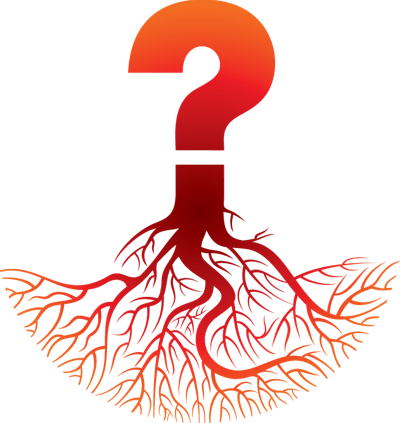
Expanding your cultivation business is no small feat, and the factors involved in the decision to expand and the process of doing so can be daunting and even risky if you’re not prepared. In Part I of this two-part series — titled “Successful Expansion of Your Cultivation Operation: A Pre-Construction Guide” — we addressed questions of whether or not you should expand, things to take into account while planning the process and designing your expanded facility, as well as legal and compliance considerations. In this column, we continue exploring how to effectively and successfully scale up, focusing on important issues to take into account in three key areas: Construction, staff preparation and management, and crop propagation.
Construction
To make the construction process go as smoothly as possible, do your homework on contractors you hire. Ask for and contact their former clients to gauge their performance on previous jobs. A bad contractor can delay your expansion by months or longer, leading to unplanned, skyrocketing costs. Establish a detailed timeline for construction with specific goals and deadlines to be met, so that progress can be monitored and evaluated. (Gantt charts, which illustrate project timelines and milestones, can be very useful for this exercise.) An independent project manager is ideal, if possible, so your cultivation staff can focus on their own tasks and an experienced professional can be focused on the construction project.
Now that the industry has been around for a few years, look to hire a contractor or company that has experience working with cultivation facilities. It helps immensely to work with someone who is aware of the unique challenges of working in a functioning grow. For example, we have seen electricians, unaware of the importance of not interrupting the light cycles of flowering plants, enter dark flower rooms with normal flashlights, interrupting flower development and causing hermaphroditism. On the other hand, we have worked with very conscientious HVAC companies, with experience in the industry, who asked for the light schedules for flower rooms up front and planned work accordingly. If you can't find contractors or project managers with sufficient cannabis experience, consider hiring an industry consultant versed in these issues to coordinate planning and communication between your staff and any contractors.
As always, compliance concerns remain at the fore. In Colorado, for example, be sure your contractor knows that only people age 21 or over can enter cultivation facilities. Colorado regulations also require that contractors sign in as visitors, and visitors must be escorted by an employee with an MED (Marijuana Enforcement Division) occupational license, commonly known as a “badge,” at all times.
Be sure contractors are aware of issues affecting their safety, such as observing re-entry intervals (REIs) after pesticide applications, alert systems in case of excessive carbon dioxide levels, and any hazardous or combustible materials, such as extraction solvents.
Communication and information are key. Identify, up front, as many potential issues as possible and convey them to your contractors, along with written instructions on facility schedules (for both staff and plants), procedures and necessary steps for compliance.
Even with the best preparation, however, there will be disruptions and unanticipated costs. For example, the facility's power may need to be turned off to finish an electrical upgrade, or perhaps the Internet will intermittently be down, in addition to more mundane possibilities such as drywall dust or paint getting onto plants. Things will happen — there are too many moving parts for any project to go completely without incident — but detailed preparation, deliberate management, and effective communication can help smooth over the speed bumps that can arise.
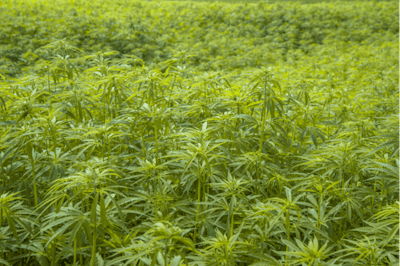
Staff Preparation and Management
Once expansion is complete, you will require additional staff, and almost certainly a reorganization or restructuring of staff. This should begin to be addressed well before construction is completed. While smaller grows can be run effectively by just a few employees with general responsibilities, anyone attempting to do so on a large scale will quickly realize that more structure is required to achieve the desired productivity and efficiency.
Carefully consider the work that will be required in your expanded operation and define staff hierarchy and responsibilities. Write formal job descriptions and standard operating procedures (SOPs). It is difficult to anticipate exactly how the expanded operation will run, so don’t worry about formulating roles and responsibilities perfectly; job descriptions and SOPs can be amended. Additionally, defining responsibilities and positions ahead of time will allow you to interview potential new hires more effectively and better evaluate existing staff for new roles.
Determine if any existing staff are realistic candidates for management positions. An employee can be exceptional in his or her current position, but that is not necessarily a reliable indicator of success in a management role. You may be required to make tough calls in terms of promoting newer staff members ahead of more experienced ones, or bypassing existing staff altogether. Be prepared to deal with frustration and hurt feelings, but know that you have to make the best decisions for your business.
Bringing in new, high-level employees can raise other issues as well. We have seen so-called “master growers” hired to run commercial facilities, only for them to show that, while they may be amazing small-scale cultivators, they cannot manage a large operation effectively. This emphasizes the importance of having strong SOPs in place. The best person to manage your operation might not necessarily have the greenest thumb, but they need to know how to communicate effectively, coordinate staff, stick to schedules, execute procedures and evaluate where and when changes are necessary. Having set protocols also protects against the contingency of a master grower abruptly leaving his or her position and taking his or her “secrets” with them.
Smaller operations often use temp harvest and trimming services, or simply have the cultivation staff chip in on those tasks. However, in a larger facility, harvests are more frequent, and the volume of product to be trimmed increases greatly. Once you have scaled up, having your own full-time trim and harvest staff is essential. First, it will save you money, as temp staffing companies charge more per hour for each worker to cover administrative costs. Dedicated staff also generally are less likely to steal. Second, it will allow you to train your staff according to your procedures and goals. It also will help mitigate the threat of a temp worker bringing pests in from another grow he or she worked in recently.
All staff should be trained on in-house procedures pertinent to them, in addition to providing any specific training or certifications required by law. To use Colorado as an example once again, Environmental Protection Agency (EPA) Worker Protection Standard training is required for any employee who will be working in spaces in which pesticides (including organic) were applied within the previous 30 days. A Private Pesticide Applicator License from the Colorado Department of Agriculture is required for individuals who apply the pesticides.
Finally, cultivation on a commercial scale is hard, repetitive work. Taking care of your staff with small amenities such as providing beverages and occasional lunches can help keep morale high for a relatively low cost. Constructing comfortable common areas is important; no one wants to be eating lunch while sitting on an upside-down bucket as construction workers operate a jackhammer nearby. Introducing performance-based incentive programs can maximize productivity and employee engagement. Consider such items when determining how to structure and organize staff. For example, splitting your employees into teams that are responsible for certain tasks or individual rooms can create friendly competition and additional motivation to perform well, while also being an efficient, effective way to delegate responsibilities.
Propagation
Once construction is winding down, new staff have been brought on and trained, and everyone is excited to get growing, you had better have plants prepared to fill all your new rooms. Otherwise, your expansion could sit empty for weeks or months, delaying your return on investment. It also does not help to “steal” from yourself, by filling new spaces with plants intended for other rooms or plants not yet at an ideal size to flower.
To prevent such situations, an expanded propagation plan is necessary. If you haven’t already constructed a regular schedule of which strains are to flower in which rooms, you should do this during planning. The schedule also should include when the plants are to be cloned and from what plants the cuttings will be taken. There are a number of different ways to go about this, including cloning from mothers and cloning from your vegetative plants themselves, and the ideal approach will be contingent on a number of variables unique to your facility and the varieties of cannabis you are growing.
When it comes to propagating additional plants for your new expansion, identify the strain or strains you would like to propagate. Set aside enough mother plants of those strains to provide the desired number of cuttings so that they may be taken when the time is right. Again, communication with your contractor is important, as timelines may shift. It should also be noted that, depending on existing veg space, your construction timeline may need to first address expanding clone and veg areas to ensure that adequate space is available for additional plants to be propagated. Since you should always be cloning more than you ultimately need, remember to design a veg space that will hold at least 125 percent to 150 percent of the amount of plants you will flower.
One thing that should hold true across the board concerns strain evaluation and selection: Just because you will have more cultivation space after expansion does not necessarily mean you need more strains to fill it. In fact, to ensure a timely, reliable ROI, propagate strains that have historically performed well in terms of yield, pest resistance and quality. If you haven’t yet identified such strains using record keeping and data analysis, start as soon as possible. The “eye test” only goes so far, and we have seen cases where a strain that seemed to perform well based on a grower’s impressions was actually just middle of the road, or worse, when hard data was collected, broken down and examined.
Proper strain selection also will help staff focus on becoming accustomed to the new spaces and procedures, as the plants they are cultivating will not become problems requiring extra attention and labor; existing staff members will be familiar with the strains and able to provide guidance to new employees.
If you are already growing, you know that dialing in your cultivation approach to a new strain can take several harvests, and you don’t want to do that kind of trial and error while attempting to quickly recoup a multi-million-dollar investment (and any sizable expansion will absolutely run into the millions of dollars). Seasoned growers also have probably experienced what could be considered the worst-case scenario: the introduction of pests into a facility via the cuttings of new genetics. Imagine your new, expanded crop taken down by mites just because you wanted to add a trendy strain you are not even sure will perform well. If new genetics must be brought in, implement strict inspection and quarantine protocols to isolate cuttings until it can be determined they are clean.
Planning Will Go a Long Way
As you can see, scaling up your operation — or going from small-scale home cultivation to commercial production — is not as simple as just hanging more lights. It involves the coordination and cooperation of dozens of outside parties, from architects to security providers to city inspectors to utility companies, and many more in between, not to mention a refashioning of internal structures, procedures and staff. Rigorous planning and preparation at the outset will go a long way toward avoiding costly headaches throughout the process. In extreme cases, expansion projects can even end up killing a business, which, of course, is the exact opposite of the intended result, and the type of Growing Pains that this column is designed to help you avoid.
Nic Easley is the founder and CEO of Comprehensive Cannabis Consulting (3C). A decorated veteran of the U.S. Air Force, Easley established a 35-acre organic farm in Colorado after completing his military service, and has degrees in biology and environmental studies. Over the past eight years, Easley has consulted with more than 60 clients in Colorado and formed 3C to bring organic, sustainable cultivation solutions to the world. Adam Koh is the Chief Cultivation Officer for 3C. Previously, he served as cultivation manager of a Denver-area medical cannabis facility that was awarded the High Times Cannabis Cup for Best Medical Hybrid in 2014. Koh has experience cultivating more than 100 different strains, including numerous high-CBD varieties, and in his previous position oversaw the care of roughly 3,000 plants at any one time.