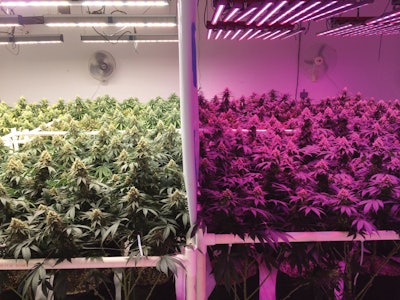
Dave Spillman, owner of High Mountain Health in Arizona, is an engineer by education, and he challenges his cultivation practices with a scientific approach. To test the efficiency of LED lights against his traditional high pressure sodium (or HPS) lights, he transitioned three of his 12 grow rooms to an LED setup.
“We put LED lights in and measure the heat they put out. We [also] measure the light they put out,” he says. “We have just collected every bit of data since we started this facility. I’m a data-collection geek.”
After several rounds of testing, “We’ve seen remarkable results,” he says. “We haven’t seen any loss in weight or yields with LED compared to our single-ended HPS rooms.” Coming to the end of a test with similar results in both groups sounds like wasted effort, but for an engineer like Spillman, it has changed his outlook.
“We operate with a triple bottom-line,” says Spillman. “We really look at what we’re doing socially, what we’re doing environmentally and then what we’re doing as a business.”
Spillman says he sees more even canopy development in the cultivation rooms with LED lights, letting the whole canopy ripen at once. That efficiency in growth helped them take an extra week off of cycle times.
With HPS, he also has to replace the bulbs every third cycle, as opposed to LEDs, which will “probably last me 12 years,” he says. He has used a kilowatt calculator to compare the energy usage to break down the cost per cycle between the rooms. In his single-ended HPS rooms, that number comes to $1,836 per cycle. In the LED rooms, the cost of electricity per cycle is $954.72, he says.
“We’re saving half our electricity right there,” he says. “That’s what my CFO wants to see. … They want to see those numbers.” That cost doesn’t include cooling, of which rooms equipped with LEDs also require less, he says.
“I’m directly replacing a 1,000-watt fixture that has two fans and a cooling load attached to it,” with a 650-watt LED fixture, he says.
Comparing results from his current grow rooms that have already transitioned to LED versus his traditional double-ended HPS rooms, Spillman reports a grams per watt yield increase of 101 percent.
“We’re seeing a doubling of efficiencies there,” he says. “I’m getting much better per watt. … I’m getting more power out of it.”
For an even larger test, Spillman split up a grow room into two halves, separated by a light-deprecation barrier to keep light from penetrating from either side, testing different LED lights to compare crop results. With that setup, “I’ve been running mirror studies,” he says. “So, same strain, same mother, same amount of veg time. Everything equal on both sides of the divider.”
Aside from the regular grow areas in his 15,000-square-foot-operation, he also runs test bays where he sets up experiments with new equipment.
These numbers are meaningful for Spillman because he’s counting on energy efficiency to help cultivation continue to grow, even as the cost for energy rises, he says. “[For] all my growing partners across the nation that are running into capacity issues, the capacity of how many amps you delivered to your building creates a finite number of how many pounds you’re going to put out of your facility.” Power upgrades from the utility will eventually have to cap, and then, he says, “the only way to increase your production then is to get more efficient lighting, right?”
Efficiency aside, Spillman relies on data to help him make the best choices for his business, and has been branching out to test light setups from different manufacturers. But that’s only part of the data he records throughout his grow.
“You can’t manage what you can’t measure,” he says. “From the time we take a clipping off a clone, there’s a track of that plant as it goes through our facilities.” Spillman works with his manager to test new ideas in cultivation within the boundaries of designed experiments. After they reproduce results several times, they can go back to the data to see what has worked best to develop the best blooms.
That helps him keep strains from slipping, he says, and allows him to find extra efficiencies in his cultivation.
“All that data is [a tool] for us to use,” Spillman explains. “I want us to reduce our carbon footprint, as a collective [industry]. I really feel strongly about it, so I share all the data. … If we want to be embedded into the mainstream with a positive image, we can’t be doing things that are negative to our environment. We’ve got to try to step with our best foot forward.”