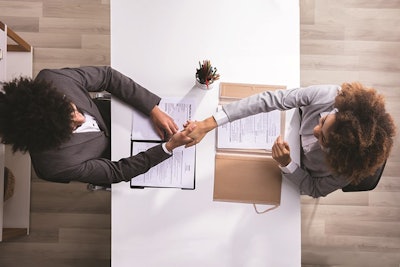
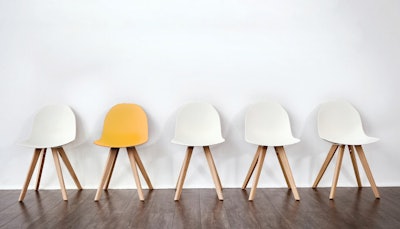
Hiring can be a daunting task for any start-up or expanding business, and this is especially true in the cannabis industry. Finding the right crop of people can be incredibly challenging for any hiring manager. When done correctly, staffing a cultivation start-up or expansion can result in a group of unified individuals who truly feel empowered to contribute to the success of the business. When done poorly, bad hiring decisions can lead to team infighting, delayed production and regulatory compliance issues.
In most early start-ups, a few individuals wear many hats, since there is not enough work to justify multiple new hires. But once the company starts growing, a number of critical positions must be filled to guarantee success. Consider the following six key hires when it’s time to begin sourcing your cultivation dream team.
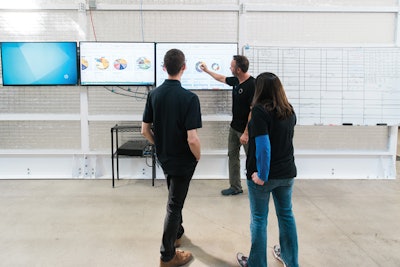
Director of Operations
The director of operations coordinates all of the moving parts of a commercial cultivation facility. This goes beyond just growing to include extraction, purchasing, shipping, security, retail and even human resources. The director of operations makes sure that all of these departments function in unison and move the entire company toward the same end goal. Due to its regular contact and influence in each department, this position helps create and promulgate the company culture across all functions of the production facility.
When searching for the perfect candidate to fill this role, don’t restrict yourself to the cannabis industry. Be open to considering someone with at least 10 years of experience managing operations for a manufacturing facility. Grow-ops and manufacturing plants have a lot in common, and these kinds of individuals can infuse valuable work experiences and lessons learned from other industries.
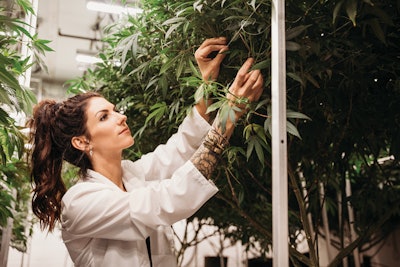
Master Grower
The master grower is the person who is 100-percent responsible for your cultivation program. Also referred to as the head grower or cultivation manager, this position is the single most important asset for any commercial cultivation facility. This individual draws on support staff and previous growing experience to turn a company’s cultivation goals into reality. They do this through crop scheduling, constant staff training and regular interaction with the crop. Master growers have an innate ability to “read” plant needs, which is a critical component in forecasting potential crop problems and resolving current plant issues. They also tend to be level-headed, rational thinkers that avoid any sudden changes in production that could risk affecting the entire crop.
While the ideal master grower should have experience cultivating cannabis, this is not a requirement. The most critical skill that he or she should bring to the table is commercial growing experience of any crop (preferably at least 10 years). In large, dynamic and actively expanding grow-ops, cultivating cannabis is only half the job. Balancing budgets, managing human resources and coordinating infrastructure maintenance are all tasks that can fall onto the master grower’s lap, and for cannabis growers inexperienced in these areas, the learning curve can be long and expensive for the company. (For a deeper dive into this critical position, see “How to Find and Hire the Right Master Grower,” in Cannabis Business Times‘ May 2018 issue.)
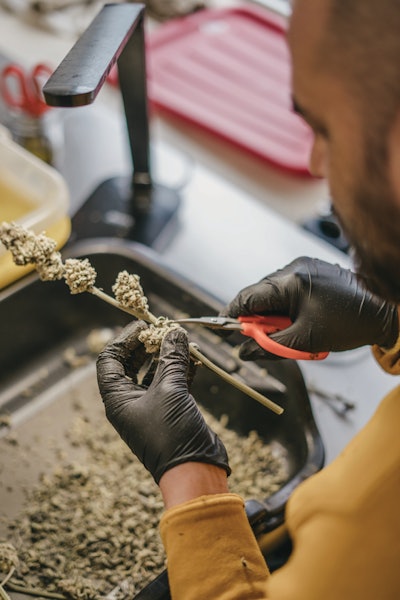
Section Grower
A section grower manages cultivation activities for a specific area of the grow facility. In greenhouses, this is usually defined by greenhouse bays, while indoor operations typically define sections by grow room. Section growers keep the company’s cultivation plan on schedule by guaranteeing that tasks like transplanting, pruning, spraying and harvesting happen on time within their assigned areas. They forecast labor needs and coordinate additional help when necessary, and alert the master grower to any anomalies in plant performance that could affect the outcome of the crop. Section growers are responsible for operating and maintaining the grow equipment within their respective sections, and they schedule repairs if they identify problems with lights, irrigation or climate control equipment.
Job candidates should have former cannabis growing experience, but if previous greenhouse work appears on their resume, that’s just as good. For cultivation companies with future expansion plans, section growers are usually first in line for promotion to master grower at the new site.
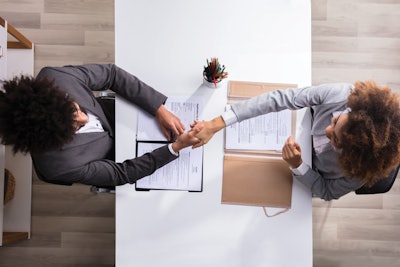
Plant Technicians
Plant technicians support the master grower and section growers by handling day-to-day plant maintenance and grow-facility cleaning. These individuals are the true labor force behind any commercial grow—they have a hand in every part of the cultivation process. As such, it is critical that plant technicians are properly trained on company protocols and the importance of compliance. A company may have impeccable cultivation standard operating procedures (SOPs), but if the individuals performing these tasks do not follow company protocols, it can result in unsalable cannabis or product recalls.
Ironically, when hiring for this position, a lack of cannabis growing experience can be a plus. This way, no one starts the job with preconceived notions of how best to grow. A stubborn home grower that enters the industry as a plant technician can slow down the cultivation process with constant debates or outright refusal to follow protocols, because it’s not how they like to grow. At the opposite end of the spectrum, new hires with no prior experience but that are interested in joining a growing industry can make the best plant technician candidates as they generally have a great work ethic and learn quickly. They are blank slates who can be quickly trained and put to work.
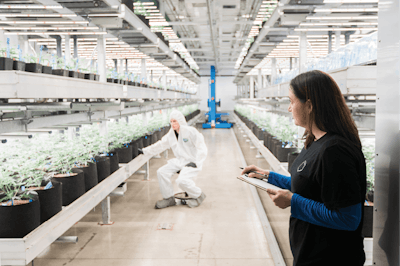
Post-Harvest Manager
The post-harvest manager is responsible for the finished crop once it is removed from the cultivation area. This hand-off of responsibility is common in large commercial operations, as it allows the cultivation team to immediately focus on cleaning and refilling a grow space after harvest. The post-harvest manager ensures that finished cannabis flower is trimmed, dried and cured to company specifications prior to being released for sale or sent to the extraction department (or processing partner) for further processing. They work closely with section growers to coordinate harvest dates and guarantee the availability of space and people to process the raw plant material. Post-harvest managers oversee the operation and maintenance of trim machines, as well as bulk packaging and labeling to ensure that dry flower is stored in a manner that won’t negatively affect quality.
When recruiting for this position, look for someone that is detail-oriented and computer-savvy. The smallest change in a dry room’s atmosphere can ruin the previous four months of growing, and computer skills are critical to managing the inventory tracking system that accounts for every leaf, seed and plant stalk that enters the trim room. Wet plant weight, dry flower weight and compliant destruction of unusable plant material are critical components in correctly tracking the production cycle from seed to sale. The post-harvest area also is one of the highest risk areas for weight discrepancies due to employee theft.
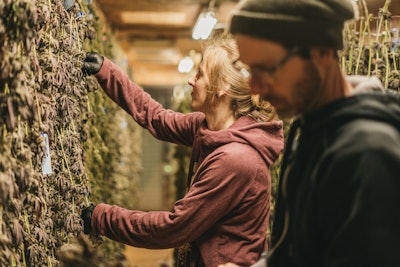
Trimmers
Trimmers are like soldiers on the frontline of quality control. Most commercial cultivators harvest on a weekly or bi-weekly basis, and trimmers are critical to the success of this final step in the cultivation process. Trimmers remove excess leaf from the harvested cannabis flower and help guarantee that the end product is visually appealing and smooth tasting. Leaving too much dry leaf on a cannabis flower can result in harsh taste and decreased medicinal efficacy, as well as poor presentation at dispensaries, unsatisfied retail customers, and the potential added expense of re-trimming a product. Trimmers are the company’s last defense against imperfections like seeds, mold or insects from entering the finished lot.
This job is the true entry-level position for anyone interested in entering the cannabis industry without prior cannabis growing experience. Trim work can be sporadic when there is no harvest, and monotonous when there is a large harvest. As a result, there is high turnover, and commercial operators are always hiring trimmers. When looking to fill your trim team, search for candidates that have a work history of performing repetitive tasks in less-than-glamorous environments. A room full of trim machines can be loud, and working with scissors eight hours a day requires relentless focus. Trimmers must constantly be aware of safety hazards in their work environment to avoid potential injury.
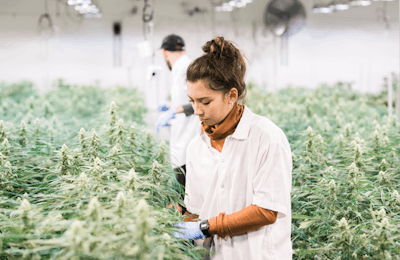
System Control Specialist
This is the techie on your grow team. This individual should have a special flare for understanding technology and the complexities of getting independent pieces of equipment to work together. This position supports the head grower and section growers by allowing them to focus on growing, not technical troubleshooting. From climate control equipment to inventory tracking systems, almost everything in a commercial grow facility is online, in the cloud or on your computer. When something breaks down or fails to perform as expected, growers can’t afford to stop everything, track down a user’s manual and spend the rest of the day troubleshooting. This is where the system control specialist comes to the rescue. They can usually solve the problem immediately, or they know whom to contact to fix the problem quickly, meaning minimum downtime for the grow team.
Look for candidates familiar with managing interdependent systems. Previous experience setting up HVAC systems, computer networks, or sound and audio equipment is ideal. Search for individuals experienced in scheduling regular maintenance of manufacturing equipment, or IT geniuses that are good with hardware installations, updates and repairs. These people often work at big-box stores installing electronics, so the next time they are at your house installing a new flat screen TV, you may just want to offer them a job.