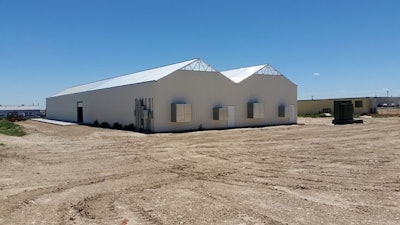
Expanding your business is a daunting task for any cannabis cultivator, but it can be especially challenging if you’re transitioning or expanding your business into a greenhouse for the first time. There are so many pitfalls to avoid and questions to ask that it can be hard finding a good starting point. Nexus Controlled Environment Agriculture Engineer and Northern California Sales Manager Paul Golden answers the most frequently asked questions about transitioning from an indoor grow to a greenhouse operation.
Q: What are the biggest mistakes to avoid when transitioning from an indoor facility to a greenhouse?
Paul Golden: Often growers who are transitioning to greenhouses will bring the equipment they use in warehouse grows to greenhouses. Working with a qualified greenhouse manufacturer reduces costly mistakes, such as lighting with fixtures not designed for the greenhouse environment or lighting with bulky reflectors, which block the natural light.
Another common mistake is using growing techniques that originated with basement growers and were adopted in warehouses. These practices, such as aeroponics and vertical growing, may not contribute to solid automation or efficient workflow, which are important goals in larger greenhouse grow operations.
Q: What is the optimal supplemental lighting setup for a greenhouse?
PG: We recommend one light for every 50 square feet.
Depending upon the situation, that can range from one light for every 36 square feet to one light for every 72 square feet. If you’re in an area that has a lot of natural light, you could move to the less concentrated end of that scale, around 72 square feet. If you’re in an area around the northeast where it’s more overcast and there’s less sun, you might want to go on the higher concentrated end around 36 square feet. The important thing to remember about supplemental lighting in a greenhouse is that it just that … supplemental. Let the light in and use what nature gives you for free.
Q: How is HVAC different between an indoor facility and a greenhouse?
PG: An indoor facility is going to be heavily reliant upon an HVAC [system] to cool the room due to the need to use grow lights. Without a way to exchange the air, the HVAC system needs to operate to regulate humidity and temperature. This approach increases the daily operational expense when compared to greenhouse cooling. In a greenhouse, we’re using evaporative cooling, and most greenhouse growers are not using HVAC. If they do, it’s because they are willing to absorb the cost or they might do it in a small supplemental way.
In select areas where high heat and high humidity coincide at the same time of day, some growers choose to use HVAC as a secondary climate control system, especially during the blackout hours of the night, the same way somebody in their house uses an HVAC and doesn’t run it all summer long, yet only runs it when the heat and humidity are at unacceptable levels.
Q: How can I maximize my use of the sun?
PG: The first thing you need to do is understand the climate conditions in your area. That is crucial. In each area of the country, you’re going to have specific sun-related issues to manage. In the West, you’re going to have a lot of sun, you may have some extreme heat in the deserts of California and Arizona, or other parts of the Southwest. As such, you’re going to need a strategy for how you can get your greenhouse cool to the range of 72 to 80 degrees.
The advancements in greenhouse coverings in the past decade have led to a prevailing choice for growers today. Diffused polycarbonate coverings allow for high PAR light transmission and filter unusable light, such as infrared, which only contributes to heating the greenhouse. Diffused polycarbonate coverings help keep the greenhouses in the proper temperature range while eliminating shadows and light stress to the crop, all of which increases plant productivity. These coverings spread the light to all areas of the plant canopy with minimizing shadows.
Q: What materials should I use to build my greenhouse?
PG: Primarily, for cannabis, we use diffused polycarbonate on the roof. It’s lighter, it’s less expensive, and it minimizes shadows. It works really well in that even if there’s less light, the diffused material spreads the light throughout the greenhouse. Every few years, advancements are made to increase the light transmission of polycarbonate coverings that make them more practical for low-light climates. The diffused nature of the light entering the greenhouses also helps mitigate the impacts of non-transparent or metal walls commonly seen with light-dep greenhouses. You’re giving up some light with those metal sidewalls, but the diffused polycarbonate roof will eliminate shadowing from the walls, curtains, trusses and other equipment that would normally block light to the canopy. Bright white sidewalls common with light-dep greenhouses also help reflect supplemental light back into the greenhouse as opposed to clear walls which allow this light to escape.
Q: What efficiencies should I focus on maximizing in my greenhouse?
PG: The two best ways to be efficient are to reduce your energy costs and to increase your production through benches. We recommend rolling benches since they are going to have more efficiency than stationary benches at a lower cost than palletized benches. By eliminating aisles, growers have more efficient use of their supplemental lighting and increase the amount of canopy that will fit in a zone.
Q: How can operating in a greenhouse impact overall cost of production?
PG: We anticipate the utility costs of being in a greenhouse to be about 25-33% of what a warehouse would be. If you’re spending $40 per square foot in an indoor, it’s going to be about $10-13 per square foot in a greenhouse. Going back to pricing, that’s a huge efficiency gain.
For more information on the differences between greenhouse and indoor growing, you can refer to the informational video below or find a Nexus Greenhouse representative to contact here.