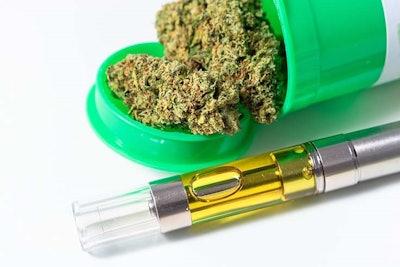
With a wide range of cannabis vaping hardware suppliers out there, it might be hard to determine which one to choose. It is increasingly difficult to identify which companies are reliable and which companies can consistently deliver high-quality, safe and compliant products. While certain technologies have been around for a while and/or have become well-known names, there is still a lot more to consider when purchasing your cannabis vaping products.
While everyone in the cannabis industry is familiar with the daily sales emails blasted out by international suppliers, most of those businesses aren’t really factories but rather just trading companies that resell products.
Based on the more than 10 years I spent in the vaping industry and more than five of those years in Shenzhen creating vaping products for nicotine and now cannabis, I suggest you ask your vaping hardware suppliers these top three due diligence questions:
Supply Chain: Do you control the entire supply chain (e.g. raw materials)?
Most of the factories that produce vaping products are actually assemblers; they don’t manufacture per se. They have suppliers that provide the metals, the ceramics, the plastics, the glass, the batteries, etc.
Here’s a true story without names: Leader Extracts (a fictional cannabis processor) buys 20,000 cartridges from Excellent Vapes (a fictional Chinese vape hardware supplier) on March 1. Leader gets its cartridges delivered on April 1 and fills them in a week. Since it is the leader and its extracts are the best, it quickly sell through 75 percent of its filled cartridges by May 1. It scrambles to order from Excellent Vapes another batch of 20,000 cartridges.
In the meantime, Suzy, a purchasing manager of Excellent Vapes, has identified a new supplier of ceramic that sells for 0.1 RMB (Chinese currency = US$0.015) cheaper than the previous supplier. She decides to place an order of 20,000 ceramic pieces from this new supplier in order to assemble this new batch for Leader Extracts.
On June 1, Leader Extracts receives the 20,000 pieces and starts filling orders right away because it already has a backlog of orders waiting. After selling these filled cartridges for a week, it realizes that one out of five of them leaks. Its customers quickly stop ordering, and Leader Extracts’ reputation takes a hit. In three months, it went from leading to failing.
After a little bit of investigation, it took apart a few cartridges of this new batch and realized that the ceramic in this new batch was a lot more porous; it had a higher void ratio. This caused the ceramic of the new cartridges to get saturated in oil after a couple of uses, therefore leading to leaking and spit-back. The company contacts Steve, its Excellent Vapes sales rep, and complains about the issue; but for Steve, these are the "same" cartridges. In the end, Leader Extracts decided to find a new supplier and had to throw away the entire filled batch as well as the packaging it had ordered for it, losing over $50,000 in the process.
How could this have been prevented? Here are a couple of solutions:
- Excellent Vapes should have tracking and quality control processes in place, which is not the case with most manufacturers.
- Suzy should have asked the new supplier for all the specifications of its ceramic and made sure they were the same as the previous supplier’s.
- Steve should have known about the change in supplier and should have informed Leader Extracts as well as provided a few testing samples to make sure they worked like the first batch.
- Leader Extracts should have done due diligence first and verified that Excellent Vapes has all the processes in place to identify potential batch inconsistency issues.
- Leader Extracts should have requested Material Safety Data Sheets and Specifications for the core components of its products.
- Leader Extracts should have had a process in place for internal testing on a certain number of cartridges from each new batch.
As we can clearly see, there are multiple points of failure in this situation that all point to the same need: control over your supply chain.
Can you imagine that all of this money was thrown away, all the time lost finding a new cartridge supplier and all of the missed sales and reputational damage that was caused by one person trying to save $0.015 per cartridge?
Unfortunately, since the factories in China don’t control their supply chain, and it’s a very long and expensive process for purchasing companies to do so, it becomes very hard to mitigate risk. This requires extensive relationships and due diligence to be done in Shenzhen and elsewhere on a regular basis.
Either do it yourself or work with a trusted partner with experience in vaping products.
Safety & Compliance: Is the safety and compliance of each product guaranteed?
When it comes to product safety with cannabis vaping products, the verdict is still out. We are using a product that we, as an industry, don't completely understand; we, as an industry, do not yet have long-term data at our disposal. Years of research will be necessary before we can truly comprehend and master the science of cannabis vaping.
Nevertheless, there are ways to mitigate safety, and this starts on the vaping hardware side. We’ve all heard about the Phase 3 testing that the Bureau of Cannabis Control in California created and started enforcing on Jan. 1, 2019. The main issue concerning hardware in this phase is heavy metals.
California BCC Required Lab... by sandydocs on Scribd
Although heavy metals can be present in the concentrate itself, through water, pesticides, soil, etc., they are also present in the hardware. The process by which they find themselves introduced into the extract is what we call “leaching.” Depending on properties like pH, some cannabis constituents can suck the heavy metals out of the devices; the user then inhales them through vaporization and finds himself faced with potential long-term health risks.
Many hardware suppliers, whether they are U.S.-based distributors, Chinese trading companies or even Chinese factories, say their products are “heavy metal free." This is hardly the case for multiple reasons:
- The most widely used and available alloy in China is H59, which contains lead.
- Cannabis is 100-percent illegal in China, therefore preventing any factory from doing any testing of the final product with cannabis extracts.
- Leaching happens over time, so you can fill a lead-containing cartridge with cannabis oil, test it within 24 hours and have it pass testing, but it may not pass the seven- or 15-day test.
So, how do you make sure that your suppliers use safe and compliant products? Here is a list of questions you can ask them:
- Can you provide long-term heavy metal testing certificates of analysis (COAs) for your products?
- Can you provide a list of the materials used in each product?
- Can you provide certificates of conformity for the products?
- Can you provide any if all of the manufacturing facility’s accreditations or certifications?
Andremember, the most important aspect about ensuring safety and compliance is to know the regulations in effect in the state/country where you will be selling these products.
Quality Control: How do you guarantee product quality and consistency?
Often overlooked, Quality Control (QC) is a very important part of the process when working with suppliers. It is important to rely on third-party QC experts in this industry or at least understand the process in place with your supplier.
I’m sure this has happened numerous times if you’ve been working with smaller or international suppliers in any industry: You order a product and approve the final samples and color, but when you receive them, the colors aren’t the same, or the manual isn’t present, or you’re missing a silicone cap. Any number of issues can arrive with your shipment.
When we’re looking at batteries, whether disposable or rechargeable, they often lack protection circuit boards (PCBs), and/or the provided chargers lack fuses or short circuit protections. These issues end up on the news when devices “blow up.” Now imagine that battery has your company logo on it; who do you think will end up getting sued? Certainly not the manufacturer.
This is probably one of the most overlooked aspects in our industry, so you should always ask your supplier what kind of QC processes are in place. Your supplier should be able to list them and provide examples and reports. You should at least be presented with a well-documented Quality Control report with detailed findings and photographs before finalizing your payment and before approving shipment. This is called a final inspection before shipment.
But there are also other various QC checkpoints, Here are a few:
- Incoming quality control (IQC) or Initial Product Check (IPC): Inspecting parts and materials chosen for a product, a process called incoming quality control (IQC), is an important first step in identifying any quality problems. Purchasers typically leave IQC to their supplier’s staff to perform, rather than visiting the factory themselves or hiring a third-party QC inspector for this purpose. If you’ve bargained your order price too low when negotiating with your vape hardware suppliers, don’t be surprised if they attempt to recoup lost margin on your order by using cheaper, substandard or non-compliant materials or parts.
- First article inspection (FAI): For some purchasers, the next prudent step in identifying product defects after IQC is checking some of the first mass-produced units. During first article inspection (FAI), an inspector will check one or a few of the first units of an order off the production line or a unit from the first production lot.
- In-process quality control (IPQC) and during production inspection (DUPRO): The next logical stage to consider is quality control inspection after FAI is when production is well underway. The two types of inspections commonly performed here are in-process quality control (IPQC) and during production inspection (DUPRO). The difference between these is that inspectors generally perform IPQC on semi-finished goods, while they conduct DUPRO on finished goods. DUPRO typically occurs when the factory has manufactured 15-80 percent of the total order quantity.
- Final inspection: The most common time purchasers choose to perform quality control inspection is when most of the goods are finished—typically 80 percent or more. Usually called final inspection, this represents your last opportunity to see the quality and condition of your shipment while it’s still in the factory. Many experienced QC professionals consider final inspection to be the bare minimum required level of product oversight.
The main key point here is that you need to make sure that you have a clear understanding of your supplier’s QC process.
Here’s a tip: The right suppliers will have you sign off on a final inspection report before billing and shipping. This is the main method to verify quality and consistency of the cannabis vaping hardware you are purchasing.
All of this may seem confusing or frustrating at first—but when selecting a supplier, these points are of utmost importance and will be instrumental in avoiding any issues down the line. As a final piece of advice: If and when you find a supplier able to provide all of the above, don’t nickel and dime them over a few cents per product as those few cents pay for the processes in place that provide you with insurance and are “future-proofing” your cannabis enterprise.