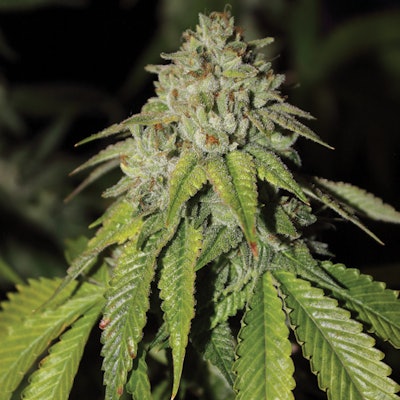
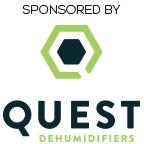
Theoretically, cannabis should be as easy to grow as a weed, considering the plant’s nickname. In the real world, cultivating high-quality, biosynthetically-grown (or, a hybrid organic) marijuana as a for-profit business is anything but easy, according to The Herbal Cure’s lead cultivation technician, Don Newman. The Denver-based medical and recreational cannabis grower and dispensary is a recent winner of six first-place awards for traits such as flavor, yield and potency.
Like many growers, The Herbal Cure cultivates cannabis in buildings that had to be retrofitted extensively to meet legal cultivation standards. An ample budget allowed the company to build an optimal environment for indoor cannabis cultivation. “A lot of cannabis growers operate in older warehouses that constantly need to be fixed and updated,” Newman says. “When you do that, you’re always kind of chasing your tail.”
Odor control is a big issue—one they tackle by operating in sealed rooms. In a marketplace where product prices are on the decline, however, it can be challenging to control the climate of the sealed, organic environment while maintaining profitability. “At the end of the day, cannabis prices are dropping, so having your i’s dotted and t’s crossed will determine who remains standing,” Newman says.
Conditions That Combat Humidity
Essential to profitability is making sure every plant is healthy. As plants absorb water and nutrients, they transpire (more so in higher temperatures) and can create a very humid environment that may welcome black mold, powdery mildew and pests. The Herbal Cure wards off such threats with fastidious climate control, using 110-pint dehumidifiers that help maintain 40-percent to 50-percent humidity. The goal is to create such a healthy environment that plants can defend themselves against almost anything.
Newman says commercial cannabis growers must be vigilant about conditions that create microclimates, such as a room set for 60-percent humidity and 78 degrees. “In that microenvironment, where leaves overlap and lay atop one another, there is no light, there is 100 percent humidity, and there’s a lot of extra heat-the perfect environment for mold spores to take hold.”
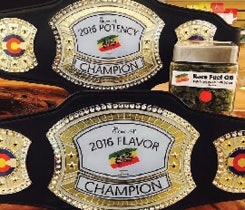
Good pruning can prevent such problems. When plants reach the flowering stage at The Herbal Cure, they are pruned until there is only one node on each branch. The idea is to create airflow beneath the canopy and prevent microenvironments. Pruning also forces a plant to direct all its energy into top growth where it gets the most light.
Newman believes in following recommendations provided by Vapor Pressure Deficit (VPD) charts, which prescribe the right humidity and room temperature during vegetation and the first three to four weeks of flowering. (Vapor Pressure Deficit measures the difference between the moisture level in the air and the amount of moisture the air can hold. Temperatures come into play since warmer air can hold more moisture than cooler air. Cannabis plants will try to cool themselves in warmer temperatures through transpiration, which further increases the moisture in the air.)“When you start to see buds form and good resin production, drop your humidity down to 40 to 50 percent,” he says. “Anything above that encourages powdery mildew. Anything below it encourages downy mildew.”
Newman says the principles of humidity control are simple: If humidity is too low, moisture is drawn from the leaves, which stresses the plant. Too much humidity can ruin THC production. Plants may grow vigorously, but the resin content won’t be desirable. In a perfect environment, the humidity in the air is matched to leaf humidity, producing robust growth.
Drying and Curing: A Crucial Point for Humidity Control
Controlling humidity also plays an important role in drying and curing—a process that can make or break a cannabis crop. “If you don’t have enough humidity, your flowers are going to dry too quickly, locking in moisture and chlorophyll,” he says. “You’ll get a harsh smoke that has no flavor.” On the opposite end, too much humidity promotes bud mold or rot, which can wipe out an entire crop.
Through trial and error, The Herbal Cure has developed a curing formula that Newman says delivers consistently good flavor and smoke: Harvest the plant, remove the largest fan leaves and hang it for 14 days at 65 degrees and 60-percent humidity.
Simple Principles to Follow
Newman says cannabis thrives when growers follow simple, well-honed cultivation principles, such as maintaining 40-percent to 50-percent humidity, avoiding cross contamination and making sure water has the right pH for plants to absorb nutrients. Veer from that path, and you start to have issues.
“At the end of the day, people often try to put their own spin on it, create their own version of cannabis cultivation and claim it as their own,” he says. “But really, if you just follow basic guidelines, you’re going to have a successful run, and you’re going to be a great grower.”