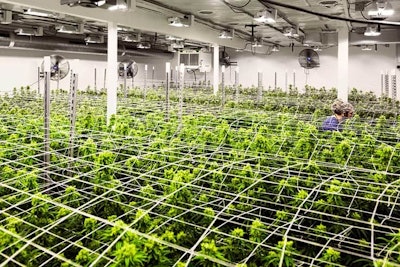
Editor’s Note: This article has been adapted from Chapter 05: Navigating the Equipment Procurement Process from Getting Grow Rooms Right, written by Geoff Brown, Quest’s VP of Technical Solutions and Dan Dettmers, Quest’s Applications Engineer.
Buying HVAC equipment can be a complex endeavor, and cost just one significant consideration. The investment does not end once the system is purchased, and to understand the true cost of HVAC equipment, cannabis cultivators must examine what it will take to operate and maintain that equipment over the life of the system.
Total cost of ownership includes installation cost, energy cost, warranty, serviceability and maintenance requirements, and a long-term approach is important when making purchasing decisions.
Whether cannabis cultivators are building new or retrofitting an existing building, it’s important to consider HVAC systems from the start, as everything from lighting to layout can impact which equipment is right for your grow. The following is an outline of the process and steps owners generally take when designing for cannabis production in new buildings and often for repurposing existing buildings:
1. The owner selects an architect to design or retrofit a building.
2. The architect hires an engineering firm to manage all facets of engineering.
3. The engineering firm may hire an HVAC specialist to design HVAC requirements.
4. The engineering firm/HVAC specialist invites representatives from the vendors to recommend HVAC solutions and propose equipment options.
5. Vendor representatives propose various solutions, price points and may require manufacturer support (few representatives are experts in all equipment lines they represent).
6. The engineer accepts a proposed solution and uses that solution to create their “basis of design” specification for the bidding process.
7. The general contractor is hired by the owner, architect or engineering firm to build the project, typically through a price-sensitive bidding process.
8. The winning general contractor solicits bids from sub-contractors specializing in various aspects of the job (another price-sensitive process).
9. The winning sub-contractor typically gets the job based on best price to supply and install the HVAC equipment that “meets the specifications” set out by the engineer. (Of note, there can be several vendors and several levels of quality that will technically meet specifications; the sub-contractor may be motivated to choose the lowest cost in order to maximize their profits.)
10. The winning sub-contractor typically must support the installed equipment for only one year after start-up. This short-term window of product support means the contractor may be less concerned with long-term product viability.
The key takeaway from this process is that there are two main hurdles that growers face. First, those involved in the process are often not grow room experts and therefore don’t always know the “right” equipment choice.
Second, the contractor who buys the equipment is often hired at a fixed price and may be motivated to procure the lowest-cost equipment that technically meets the engineer’s specifications in order to maximize their profit, which often does not offer the best value.
Although the word “value” can mean many different things to many different people, value when purchasing HVAC equipment should be evaluated based on the following factors:
1. Equipment purchase price: initial capital costs of equipment
2. Installation costs: ease of installation and related costs
3. Operating costs: energy consumption
4. Maintenance costs: regular maintenance costs and system risk mitigation
5. Repair costs: cost to repair or replace key components, including warranties or special extended service agreements
6. Lifetime of service: life expectancy of the equipment
7. Scalability: room by room expansion, facility growth, incremental stages
8. Reliability: likelihood of failure, ease of repair
9. Redundancy: built-in failover or multiple independent refrigeration circuits to prevent total failure
Another important tangible value of equipment is the impact it has on the grow; if selecting a certain kind of equipment can improve your yield and quality by just 2%, for example, what kind of value does that lend to the overall business?
Ultimately, growers own the equipment procurement process and can get what they want if they know how to take control of the situation.
For example, when the design team is assembled, hold an initial meeting to go over expectations for how the facility will function. Capturing details in writing is also a crucial step to ensuring everyone is working toward the same, clearly stated goals.
Growers should also ask many questions and ensure they are getting clear, accurate answers. Understand the reasons for certain recommendations and know all the options that are available.
Another crucial piece of the puzzle is asking engineers to explain the key competitive features of the equipment, including:
1. Solution Design: What kind of a system will be used?
2. Airflow: CFM to the room to ensure sufficient air changes (ideally x per minute or per minute or y per ton of capacity)
3. Duct and diffuser design: to ensure 100% optimal airflow and distribution to the room and canopy to match the CFM
4. Detailed load calculations: based on accurate lighting loads, plant densities, room conditions, ambient conditions, watering and transportation loads, etc.
5. Energy consumption: estimates based on specific design elements
Ultimately, designing commercial-scale cannabis grow rooms is still a new frontier and technologies are constantly changing. Getting grow room equipment specification right requires careful modeling of grow cycles, transpiration rates, temperature and humidity specifications, lighting loads and irrigations loads, as well as external factors such as annual temperature and humidity ranges and the type of building structure.
At the end of the day, choosing HVAC equipment is an investment in the health of the facility and business. While the variety of options on the market seek to do the same process, they do not all perform the same way, and performance of the equipment is what matters most.
Dan Dettmers is an Applications Engineer at Quest and its Controlled Environmental Agriculture division. Before Quest, Dettmers dedicated over 20 years to research and instruction at University of Wisconsin-Madison, primarily in industrial refrigeration for food and pharmaceutical processing. In his current role, Dettmers leads efforts to develop more efficient methods for handling latent loads and improving the air quality for cannabis and all controlled environmental agriculture operations. He is a contributing member to The American Society of Agricultural and Biological Engineers (ASABE) X653 guideline “Heating, Ventilating, and Air Conditioning (HVAC) for Indoor Plant Environments without Sunlight.”
Geoff Brown started his HVAC career over 15 years ago and has honed his expertise, dealing in every aspect of dehumidification throughout his career. Prior to his position with Quest, Brown was a senior sales manager and sales engineer, who consulted on and managed various successful dehumidification projects. As one of North America’s leading authorities on HVAC for grow rooms, Brown participates in various advisory boards in the cannabis industry and is a contributing member to ASABE X653 guideline “Heating, Ventilating, and Air Conditioning (HVAC) for Indoor Plant Environments without Sunlight."