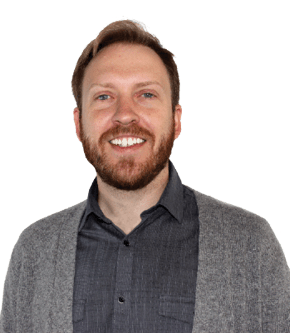
Chatting with industry peers often is a great way to get different perspectives on ongoing challenges and ideas about how to move forward. In this fast-paced Q&A, Brandy Keen, co-founder and senior technical adviser with Surna, speaks with the company’s lead engineer, Kenneth Loshelder, about what he sees as the cannabis industry’s greatest design and construction challenges. Loshelder, a licensed engineer who has been working in the HVACD industry since 2005 and is experienced in mechanical design and commissioning, energy efficiency, building controls optimization and LEED/sustainability consulting, also shares what continues to surprise him, and what excites him about the future.
Brandy Keen: What do you think is the biggest challenge during design and construction of cultivation facilities?
Kenneth Loshelder: The amount of self-inflicted pain on project teams due to poor planning. Although it’s improving as the industry matures, it really felt like the Wild West of construction when I started. There are thousands of decisions that are interconnected through several trades in any major construction project, and this is especially true in a cannabis facility with specialized systems and equipment. These decisions need to be made in the proper order with consideration of the entire timeline to achieve the desired outcomes with the least pain and money. Careful project planning and execution will pay itself back tenfold when it leads to desired outcomes on the first try.
BK: You’ve been doing this for a long time now. Do you still get surprised?
KL: I am still surprised by how little consideration is given to the HVAC system and its integration with the facility during early design decisions. Other than the building itself, the HVAC system is one of the most expensive components of the facility, and it has a direct impact on the heart of the operation. The value of the facility is generated in the cultivation rooms, yet, oftentimes, the racking and the climate control environment are the last items to be figured out. Cultivators are better served by starting with the needs of the plant, and then working from there to determine the best way to integrate critical systems into the facility design.
BK: What would you say is the most challenging aspect of mechanical design for cultivation facilities?
KL: The lack of industry standards and empirical data is a major challenge, especially for less experienced engineers. There are not many reliable sources to go to when you are working through a problem or considering a new approach. We continue to apply our experience to develop our own internal resources, and to give cultivators access to real data through our controls systems.
BK: What excites you the most about the industry and the work you’re doing at Surna?
KL: There is so much room for innovation! At Surna, we have our own opportunity to be a part of this evolution to push the envelope in terms of environmental consistency and energy efficiency. I am excited about our work to expand our offerings and educate our clients in several possible approaches for environmental control in cultivation facilities. We’ve put in a lot of time and energy to evaluate the various HVACD system approaches that work well, and to ensure we can offer a wide range of system types to meet the specific needs of each cultivator. In addition to that, the industry is increasingly seeing the value of energy efficiency, and we continue to focus on energy efficiency, energy models, and data collection to further our understanding of the operational costs of each alternative. The quality and value of our offerings continue to improve each year.