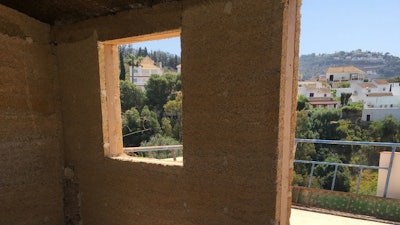
How many of us think about the quality of building materials used in our homes? This is a question that’s driving the interest in the hemp building industry in Europe and North America.
That was also the motivation for Stephen Hill and Marjolein Meulblok, a couple based in the south of Spain, when they decided to rebuild a derelict Spanish farmhouse using raw hemp materials. In 2020, they launched The Hempcrete Project after years of searching for the right location to build a durable home for their family.
Hill and Meulblok met 15 years ago in La Herradura, Andalucia, and today the couple has five kids. They’ve lived in rental accommodations since they met, but for the last few years, they have been researching alternative ways to live that are more connected to nature–and may even avoid the burden of a 30-year mortgage.
Due to their backgrounds, sustainability and self-sufficiency are important to Hill and Meulblok. Hill grew up on one of the first organic farms in the United Kingdom, where he gained an in-depth knowledge of agriculture. Since 1980, he has specialized in making hand-made guitars, and still teaches the craft to students around the world.
Meulblok is a Tibetan yoga and reflexology practitioner with a deep interest in self-healing practices. Together, they’ve run organic farming workshops in La Herradura, where they learned about permaculture (a sustainable and self-sufficient approach to land management) and how to live in harmony with nature. They knew they wanted to infuse their knowledge of sustainability and self-sufficiency into their next home.
La Herradura is also home to beautiful beaches. But as scenic as is the region is, its coastal location brings high humidity inland, which has a major effect on the structural integrity of buildings over time and makes homes built with concrete extra cold in the winter and extra hot in the summer.
This was another factor in Hill and Meulblok’s decision-making process. In keeping with their sustainable goals, they also wanted a to create a house with a stable temperature, powered only by solar panels.
Meulblok says she also looked into tiny houses and container living options, but none of those seemed like they would suit her lively family. After countless hours of researching, she discovered that homes could be built using hempcrete or hemplime, which is mixture of hemp hurd with a lime-based binder that creates a “monolithic wall system,” according to the Carbon Smart Materials Palette, to be used as a material for construction and insulation.
In 2020, they eventually purchased an old cortijo (farmhouse) in the hills behind La Herradura and decided to reconstruct it using hempcrete.
Hands-On With Hemp
The house they bought was built in 1936 and had a floor space of 88 square meters (947.2 square feet). It was originally divided into two parts: a living space in the front half and stables in the back. They converted the whole space into a home by knocking down the stables and adding a second floor to the back part of the house.
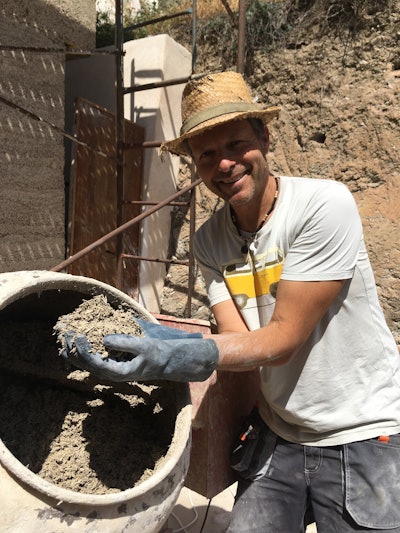
To fully insulate the house, they began the rebuild from the foundation up and re-rendered the old walls and built new walls with a hemp and natural hydraulic lime (NHL) mix. Hill explains that people often use concrete to restore the walls of old homes, which can trap moisture and cause damp problems.
They removed the concrete render from the old 50-centimeter-thick walls and converted it back to the original stone. They then re-rendered it with NHL and hemp shiv mix.
“What this mix does is allow the walls to breathe, as well as [adds] a layer of insulation and [prevents] any future issues with damp[ness],” Hill says. They used shiv and lime manufactured in France, and lime bought locally from Cannabric.
Over the course of several months, they dug up the foundation by hand, digging about a foot into the ground. They created a new foundation with a mix of stone, lime and hemp.
“First, there’s a sub-base of gravel and that prevents ground water rising up into the foundation,” Hill says. “Next is a breathable waterproof membrane, and that’s topped with expanded clay aggregate, which controls humidity. On top of that is about 15 cm of hempcrete mixed with sand, and on top of that again is 3 cm of hydraulic lime, sand and water, which seals the floor. The final skin is a special Moroccan skin called 'Tadelakt,' which gives the floor a smooth finish and can be dyed any color.”
To build the walls at the back of the house, they used a process called hand casting. To accomplish this, Hill and Meulblok built a wooden support structure for the walls and laid a foundational plinth at its base made with local rock and thermal brick, about 14 centimeters high. “The hemp cannot be placed at ground level because with heavy rain the splash will seep into the walls,” Hill says.
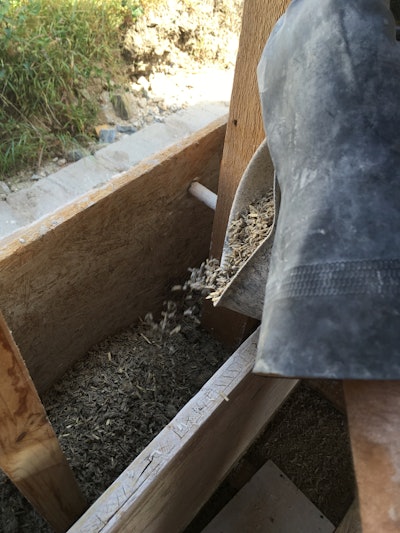
To create the hempcrete for the walls, they mixed shiv, NHL and water in an old cement mixer. To build the walls, they placed shutter boards on the interior and exterior of the wooden frame, creating a gap the width of the wall, and about a foot high. They poured the hempcrete mix into the space and left it to dry for over 24 hours.
“I use[d] a piece of plywood to tamp down the outer edge of the hempcrete, nice and firm, which creates a hard outer skim that can be rendered,” Hill says. “Without tamping down the hemp, the final walls can be flaky, so this is an important part of the process.” The next day, they moved the shutter boards up another foot and repeated the process. The renovation project has cost them around €50,000 (or $53,628 USD).
Even though Hill’s and Meulblok’s project is not yet finished (they have another six months of work to compete the job), the difference in air quality inside the structure is already noticeable. Not only is it comfortably cool despite the heat of the midday sun, it has a cozy feel, like stepping inside a sound studio, one that breathes.
Hemp Building Challenges
Projects like this are happening across Europe today. With the right materials and practices, homes built with hemp have a low- or zero-carbon footprint, good thermal performance, stable temperature and higher indoor air quality.
Tom Woolley is an architect based in County Down Northern Ireland and is a special adviser on the board for Hemp Cooperative Ireland. He’s been building with hempcrete for 20 years and has hosted workshops all over the world. His firm built the Rediscovery Centre in Ballymun, an outer suburb of Dublin.
In the last year, he’s noted a greater interest in hemp from local community projects and “individual people who want to build the best way they can,” he says.
He also highlights challenges the hemp building industry is facing in the UK. One issue is hemp’s reputation. Back in 2014, British TV presenter Kevin McCloud of Grand Designs hosted a show about building with hemp. At first, the show stirred interest, but ultimately “did a lot of damage,” he says.
“They used the wrong materials and [the houses] weren’t built correctly,” Woolley explains. “Even though the design was nice, it spread throughout the construction industry that hemp was ‘bad news.’” Woolley sees resistance from the construction industry as one of the biggest hurdles for the hemp-building sector in Europe and North America.
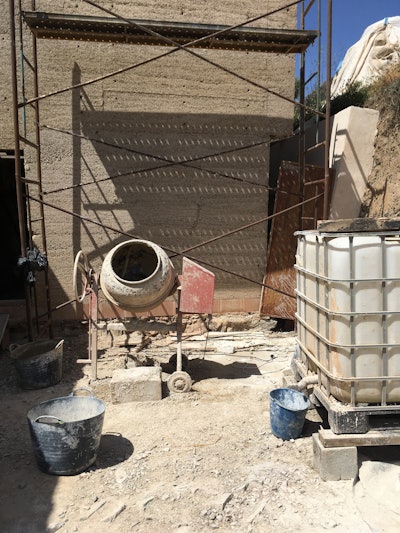
He also adds that unsuccessful hemp construction projects can give a wrong impression of working with hemp, noting photos of a home in Devon, England, (built with hemp-based materaisl) with mushrooms growing out of the wall. “When there’s too much fiber in the mix, it can rot,” he says. And he warns against using the wrong kind of hydraulic binder.
“If there’s too much cement in the binder, the hempcrete becomes too dense. It then takes a lot longer to dry and doesn’t have the thermal performance of low-density hempcrete,” he says, referring to its ability to retain heat.
He also stresses the importance of using “clean shiv”—the interior stalk of the hemp plant, also called hurd—meaning it contains minimal fiber and is dust-free. For Woolley, a failed hemp construction project is usually due to the use of “the wrong part of the plant or the wrong binder,” he says.
But this is still a “cottage industry,” he says, and things are improving, with good suppliers emerging, such as East Yorkshire Hemp in the UK, as well as others in France, Italy and Lithuania.
Building a Hemp-Building Industry
Woolley is waiting for someone to make a breakthrough by landing a contract for a large housing project in Europe and notes that could help advance the hemp building industry there. This is a sentiment shared by the European Industrial Hemp Association (EIHA) and the U.S. Hemp Building Association (USHBA).
“Bio-based construction is gaining interest, and we see traditional construction companies acquiring hemp companies or showing an interest in their own line of hemp products,” says Francesco Mirizzi, senior policy adviser at the EIHA. “The ideal evolution of industry is the integration of bio-based hemp products by the construction industry.”
There are companies dedicated to using hemp as a building material. For example, IsoHemp in Belgium is a construction company that makes hempcrete blocks for residential homes. “The company has doubled the size of their facilities in the last year,” Mirizzi says.
In addition, there are industry initiatives such as the GRACE project, which is a consortium made up of 22 partners from academia and the bio-based industry throughout Europe, to cultivate hemp crops that can be used in industrial-scale production.
However, according to the EIHA, the lack of decortication lines in Europe is a problem. Right now, there are only 12 on the continent, with six located in France. Mirizzi calls this “a lost opportunity” that results in supply chain issues. Without a processing industry, agriculture farmers have no incentive to grow. “The sector needs investment,” he says.
Another problem, according to Mirizzi, is the price of hemp, which is higher than conventional products, like cement. However, he believes it “will be less of a problem in the future because nothing else compares on energy performance.” He also sees a need for training, to give builders the knowledge to “build homes that breathe,” he says.
Hemp’s Sustainable Impact
Despite the challenges, industrial hemp hubs are growing in France, Italy, Germany, Poland and Lithuania, and the same thing is happening in the U.S., according to Jacob Waddell, president of the USHBA. With more processing factories opening up near growers, the beginnings of reliable supply chains are taking shape.
“What makes sense are localized markets,” Waddell says. “Right now, we’re importing goods from overseas to use in building. But long-term, we see companies coming in and establishing hubs in the U.S. What’s being imported is the technology.”
There are also companies innovating technology in the U.S.
HempWood is a Kentucky-based company that specializes in hardwood flooring made with hemp. They’ve overcome the problem of not having a decorticator by adapting old technologies from other industries.
They also use a modified drier from the tobacco industry to dry out the fiber and source all their materials locally.
Waddell sees HempWood as an example of a localized system signaling the future of the industry. “Between 2009 and 2015 there were a lot of one-off innovative projects but now, there’s a mind-shift. What’s happening now is we’re figuring out how to make these products available to everyone,” he says. More recently, he’s seen interest from large chains such as Lowes and Home Depot in carrying hemp products.
“While there’s no question, building with hemp by hand is great for one-off projects,” says Kiko Thébaud, a Massachusetts-based architect and adviser on the Cape Cod Hemp House project. Thébaud has spent years researching low-carbon products for the construction industry and says he sees mass insulation with hemp as a way to battle environmental problems.
“The construction industry is responsible for 40% of carbon emissions in the U.S. alone,” he says. “Using hemp is a way to counteract that damage and create beautiful homes, and it can be adapted to local needs. For example, because it’s fire resistant, it makes sense to use it in California. That’s just one of its many benefits. Really, we have no time to lose.”
Based in Spain, Natasha Kerry Smith writes about cannabis trends, and tackles taboo topics on her blog, The Healthy Hashhead. She’s currently working on a collection of poetry and a book project, both inspired by cannabis. Find her on LinkedIn.