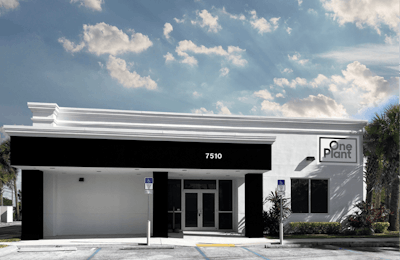
Multistate cannabis operator Cresco Labs announced Jan. 14 that it will acquire Bluma Wellness, a Florida-based, vertically integrated company, in a transaction that company executives say combines two like-minded companies with similar business models.
The acquisition places Cresco in 10 total U.S. states and advances the company’s overall goal of developing a strategic geographic footprint based on desirable regulatory structures and population, Cresco CEO and co-founder Charlie Bachtell tells Cannabis Business Times.
The acquisition is “the culmination of a multi-year evaluation of how to get into the Florida market the right way,” Bachtell says. “We wanted to make sure we [entered the market] in a very thoughtful and appropriate way, and Bluma really presented that perfect opportunity for us, so we’re really happy with it.”
Bachtell describes Cresco as a traditional, consumer packaged goods-focused organization with a “product-first” approach that prioritizes the creation and distribution of branded products into as many retail stores as possible. This differs from other companies’ retail-first business models, he says, which prioritize the opening of as many dispensaries as possible.
“Bluma is arguably the only operator in Florida that thinks about the industry similarly to how we do,” Bachtell says. “They focused on production first, and then they opened very strategic, very thoughtful retail locations as they had product to sell.”
As a single-state operator, Bluma has been looking for a multistate company to partner with in order to expand nationally, especially as cannabis policy reform efforts begin to take shape at the federal level after the 2020 election, says Bluma CEO Brady Cobb.
“You see with the presidential election results [and] the Senate races in Georgia, it was time for us to find an MSO and a partner to be able to expand and be able to take advantage of this opportunity at the federal level that we’re seeing,” Cobb details.
Bluma’s CEO says his company had a lot of suitors looking to enter Florida’s market, but that Cresco emerged as the best partner, “based on their culture [and] their focus on having the best flower and best premium products in any market that they operate.”
“They invested like we did in building out cultivation and … manufacturing so that you could have quality product, and then [focus] on retail,” Cobb says. “Once we had a chance to meet them and see how great of a cultural fit it was, too, it was a no-brainer, and we can’t be more excited to go on this ride with them.”
Bluma currently operates seven dispensaries under the One Plant Florida brand, with eight more locations planned. The company also has 54,000 square feet of cultivation space, with a planned expansion of its cultivation capacity, processing lab and edibles kitchen.
Cobb says that it will be business as usual for Bluma following the acquisition, although the company has a lot of work ahead to expand its cultivation, manufacturing and retail footprint.
Cobb is looking to close the deal by April 1, 2021. “Then, it’s building the expansion of our cultivation facility. We’re looking at doing a large indoor facility at our existing farm, and then also building out a manufacturing house where we can do a full post-harvest process—dry, cure, trim, dry packaging, a full edibles kitchen, a full concentrates lab, full hydrocarbon lab, distillation lab. Getting all of those projects done in 2021 is a key goal, and getting us up to 15 stores is a key goal.”