafter. During this period, the employees stopped listening to me and began doing whatever they wanted—usually over-watering and excessively removing fan leaves from the plants. The staff knew that labor cuts were coming, with transplanting already streamlined and watering and fertigation automation being planned. The grow became a free-for-all with everyone scavenging for work. The mood turned gloomy.
And mistakes were being made. One of the worst occurred when the junior head grower decided to “correct” a perceived calcium deficiency in one of the rooms. He sprayed 450 plants with an untested concentration of CalMag (a calcium magnesium supplement) and humic acids.
We had talked just a few days before about how to properly test new sprays: Treat a small number of test plants, spray another group with just the water in the mix to rule out its contribution, then wait a day or two to see the results. This is basic “good gardening practice” to protect against the possibility that the new spray might damage the grow. I’ve got plenty of stories about growers who didn’t test properly, received negative results and lost their jobs.
The entire garden took a major change for the worse. With too many people calling the shots, some plants were underfed, others overfed. The root aphids came back with a vengeance, and the environmental problems were unabated.
This was when the owner stopped listening. Suddenly I was responsible for everything—inventory, product procurement, training, SOP creation, automation and process planning, design review, verifying what each employee was doing and how they were doing it—all in 20 hours a week.
While growers who accept full-time positions might get a salary instead of a set number of hours, the expectations and operational responsibilities can be the same.
Lessons Learned
This experience has taught me many new lessons and reminded me of others I had forgotten. Here are some of those lessons. Hopefully you’ll learn from them, so you don’t have to make the same mistakes.
Growing Facility Operation and Design
- Remove old or unused nutrients from the grow. If you can’t bring yourself to get rid of them, store old/unused nutrients off site or locked up to remove the temptation for someone to do something stupid. No one is there all the time to keep an eye on everything.
- Growing vertically can challenge employees physically, if you’re not prepared. The bottom levels of vertical grow systems are lower than typical benches, which means your employees need seats or kneelers to protect their backs. Unless your growers have super long arms or a powered lift, expect them to spend a lot of time climbing up and down ladders to tend to the upper level(s).
- Floor drains are you best friends. This grow facility had one working drain for the entire grow when I arrived. Countless hours were spent pumping out reservoirs and vacuuming spills. I had forgotten how easy it is to squeegee spills into a drain instead of having to vacuum and pour them down a drain.
Organizational Matters
- As you start automating, employees will scramble to find work. As there becomes less to do, they fear losing their jobs and will start making up work to look busy. At this grow facility, the employees started feeding the plants too frequently: Plants in grow areas that were being hand-watered were getting fed every other day, like clockwork, instead of based on the plants’ actual needs.
- Understand the commitment of a “demo grow.” In a demonstration grow, visitors will take up some time with tours and questions. Since this grow facility was a manufacturer’s “showcase,” the owners let the look sometimes outweigh what was best for the grow. Bad-looking plants may be sequestered or harvested weeks early to keep them out of customers’ view.
- If you’re going to be the head grower, expect a 50-plus hour work week and to oversee the staff in addition to training or replacing them.
Consulting Projects
- Either be the consultant or the head grower, but not both. I tried to be both; it didn’t work. As a consultant, be there to fill in the information gaps and offer advice. This role can be accomplished part-time.
- If you’re the consultant, run the project as a real consulting job. It is important to document shared expectations in a written Scope of Work (SOW), then hold weekly and/or monthly progress reviews. It’s far too easy to get caught up in the day-to-day craziness of a commercial cannabis grow and skip this crucial step. Prepare weekly reports that document the week’s work and set the next week’s expectations, and the project sponsor should read and react to them to confirm or update work accomplished and planned. These weekly reports are working documents, not merely a record of what has been done.
- Investigate the ownership team/consultant prior to accepting the project. Ask the owners or consultant about their background and check the internet. Do they have the experience and backing to succeed? How do you complement each other’s skill sets? Also, know this: Just because you’re good friends with the owner/manager outside the grow does not automatically mean either of you is a good fit in the grow.
- Get the full picture before starting. Past problems are as important, if not more so, than current operating issues. Interview long-term employees in addition to management for information about the grow’s status and any issues to anticipate.
- Only work the hours you’re getting paid for, and ensure you get paid. The concept of “work a bit more today and a bit less later” never comes true. In this case, I ended up working 30-plus hours a week, so this client got 50-percent free labor out of me. Also, bill the client weekly. It is not uncommon, at a consulting project’s end, for the client to refuse, get too busy, “misplace” or otherwise find a reason not to pay your final invoice. Weekly billing limits a client’s ability to dodge paying for your work.
- When the project is over, conduct a clear-eyed postmortem. Important lessons can be learned on both sides of the table by soberly revisiting the project. Compare expected vs. actual outcomes and examine what contributed to any gaps. Note successes and the actions that led to them and be honest about things you or your company might have said or done—or not done—that did not help. Jot down things to do again and to change. Most often, postmortems reveal gaps in expectations between the consultant and client, which is a good reason for a solid SOW and weekly project updates.
Clients should be particularly careful not to simply “blame it all on the consultant,” an easy way out that will stifle much-needed discussion of lessons learned and possible improvements. Clients who fail with consultants more than once at the same facility, or who frequently turn over head growers, should be particularly open to problems arising from within their organization that may have impaired or prevented the consulting project’s success.